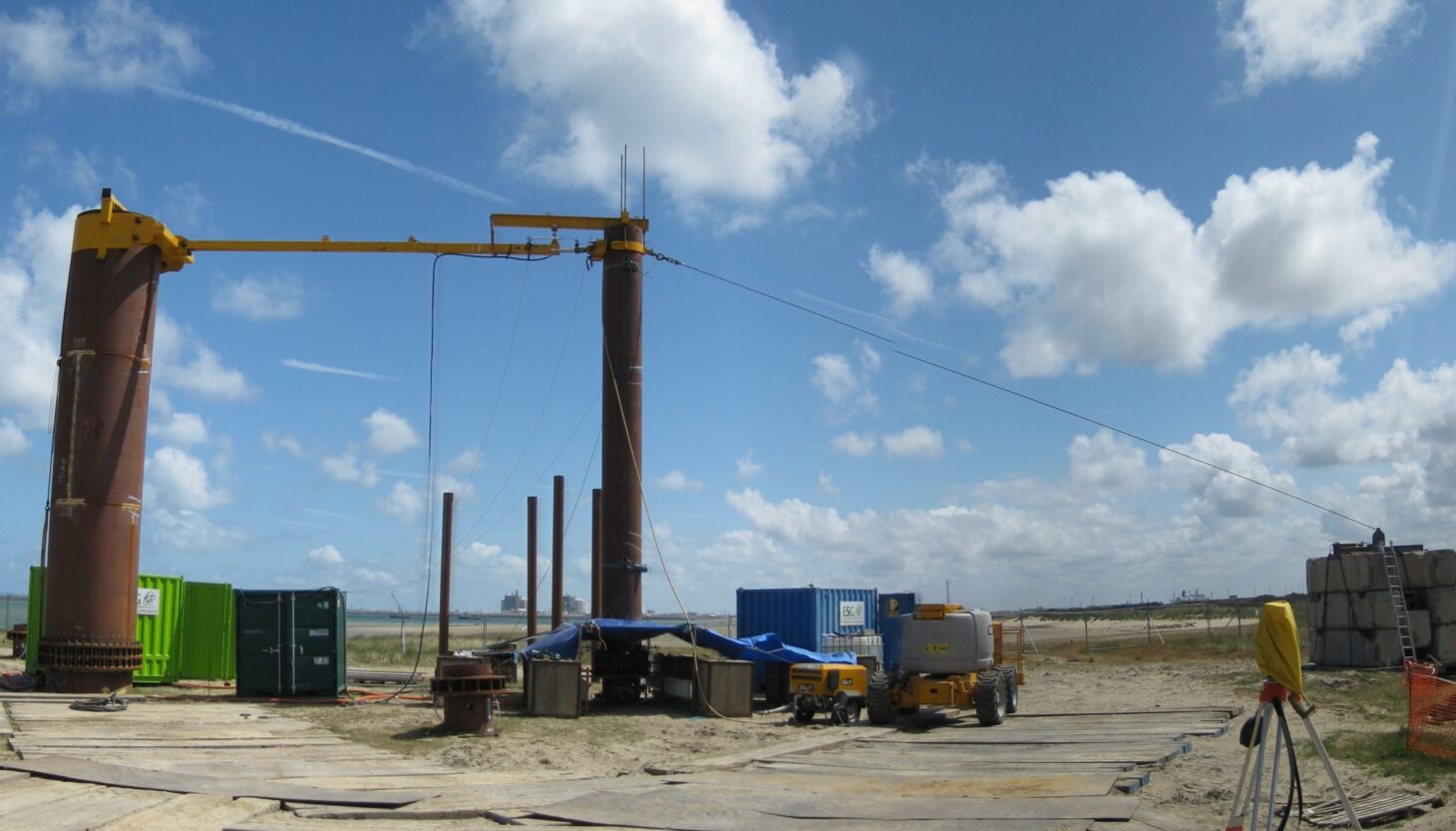
A simplified computational model of monopile foundation design for offshore wind turbines, developed through the recently completed Pile-Soil Analysis (PISA) JIP, marks an important step in advancing green energy. However, the approach could also be applied to other foundation and soil structure interaction problems within the piling industry.
Professor Byron Byrne, Ørsted/Royal Academy of Engineering Chair in Advanced Geotechnical Design at the University of Oxford, was the principal investigator for the Carbon Trust/Ørsted/Industry-funded PISA project that developed the model. He spoke during the 4th International Symposium on Frontiers in Offshore Geotechnics’ New Design Tools for Laterally Loaded Wind Turbine Monopiles webinar in May. He described the rationale behind the research project, how it was conducted and the exciting results.
“The rate of progress of offshore wind turbines in the U.K., since the first two 2-million-watt (MW) turbines were installed in the early 2000s, has been substantial, about 2,815 to date,” Byrne said. “That equates to 15 gigawatts (GW) of produced energy, with ambitious plans to install another 1,100 turbines, equating to a further 15 GW of electricity in the next five [or] seven years. Not only in the U.K., but across the rest of the world, industry is looking toward wind farms for a renewable supply of energy to power the future.”
This drive for sustainable energy has resulted in substantially larger and more wind turbines being built further offshore in deeper waters. However, as Byrne notes, this requires ongoing development of engineering design skills for different types of structures, water depths, turbine sizes, and seafloor soil and environmental conditions.
Monopile foundations
“There are a number of foundation configurations for offshore wind structures, but monopiles are often the favoured choice as they are relatively easy to install, have a strong supply chain, and are particularly suited to shallowish water and strong soils,” Byrne said. “Monopile foundations are large-diameter, steel tubes with current designs around 10 metres in diameter, impact-driven into the sea floor, anchoring the wind turbine structure above. They were considered to be suitable only for shallower waters, with other construction configurations such as jackets and floating structures used further from shore.
“Not only in the U.K., but across the rest of the world, industry is looking toward wind farms for a renewable supply of energy that will power the future.”
Professor Byron Byrne, Oxford University, Ørsted
“But since, say, 2015, especially because monopile foundations are less expensive to install, designers have been pushing the envelope to try to use them for deeper water and bigger wind turbine sizes.”
The PISA Project
Taking the approach that this was an industrialized design problem, the PISA Project industry consortium was led by Ørsted and a further 10 partners, including several key European wind farm developers. The scientific work was undertaken by an academic work group led by the University of Oxford, working with Imperial College London and University College Dublin.
Byrne says that the area of design interest for the research project was to determine the monotonic load-deflection response necessary for sizing the pile, mainly to ensure the pile doesn’t fail under substantial environmental loading conditions.
“In addition, we must be able to predict the foundation-structural stiffness under service loading, as that relates to the natural frequency of the structure, and be able to tune that frequency to avoid any substantial excitation frequencies. The model also needs to be sufficiently flexible to capture ground conditions that vary considerably across a large site and allow for each foundation to be optimized in terms of length, diameter and wall thickness.”
The research team looked for a simplified soil structure interaction design model that would allow for the many calculations needed to optimize wind farm foundations. “The basis for much of the work was to bring advanced computability into the heart of the design process, with a simplified one-dimensional (1D) finite-element approach, calibrated by more advanced 3D numerical calculations,” Byrne said.
The research process
Four elements comprise the research approach: advanced numerical modelling, simplified engineering models, medium scale field testing and accurate response prediction. Numerical modelling carried two main purposes: to help design the medium-scale field testing and pile testing to prove the hypothesis underpinning the design methods. The two sites chosen for the testing had soils like the North Sea: one with stiff, glacial clay till and the other featuring dense sand.
“The tests and systems were designed based on the results from our advanced numerical modelling,” Byrne said.
The field testing, led by Ørsted, involved 28 pile tests across the two sites. The main piles were 0.76 metres in diameter, buried up to five metres in the ground. Smaller piles at 0.27 metres in diameter were tested along with two piles with diameters of two metres and lengths of 10 metres for the main validation tests – large piles for experiments, but small-scale compared to offshore wind turbines. Extensive instrumentation data obtained throughout the testing and fibre optics delivered exceptional detail on the load responses on the piles.
A second objective was to use numerical modelling to develop simplified engineering modelling and better understand failure mechanisms in monopile foundations. “From the research, three soil reaction components were identified for monopiles in addition to the standard p-y component: a distributed moment down the pile, and a base shear and base moment,” Byrne wrote in Géotechnique Vol. 70, No. 11. “These components allowed for improved representation of soil-pile interaction behaviour.”
The test results provided great confidence that advanced numerical modelling can be used as a tool to determine soil structure interaction behaviour, particularly monopile behaviour
“From that base, we developed the PISA Design Model, a 1D model developed, calibrated and validated by means of 3DFE results,” Byrne told Piling Canada. “It is an enhanced p-y model in the sense that we have a distributed lateral load. In addition, we have some shear stresses being developed on the walls of the pile, which lead to a distributed moment, and also a shear force and moment at the pile base that can be taken into account.
“The basis for much of the work was to bring advanced computability into the heart of the design process, with a simplified one-dimensional finite-element approach, calibrated by more advanced 3D numerical calculations.”
Professor Byron Byrne, Oxford University, Ørsted
“As the pile diameter increases, some of these components become more significant, and as the length of the pile increases, some of these components perhaps become less significant. The modelling process demonstrates that for long piles, a (modified) p–y approach may be suitable for design, whereas, for large-diameter, relatively short monopoles, the p–y approach alone cannot predict the response reliably.
“We did many 3DFE calculations for our calibration process, spanning a wide range of an appropriate parameter space, for example, looking at large diameter piles up to 10 metres in diameter and 30 to 50 metres in length. From these calculations, we systematically extracted information that could be normalized and parameterized to develop the simplified model.”
Byrne says that the work demonstrated that monopile response was not well captured by the conventional p-y models, with the new advanced PISA modelling approach capturing the behaviour more closely, allowing for greater optimization of the foundations. This has led to the potential for substantial savings regarding the pile length – around 35 per cent – bringing some clear economic advantages to adopting a more sophisticated design approach.
Testing in layered soils
“Phase two of the PISA Project moved to a wider range of soil configurations as well as layered soils,” Byrne said. “After discussions with our industrial partners, we arrived at maybe five or six different cases involving multiple-layered systems. Our hypothesis was that soil reaction curves calibrated using homogeneous soil profiles could be employed directly to conduct 1D analysis of monopiles embedded in a layered soil. If you have a layered soil profile, you use the rules for the various individual materials in the calculations.
Current and next-generation wind farms are the power stations of the future, generating multi GWs of electricity for domestic and commercial use. An offshore wind farm now typically consists of 100 or more 9 MW turbines across sites covering many hundreds of square kilometres within a range of environmental and geological conditions. Driving down the capital costs for the installed offshore turbines is central to executing the longer-term evision, requiring advanced engineering to address mass production design coupled with location-specific optimization.
“In the vast majority of layered cases, the 1D model and the 3DFE calculations were very closely matched, indicating the proposed hypothesis was accurate. The layering didn’t appear to impact any of the initial stiffness calculations, but there were some differences in ultimate capacity for a small number of cases with more significant strength contrasts between soil layers. These cases would need to be further explored using more sophisticated numerical techniques.”
Following the project, in collaboration with PLAXIS, the research team with Bentley Systems developed the PLAXIS Monopile Designer incorporating the entire process into a commercial piece of software validated against the experimental results from both the test sites and output from different phases of the PISA Project (www.bentley.com/en/products/product-line/geotechnical-engineering-software/plaxis-monopile-designer).
And furthermore
“The story doesn’t finish there,” Byrne said. “There are, of course, more complex effects not captured that will need to be explored eventually; for example, we observed in the field tests some rather substantial loading rate effects. And whilst these new approaches have been developed specifically for monotonic loading of monopiles, to allow site-wide optimizations, the next step is cyclic loading, which is now the focus of efforts across the industry.”
Bryne wrote in Géotechnique Vol. 70, No. 11:
Byrne further explained that although the current form of the model was developed for offshore wind turbine monopiles, the general approach could be applied to other foundation and soil-structure interaction problems where bespoke calibration of a simplified model can lead to more efficient design.
For more information about this work and more detail about some of the specifics, equations and field test results, all nine research papers are available in the November 2020 edition of Géotechnique. View the webinar “New Design Tools for Laterally Loaded Wind Turbine Monopiles,”.