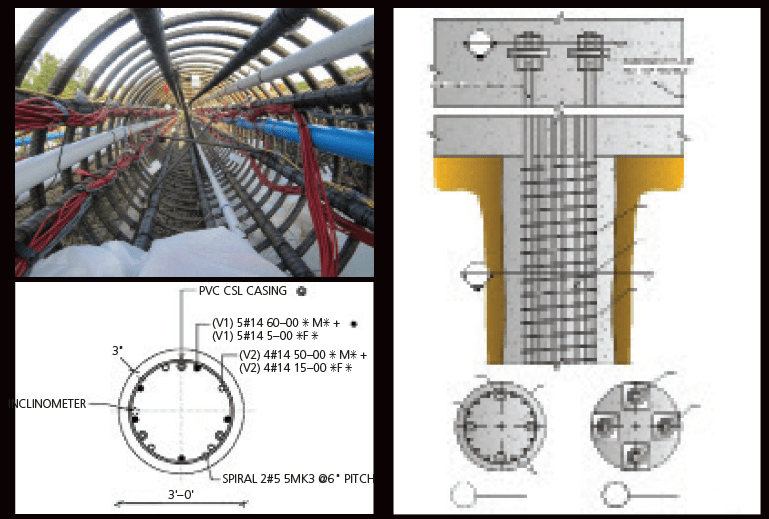
Due to the possible de-bonding problem of smooth entry tubes with concrete for crosshole sonic logging (CSL) in many drilled shaft projects, test results can be wrongly interpreted. Unnecessary and costly remedial work is often conducted.
The Hollow Bar system, originally introduced by Con-Tech Systems in North America, for grout injection bored IBO, soil nails and micropiles, turned out to be an ideal hollow rebar solution to solve the de-bonding problem. As an additional bonus, tests have shown that replacing standard rebars with the hollow bars used for CSL will produce a much more rigid and stiffer rebar cage, making handling and placing into the drilled hole faster and safer.
This paper explains the development of this new method for non-destructive integrity testing (NDT) of drilled shafts. Actual full-scale tests have proven its validity.
Introduction
The present method used is lowering CSL probes into drilled shafts through non-structural PVC or steel pipes, Figure 1. These pipes, when incorporated within the reinforcing cage, reduce the space between the vertical bars, hindering a good flow of concrete to the outside of the cage with possible creation of anomalies. Also, smooth pipes have a de-bonding problem in concrete. For CSL testing, the read-out values could be misinterpreted. For Thermal Integrity Profiling (TIP), the thermal wires are tight to the vertical rebars. The thermal wires or probes could be damaged during handling, placing of the cage and placing of the concrete.
The new method
Hollow rebars offer high-strength, very ductile reinforcement – a requirement for seismic designs – while also providing an access tube and larger spaces between the vertical reinforcing bars, allowing better concrete flow and cover.
The high-strength hollow rebars, well known for self-drilling or grout injection bored IBO, soil nails and micropiles, have thread type deformations in accordance with ASTM A 615 requirements for standard rebars. They provide good bond and adhesion with the concrete, eliminating the problems of de-bonding associated with non-structural access tubes made of smooth PVC or steel pipes during CSL testing.
The overall cage stiffness is also increased by the large, three-inch diameter, hollow rebars, Figures 3 and 4, making transportation and installation much easier and safer. Using these hollow rebars also as a conduit for TIP wires or probes provides good protection and eliminates any damage to the TIP probes.
Since the hollow bars are filled with water – for placing CSL probes – during placement of the concrete to eliminate buoyancy, further research is necessary not only to test the concrete for internal anomalies with CSL, but also to test the extreme outside condition with the TIP probes inside the water filled hollow bars. Both CSL and TIP probes could then be withdrawn for further usage, making the test not only much more economical, but also more complete over the entire cross-section. Otherwise the TIP probes can be grouted inside the bars at the time the concrete is placed.
The following outlines the NDT conducted at Oregon State University under Professor Armin Stuedlein, PhD, with the assistance of Bernard Hertlein, senior consultant for CSL and TIP. Figures 5 and 6.
During this experimental program on four drilled shafts to determine the effect of high strength steel reinforcement bars on lateral resistance, TIP, thermal wires and CSL access tubes were installed in each shaft and the corresponding NDT was performed on each shaft to assess the integrity of the shafts and to compare the results from the different NDT methods.
The results of the CSL tests using scored PVC tubes are compared against those conducted in the 73/56 (outside/inside diameter in millimetres) fully threaded hollow rebars in shaft (HRIS) in Table 1.
The results indicated that the hollow rebars served as a good host for performing the CSL tests. This paper can serve as a reference to those interpreting the measurements and data obtained by performing NDTs on drilled shaft foundations.
For the HRIS shaft, three No.11 bars were substituted with 73/56 hollow fully threaded Grade 80 (552 megapascals or 80 kips per square inch yield stress) bars that provided both the necessary structural requirements and the access for CSL testing. To prevent the intrusion into the hollow bar of drilling fluid and/or concrete during construction, the base of the hollow bar was capped with a welded steel plate. The CSL testing was performed in general accordance with ASTM D6760 (ASTM 2014a). As shown in Figure 7, significantly cleaner signals were produced for the CSL tests performed using fully threaded hollow rebar access tubes compared to the tests (in red) that used roughened PVC access tubes, resulting in improved clarity.
These results indicate that there are no barriers to use hollow rebars in both structural applications and quality control. In addition, the locations of prefabricated voids that were used for mounting the hydraulic actuator
for the lateral loading tests and a known planted anomaly were identified by the CSL measurements more clearly with the hollow rebars.
Hollow bar micropiles with inside strain gauges or TIP wires
In grout injection bored hollow bar micropiles, TIP wire probes as well as strain gauges can be installed into the grout filled hollow bars. Terracon installed strain gauges inside Titan 40/20, 52/26 and 73/53 hollow bar micropiles at two projects in Las Vegas, Nev., (Figures 8 and 9) to monitor load transfer during testing and construction.
See typical load transfer curves in Figure 10.
For another project Terracon placed TIP wires inside hollow bar micropiles to verify the required actual grout cover and anticipated diameter of the piles (Figures 11 and 12).
According to Terracon, while load tests on micropiles are generally performed on one to two per cent of the production piles, the ease of TIP testing allows for inspection coverage of 10 to 20 per cent. It can be performed relatively easy and is another valuable and innovative method to determine proper micropile installation.
A new patent has been applied for, for the use of hollow rebars, replacing pipes for post-grouting the base or tip of drilled shafts, improving load carrying capacity and also decreasing their length.
Post-grouting the base or tip of drilled shafts refers to a variety of practices related to the injection of grout under pressure below the tip of a drilled shaft foundation to improve the resistance of the shaft to top-down loading when subjected to compressive axial load. The grout may be neat cement grout (e.g. Portland cement and water). Post-grouting is accomplished using a grout delivery system that is incorporated into a drilled shaft during construction.
The grout delivery system generally includes tubes or pipes that pass from the top of the shaft to a grout distribution apparatus located at the tip of the shaft. When adequately instrumented and properly monitored, the post-grouting process has been proven to provide increased load capacity compared to conventional (non-grouted) drilled shafts, since the process provides a measurable indication of performance.
However, providing the additional pipes is an additional expense that adds to undesirable congestion of the steel reinforcement cage used for the drilled shaft foundation. Furthermore, once post-grouting is complete, the pipes used for post-grouting provide no structural contribution to the drilled shaft foundation and are a relatively inefficient component.
Accordingly, it is desirable to provide a more efficient mechanism for using a post-grout delivery system of a drilled shaft foundation and replace the pipes or tubes with hollow rebars.
Summary
This new method using hollow rebars for NDT of drilled shafts or micropiles will eliminate all previously experienced problems which caused unnecessary expensive repair costs and provides more accurate reliable test results. As a bonus, the large diameter hollow rebars (e.g. 73/53) replace standard rebars and contribute to a stiffer drilled shaft rebar cage for safer handling and placing into the drilled shaft. An additional bonus is using the same hollow rebars for post-grouting the base or tip of drilled shafts, which increases the load capacity and can shorten their length.
References
Armin Stuedlein, Professor, School of Civil and Construction Engineering, Oregon State of University, Corvallis, OR., 2016 Deep Foundation Institute., Comparison of Non-Destructive Integrity Tests on Experimental Drilled Shafts.
Bernhardt H. Hertlein, FACI, M.ASCE, Senior Consultant – NDE & Geophysics, GEI Consultants, Inc., Vernon Hills, Ill.
Bill Wright, P.E., Terracon Consultants, USA. 2017 ISM Vancouver. Micropile QA//QC Using Thermal Profiling.