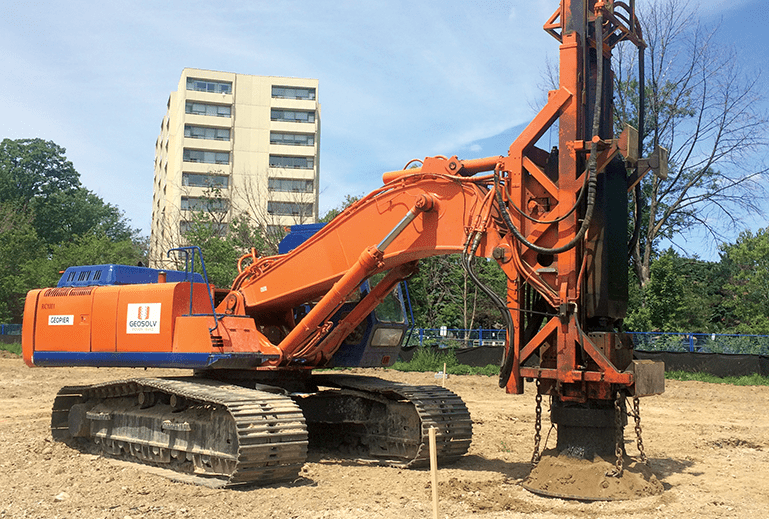
As challenging soil sites become the norm, the search is on for innovative and cost-effective methods to support new building construction. When spread footings simply don’t work, traditional approaches to poor soils such as over-excavation and replacement or deep foundation systems can be costly, time-consuming and cumbersome.
Owners and developers who are constantly battling rising construction costs and tight project budgets are wary of the risks associated with these “remove it” (over-excavation and replacement) or “go through it” (deep foundation) methods. Factors such as unpredictable weather, water and soil conditions can quickly result in extra cost and delay.
Many in Canada are now realizing that there is a third option to consider – “improve it.” There are a number of proven and cost-effective ground improvement techniques available to improve challenging soils that avoid the risks described above. One of the most cost-effective of these techniques is the Rapid Impact Compaction (RIC) method.
The RIC system involves an excavator mounted hydraulic hammer applying energy to the soil through a five-foot diameter tamper foot, at the rate of 40 to 60 blows per minute. Energy is then transferred to the ground safely and efficiently, as the RIC’s foot remains in constant contact with the ground. This system has been shown to be successful in sandy soils, densifying loose-fill soils of up to six metres deep or more, without the need for soil handling. The RIC system can provide an improved geotechnical resistance of 150 kPa or greater. In mixed fills, the RIC system has been used to reduce the risk of differential settlement for relatively lightly loaded floor slabs, often saving considerable time and cost by avoiding structurally enhanced floor slabs. Savings going from a structural slab back to a slab on grade could be $50 to $100 per square metre.
The RIC solution is typically completed in two to three passes of the site. Strike points are generally laid out within the building footprint, as well as an additional apron surrounding the building. The initial passes use a wider six-metre by six-metre grid to ensure the RIC energy extends deep to the lower soils. The surface craters created by the RIC tamper foot are then bladed flat and a successive three-metre by three-metre grid is completed. Additional strike points are added if necessary after reviewing the on-board computer diagnostics from the RIC rig.
The RIC on-board computer diagnostic system records the number of blows and the travel of the tamper foot at each location to understand the soil behavior with each successive blow. Along with visual observation by an experienced technician, this diagnostic tool helps to clearly identify areas on site which may require additional compactive effort to achieve the target density. Densifying the soils in place also results in an overall drop in the site elevation. Recording the surface elevation prior to RIC and following completion helps to qualitatively determine the reduction in voids within the densified soil.
In some cases, a test section is completed on site in conjunction with the geotechnical consultant to verify the required densities have been achieved. These test sections are typically evaluated using either standard penetration tests or preferably cone penetrometer tests.
As the fines content in soil (percentage of silts and clays) reads beyond 15 per cent, the effective densification depth tends to be reduced. Consideration should be given to test sections for soil and fill with higher fines to verify the suitability. Often, the cost savings available to the project are considerable and worth considering a test section or minor excavation of pockets of unsuitable soils that are identified during RIC work.
The RIC process uses repeated and controlled impact energy to densify soils in place. The vibrations generated by this impact energy are typically below the City of Toronto By-law requirements at a distance of roughly eight to 10 metres (25 to 30 feet). When working closer than this to receptors, mitigating measures can be undertaken to reduce vibration travel.
It is not hard to imagine the cost and schedule benefits RIC can deliver over a “remove it” approach on your project. Advantages of the RIC system include the following:
- Avoid shoring systems – work can be completed at or near the property line
- Minimize or eliminate dewatering – footings founded high on improved soils limits excavation
- Rapid installation – work is completed at up to 800 m2 a day from existing grades
- Schedule savings – avoiding excavation eliminates challenges caused by weather events
- Cost certainty – the RIC process is typically completed by GeoSolv as a design-build lump sum
When evaluating the support for your next project, remember that there are a number of options you can consider. To ensure you are maximizing the value of your project, remember to evaluate all of your options – remove it, go through it… or improve it.
Neil Isenegger, P. Eng. is a senior design associate at GeoSolv Design/Build Inc. For more information regarding RIC or other ground improvement methods, contact GeoSolv Design/Build Inc. at solutions@geosolv.ca.