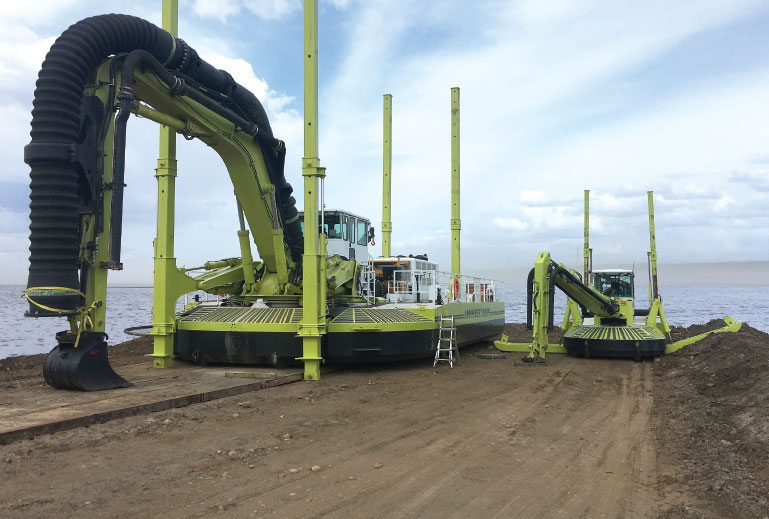
Norm Grant and his family manufacture portable dredges named Amphibex that have many functions and are sold all over the world. The company, Normrock Industries, is based on innovation and constant response to what the market needs.
Norman Grant says he was “born between a piston and a crank shaft.” The fifth child in a family of 12, and the oldest boy, Grant was born in the Matane area of Quebec and raised in Ville D’Anjou in eastern Montreal. His father was a mechanic, and Grant spent his childhood years in mechanical pursuits, which became his trade when he reached working age.
“It was common sense that I would be in fabricating, repairing and building because that was my father’s trade,” he said.
He operated and repaired equipment in Northern Quebec, Newfoundland and other areas of Canada before joining Overseas Consultant Services, a U.S. company, as a consultant. While on a job in Africa, he became interested in environmental, floating excavating equipment. “We were doing work in water with excavators on barges, including rock breaking,” he said.
Because of problems that occurred, he saw a need for creating the right equipment for these activities. Upon his return to Canada, he purchased a small Finnish machine which was too small for the job, so he built his own machine, which was the Model AE300 Amphibex, a combination of the words “amphibious excavator.” The vessel was capable of suction dredging and mechanical excavation, including rock breaking.
In 1987, he formed Normrock Industries, Inc., based in Terrebone, Que., to produce environmentally friendly machines for dredging and other on-water jobs. Over the years, he has developed eight more Amphibex models, all with the same capabilities, each one proportionately larger than its predecessor. Grant explains that each new model was the company’s response to the changing market, and to what the customers needed.
Working with him are his wife, Louise, and sons, Dany and Jimmy, who serve as vice presidents and equal partners in the business.
Performance and environmental protection
The overriding goal of the dredge designs is protection of the environment. “Since we began in 1987, Normrock has believed that performance and environmental protection go hand-in-hand,” said Grant.
This goal plays out in “the way we fabricate the tooling,” he said. “The horizontal dredgehead doesn’t disperse the underwater silt. We have different accessories that are designed to contain silt, such as the environmental (clamshell) bucket that closes completely. We use biodegradable hydraulic and other oil, and for power use hydraulic diesel drive. One engine does everything, and the fuel tank is inside the dredge – a tank within a tank – so there’s no possibility of an oil spill,” he said.
Attachments include horizontal cutterheads, backhoe buckets, an effective closed environmental bucket with hydraulic opening and closing, rakes and rock breakers, to name a few. Capabilities include aquatic weed cutting and harvesting (widely used in Africa), excavating and dredging, trash and debris collection, laying pipeline and underwater cables, marina maintenance, beach refurbishment, contaminated sediment handling and removal, and preventive ice breaking on rivers before the spring run.
“Every day we get new applications,” said Grant. New tools are designed as the need arises.
A standard cutterhead working in aquatic weeds and debris can end up fouled with massive amounts of vegetation. Grant’s response to this problem was the Conical Cutterhead, in which an outer casing only allows entrance of small material through to the rotating cutterhead, sloughing off the weeds and debris.
In response to a need by a Russian customer, Normrock is creating a pile driving attachment for use by the two largest models – the AE850 and the AE1200 – to be delivered this year. “It will be quite fun,” said Grant. “It will pick up the piles and drive them,” while moving easily around the project site.
Machines are self-launching
The Amphibex vessels are self-propelled and equipped with four tilting spuds for stability while dredging and to self-launch the dredge. Two outrigger stabilizers are equipped with floats that steady the dredge while underway and while working. They can be tilted to the bottom as another leg to provide extra stability while the excavator is in use. In shallow water, the dredge can work while resting on the bottom.
A quick connection system allows the rapid exchange of tools and attachments.
The AE1200 is the newest model, and is six times as large as the smallest model – the AE400. It is 60 feet long by 28 feet wide with a dredging depth of 38.5 feet, equipped with a Caterpillar C32 diesel engine that generates 1350 bhp (1007 kW). The other models are the AE450E, the AE600E, the AE650E, the AE800P, the AE850P and the AE1000P.
The AmphiTransports – the AT300 and AT430 – are workboats that can transport equipment to the dredge. Each model includes a removable hopper for transporting dredged material, aquatic weeds or debris. The hoppers are easily transferred to trucks for transportation to a placement site.
Normrock has a 50,000-square-foot manufacturing facility in Terrebonne, Que., with an additional 85,000 square feet under construction.
A second manufacturing location, at Marine Inland Fabricators in Panama City, Fla., provides Amphibex equipment to the U.S. market. Grant sold six units to government agencies for use in enclosed water bodies prior to obtaining a certificate of Jones Act compliance in 2013, which opened his U.S. market to projects in navigable waterways.
Grant describes his market as “all over the planet.” He rattles off a short list of locations where he has delivered machines – China, New Caledonia, Ivory Coast, Nigeria, Mauritania, Russia, Latin America, Mexico and the U.S.
Far-reaching markets
Grant has been selling machines to the Iraq General Directorate for River Dredging Works for many years, and has 27 machines there, with several of each model he manufactures. They are all working permanently in the Tigris and Euphrates Rivers and tributaries, where an annual sediment load of 30 million cubic metres per year is deposited, and must be removed to prevent flooding and for navigation.
“We aren’t in the contracting business,” said Grant. “When we operate a dredge, it’s either to demonstrate it or to perform specialized work.”
An example of such specialized work is at the Alberta tar sands project, where 16 Normrock employees are on site with two machines – an AE1200 and AE400 equipped with horizontal cutterheads – under contract to Syncrude. “This was an experiment that went very well,” said Grant. The Amphibex proved to be ideal for the work.
The tar sands operation includes settling ponds for storing the water, debris and particulates from the oil separation operation. Some of these ponds are now being remediated. The liquid is pumped to separation stations, and the bottom of the ponds completely cleaned of all foreign material in preparation for filling with the original soils and planting with the original flora.
“When we leave there, it’s going to be clean,” said Grant. “Nothing left.”