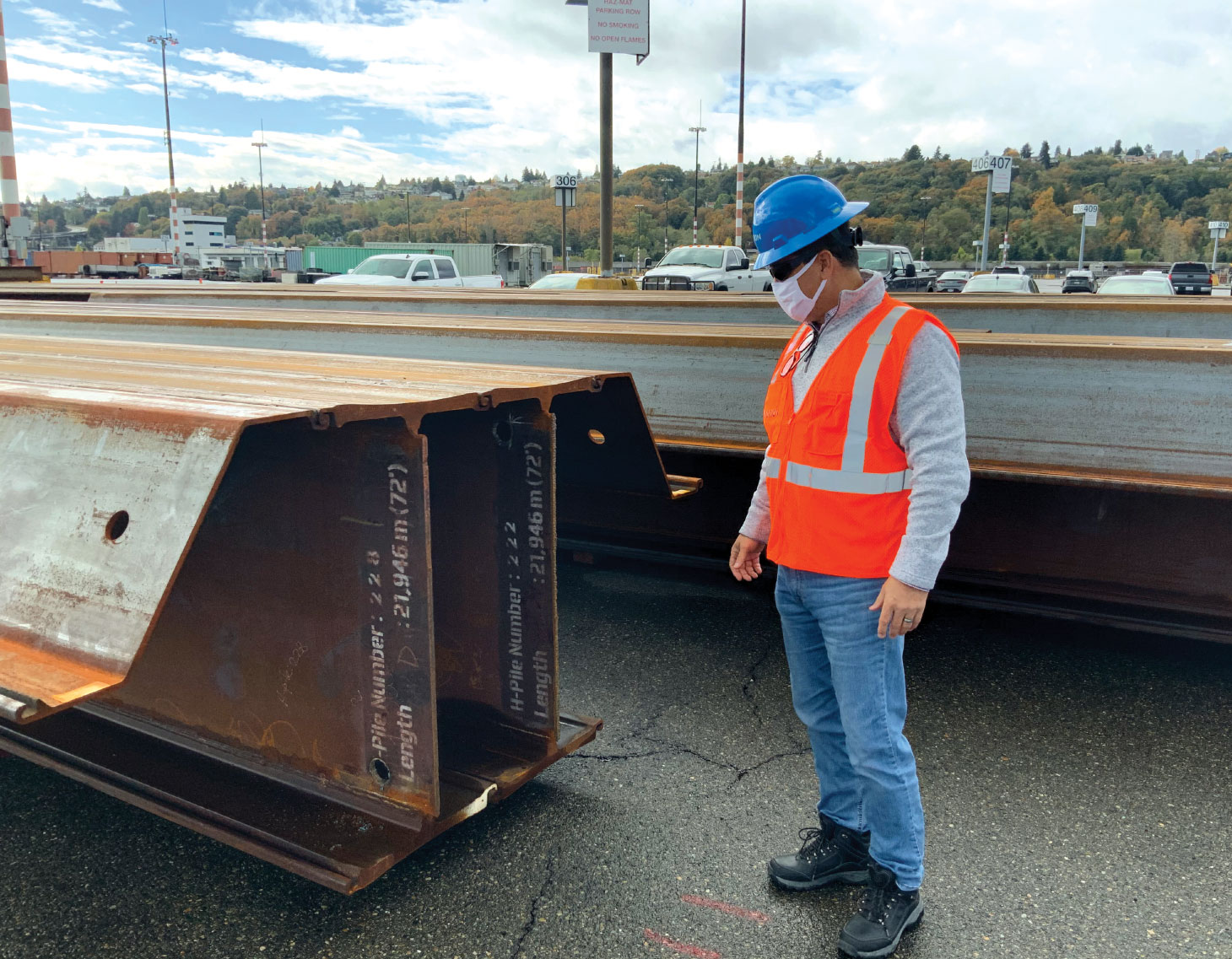
To decrease environmental effects of the steel making process, leading global steel manufacturers are going beyond the original practice of carbon credit offset.
JD Fields’ European piling partner ArcelorMittal is embracing the industry role of environmental steward, offering the first and only piling product series certified recycled and renewably produced. Recently, JD Fields held a webinar to explain the new industry terminology for environmental product declaration and life cycle analysis, and the future role low-carbon steel piles will play in project evaluation, specification and purchasing.
While the AZ family of hot-rolled sheet piles and the HZ-M combined wall system are not changing, Dean Abbondanza, JD Fields director of engineering, says it is the steel production process that is making the environmental difference. To fully understand the environmental effects of steel making, it is necessary to understand the three primary processes from which molten steel is produced.
“In order of environmental impact from worst to least CO2 emissions per ton, you have the traditional blast furnace, then direct reduction iron, to the least CO2 emissions, electric arc furnace (EAF). Fortunately, ArcelorMittal’s Luxembourg mills and all North American hot rolled piling mills all use the EAF process,” said Abbondanza.
AZ and HZ-M Lines
The AZ sheet pile series is one of the most comprehensive families of hot rolled sheet pile sections on the market. The HZ-M series is a high modulus king pile beam combined wall system that picks up where the heaviest sheet pile sections capabilities leave off. Both pile series are backed by a very experienced technical and research and development group.
“From the recent 750 millimetre (mm) and 800 mm widening of the AZ series, to the improved beam production of the HZ-M series in 2008, these innovations combine to bring maximum pile weight and performance efficiency to designers and end users,” said Abbondanza.
As for how low CO2 steel piles are made, the XCarb brand starts with the steel-making process of melting recycled steel scrap via the EAF. This is the least CO2 emissions of the known methods. “Additionally, 100 per cent of the electricity used to power the furnace is certified renewably sourced energy,” Abbondanza said. “This combination of recycled content and certified renewables is the most environmentally friendly steel-making process.”
In a recent webinar, Abbondanza referenced a project that was the first one where JD Fields supplied HZ-M sheet piles. “It is for a high modulus combined wall application in New Jersey. It was a smaller-scale project that entailed about 275 linear wall feet of bulkhead for a marine construction dock. We used it as an example to demonstrate the environmental features and benefits that could potentially be realized on future projects,” he said.
He also shared a European study that compared the environmental and economical features and benefits of eco-friendly steel piles versus concrete and in-situ methods. “This study was performed in 2018 on a cruise ship terminal bulkhead project in Europe that clearly demonstrates the value XCarb Eco Sheet Pile Plus brings to a project compared to alternative materials.”
The future
As for how these innovative sheet piles will play a part in project evaluation and decision process going forward, Abbondanza says the “effectiveness of this initiative will be dependent upon how swiftly we can apply it toward the environmental legislation regarding building and construction materials.” He is optimistic that the future of environmentally friendly steel piles with a low-carbon footprint is looking bright.
“While European manufacturers may have a head start on marketing environmentally
responsibiy-produced steel piling, domestic producers like Gerdau are not far behind. The challenge is applying the features and benefits of this green steel production process to the U.S. market and getting owners and designers the tools to realize the potential credits steel offers projects utilizing the Buy Clean & Inflation Reduction Acts as the vehicle.”