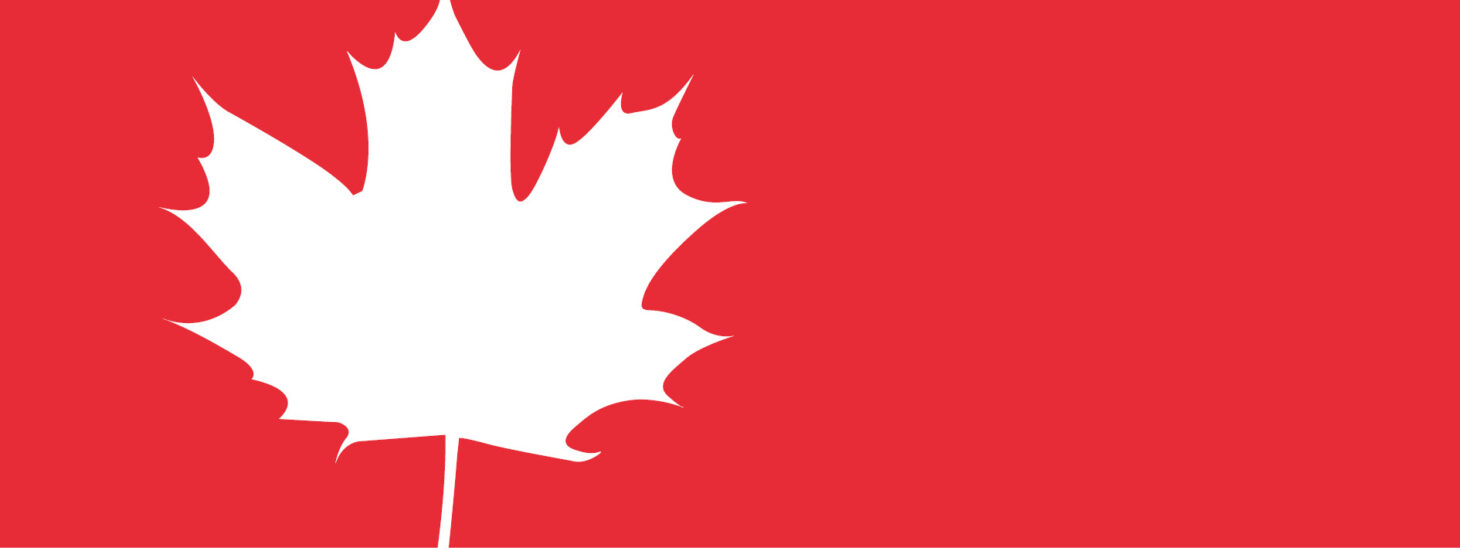
M. Johnston Construction Ltd. is an industrial and civil contractor specializing in pile driving and foundation construction, bridge construction, maintenance and repair, bridge and mat rentals, industrial steel installation and removal, resource roads and industrial site work. The company is based in Cranbrook, B.C., with a yard in nearby Galloway and a separate avalanche consulting division in Squamish, B.C.
A proactive approach to environmental protection
The family-run business was begun by Mike Johnston and incorporated in 1978. “Today, a number of employees are also shareholders,” said engineer Monte Johnston, Mike’s son, who began driving a backhoe as a teenager for his family’s company more than a decade ago.
The company employs seven people full-time as project managers, supervisors and operators and relies on a core of up to 25 seasonal workers, providing a wide range of services, from small bridge repairs to multi-million dollar contracts, to clients across British Columbia and in Alberta, Saskatchewan, the Yukon and the Northwest Territories.
Many projects are located in remote or rural locations, says Johnston, and most are in environmentally sensitive areas, often near fish-bearing creeks and rivers. Environmental professionals are called upon as needed to develop job-specific construction environmental management plans and to provide onsite assistance, and the company takes a proactive approach to environmental protection and has never had a major environmental incident.
“We use Berminghammer, APE and Bomag [equipment] for pile driving, but Berminghammers are our favourites because they’re so clean-burning,” said Johnston. He notes that diesel-burning engines can produce considerable exhaust when diesel in the chamber isn’t completely combusted. “The Berminghammer doesn’t do that, which really minimizes our environmental impact.” As a further precaution, the company uses biodiesel on these sites to lessen the environmental harm of possible small fuel spills.
Johnston Construction’s drilling and caisson-installation equipment can be used for shallow to deep foundations, and their down-the-hole (DTH) percussion hammers enable installation of caissons from 150 to 610 millimetres in diameter. The system drills and installs the caisson in a single pass, quickly and accurately, eliminating the need to case the hole before drilling regardless of the geological formation to be drilled. Caissons can be drilled at an angle, through boulder-laden overburden, or through consolidated bedrock. Johnston describes the dual rotary process.
“A drill grabs and twists the caisson into the ground while at the same time the hammer inside the caisson turns the other way and cleans the inside, operating a little bit in advance of the tip of the caisson so there’s always a bit of a pilot hole for the pile,” he said.
Drilling the “undrillable”
Since detailed subsurface information is not always available before construction begins, the DTH hammer may be exchanged for an air rotary drill or continuous flight auger, depending on the soil conditions encountered in the field.
“Modifying our method of installation allows us to drill something that’s ‘undrillable,’” he said. For a pedestrian bridge in Carcross in the Yukon, piles 130 feet deep needed to be drilled down through soil and socketed into the bedrock, after which a five-metre rock bolt was drilled into the bedrock at the bottom of the lake inside the caisson, and then grouted in place without allowing any water to get into the piles.
“We anticipated some of the problems ahead of us, but we didn’t know them all,” said Johnston, including a layer of blue clay where there wasn’t supposed to be clay at all. “Of course, with any type of impact hammer, clay just absorbs the energy – you need a hard surface to beat against – so it just shut down our entire system.” In this instance, “We took three-metre sections of pile and put a grout plug into them and drove them with our standard diesel hammers. Once they were in place, we put the drill in and drilled that grout back out and down into the bedrock, beyond the clay. We just plugged the end in and drove it like a nail rather than try to drill it like a screw.”
The biggest culverts in North America
“You always have to come up with something if you want to win the job,” said Johnston. The 60-foot-diameter culverts the company built just outside of Slocan in the West Kootenays were the biggest in North America at time of their construction.
“We built on top of 24-inch caissons that we drilled into bedrock that was higher than the top of the piles when we started,” Johnston recalled. “We had to blast all the bedrock out of place, drill down and then blast more bedrock from around piles we had already installed without damaging the piles. It was slow, but it worked out well – we never had any damage occur to any of the installed piles.”
He describes another particularly challenging project the company undertook in 2011 to stabilize a CP Rail bridge against runoff in Yoho National park, just west of Field, B.C.
“We had to remove a bridge and install piles but we couldn’t close the railway,” he said. “There was no road access to the site, and the job had to be performed basically off of the rails. So we designed a special rail cart that could carry our pile driving equipment out to the site and designed bridges that we could pull out and replace that had sections of track attached to them. We’d pull out a section and drive a pile, put the section of track back into place and let the trains go.”
After the 2008 financial crisis, the federal stimulus package attracted other industries into the infrastructure market, but the competition hasn’t had a lasting effect on Johnston Construction.
“I’ve seen that ebb off, particularly over the last two years,” said Johnston. “A lot of our competitors who were subdivision developers or heavy construction have gone back to do what they do. We continue to do more transportation systems.” Work started in mid-February on the third bridge the company has done so far this year in rural northern Alberta for the twinning of Highway 63 midway between Edmonton and Fort McMurray. Temperatures were often as low as -30 degrees Celsius, with wind chills of -40 degrees Celsius, “but the ground up there can be really boggy and soft,” said Johnston. “Sometimes it’s easier to deal with frost than it is to deal with mud.”
This year, Johnston Construction’s new division has begun doing avalanche control work, using helicopters and explosives to stabilize avalanche-prone areas, to ensure the safety of construction sites and of the workers going to and from those sites.
Most recently, the division has been working with a large contractor building hydro roads in the upper Lillooet and Pemberton area. Johnston Construction has been awarded a Certificate of Recognition from WorkSafe BC and the B.C. Construction Safety Alliance, of which it is a member. The company is also a member of the B.C. Roadbuilders & Heavy Construction Association, the Canadian Construction Association, the Alberta Construction Safety Association and the Lethbridge Construction Association.