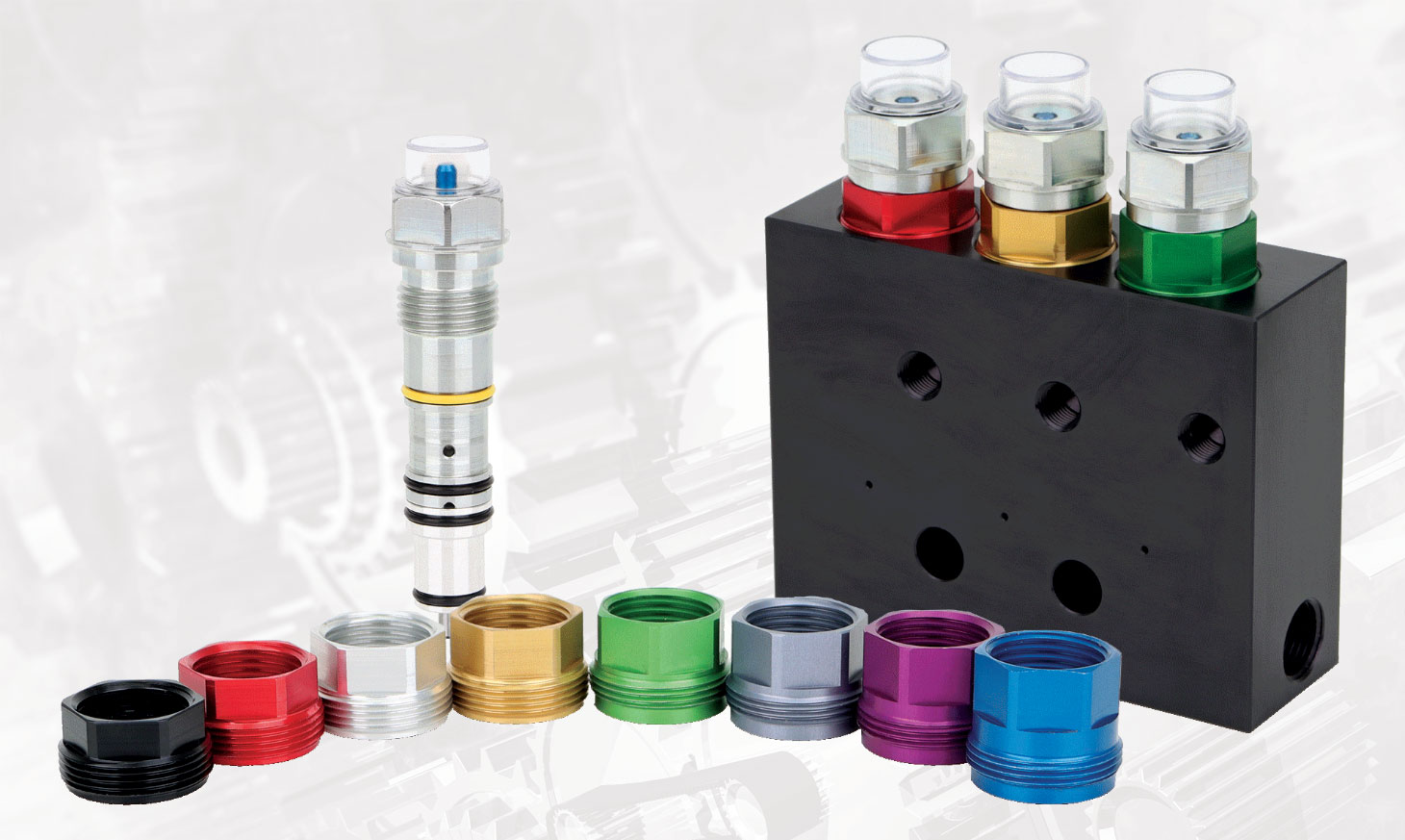
In 1926, Russell and Leil Gray fumbled with a manual grease gun in freezing Minneapolis temperatures that turned grease into a thick sludge. Thinking there had to be a better way, Russell came up with an air-powered, portable lubricator while working as a parking lot attendant.
The brothers ran with the idea and opened a store later that year to sell their new lubricator. That idea has since led to the creation of Graco Inc., which supplies technology and expertise for managing fluids and coatings in industrial and commercial applications.
“Our division is the founding division of Graco, so that’s something that we like to take a bit of pride in,” said Shane Norman, Graco’s global product marketing manager for the lubrication division. “We’ve been innovating in lubrication ever since. We’re strong in products found in service centres or maintenance shops that would be used to service the equipment in the piling industry.”
Their products are used in machines that prepare foundation work, such as excavation equipment and dozers. The lubrication products are often used when this large-scale equipment requires the 250- to 500-hour maintenance schedules. To assist with this maintenance, the company also offers pumps, hose reels, meters and fluid management systems that can track every drop of oil to ensure the end users are putting the correct oil into the proper crankcases.
Norman says this equipment can benefit from technologically advanced solutions when it comes to greasing, and there has been plenty of research and development into automatic lubrication products. The demand for automatic lubrication has increased since it was introduced more than 80 years ago.
“The automatic lubrication system market is going to grow significantly over the next 10 years.”
Shane Norman, Graco Inc.
“A lot of workers don’t want to pick up a grease gun every two or three hours to grease equipment and then go back to work or to refill hard-to-reach lube points on some pieces of equipment that aren’t very safe to get to. That’s where automatic lubrication comes in because it provides a much safer and more efficient use of everybody’s time and money,” said Norman.
Through automatic lubrication systems, grease is placed into a lube point at a designated time or cycle intervals to flush contaminants and maintain proper lubrication. This process allows workers to spend time on more productive tasks on jobsites and extends the life of the bearing or lubrication point. Further development and refinement of automatic lubrication systems is a priority for Graco, and Norman says demand for these systems will continue to increase.
Automatic lubrication systems
“The automatic lubrication system market is going to grow significantly over the next 10 years, specifically for two reasons: There is concern about safety and the lack of available workers to do the work,” Norman said. “In every industry, downtime is critical. With an automatic lubrication system, especially Graco’s newest product we’re launching, we’re focused on making the intervals longer between any failure or downtime. And once the service is required, we want to make it as easy and seamless as possible to get back to work.”
As the industry has changed, Graco has emphasized simplifying its oil and grease automatic lubrication systems. In 2018, it launched a new controller with Bluetooth capability to make it easier for either a distributor or end user to see the parameters of what is taking place within the system directly on their phone. This enables them to program the pump or download diagnostics directly from that controller via an app.
Graco has also launched new pumps over the last few years, focusing on integrating components that historically have been separate in the main pump casing. This innovation will not only make the components more compact, but it will also make them easier to service.
Another recent innovation has been the launch of a new set of injectors. Two different systems are available for dispensing grease to lube points. One is a series progressive system in which the grease travels through each metering block in a series, so one point has to dispense before the next point can dispense. The other is a single-line parallel-based system, so the main line is pressurized and once the injectors reach a certain pressure, grease is injected into the lube point.
“Since the injector space hasn’t had any innovation since the 1940s, the injectors on the market today look and feel the same as they have for decades. We took a step back and considered all the key stakeholders and what really impacts their jobs,” said Norman.
Servicing injectors
Injectors are usually replaced every one to three years, depending on how much the machine is used and how clean the grease entering the automatic lubrication system is kept. When an injector has to be changed, it usually takes two hands to do the job and about 15 to 20 minutes to complete because so many components and grease lines need to be removed.
“When we went back to the drawing board, we made a working section for our new GCI cartridge injector platform that is plug and play,” said Norman. “It’s just a threaded connection, so we can take out the old cartridge with an impact wrench and put in a new working section in less than a minute, and you are back up and running again. The additional benefit is that it’s a lot safer to do this since it only takes one hand, and you don’t have to spend as much time underneath the machine in cramped spaces where they mount the injectors.”
“Our division is the founding division of Graco, so that’s something that we like to take a bit of pride in.”
Shane Norman, Graco Inc.
He says manufacturing processes have also improved, so the new injectors have tighter tolerances and better surface finishes. It also provides about twice the lifespan of current injectors.
Graco products are currently sold through distributors and original equipment manufacturers. The company has online content and YouTube videos to assist with product use, and relies heavily on training its distributors so they understand how to install and service their products and perform any troubleshooting. The distributor usually works closer with the end user to ensure they get the most out of the products. After almost 100 years in business, Norman says Graco expects to continue being an innovation leader for another century.
“We’re going to continue to focus on efficiency improvements – whether it’s with the pump itself or on any other aspect of the system – but we are also going to focus on how we can get more data around automatic lubrication and vehicle service maintenance type products. We want to provide good insights for the end users so they know exactly what is going on with the systems. We want to make lives better and less complicated when it comes to lubrication.”