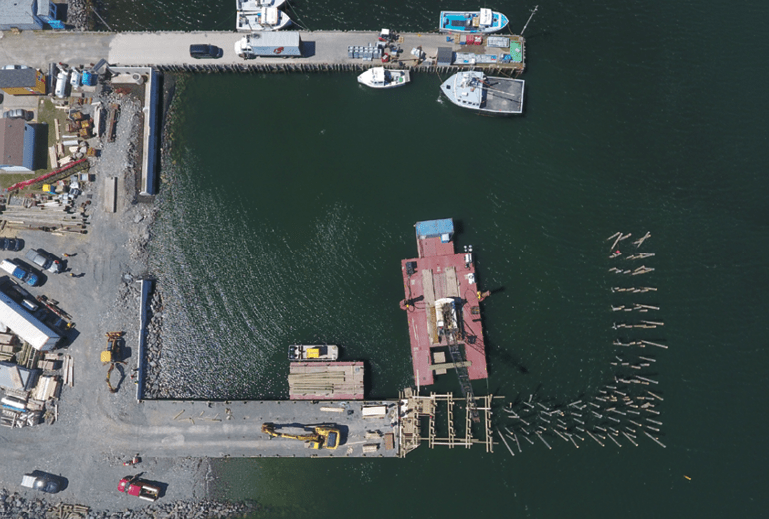
As Alva Construction Ltd. Of Antigonish, N.S. began the timber pile component of a major project to replace the fishing wharf at Little Dover, N.S., engineering manager Reg Tramble was looking for a machine control system that would streamline the placement of the piles.
The job involved driving 180 timber piles – 132 bearing or vertical piles and 48 batter piles in the L-shaped pile work wharf section. Positioning and adjusting the angles of the batter piles had always been accomplished by crewmembers in a raft, which in addition to being time consuming, presented an element of danger to the crew.
In March of this year, Tramble was about to leave for CONEXPO-CON/AGG in Las Vegas when he received a call from a local SITECH Trimble dealer, who suggested that he connect with Lou Nash, president of Measutronics, at the Trimble display at the show.
Measutronics is a Florida-based marine dealer that sells Trimble and other high-end marine sensing equipment. It is also a system integrator that combines any number of third-party sensors to provide the applications needed by its customers. The resulting meeting in Las Vegas set in motion a process that ended in the creation of a positioning system that promises to cut the time for positioning and driving piles in half.
At the show, Trimble and Teledyne had announced the re-branding of Teledyne’s Port Dredging Survey (PDS) software with the Trimble name, and they were demonstrating the new software package, entitled, “Trimble Marine Construction (TMC) powered by Teledyne.” Nash and his engineers had created a dredging system that included real-time visualization of a dredging project, including a three-dimensional view of the dredging bucket in action, full statistics on the dredging progress, real-time views of the bottom, amount dredged, amount remaining to be dredged and other vital information and descriptive operator screens.
Pile driving had always been one of the solutions Nash offered, but the addition of the PDS software offered the possibility of 3D graphics, and the request from Alva was the spur to finalize this application. Tramble explained what was involved in moving and positioning piles, and Nash agreed to create a system with the sensors and parameters required for pile driving, especially for the raked piles, which must be driven at an angle within specific tolerances.
Crewmembers are lifted to the top of the lead to install the equipment mount. The crane is a Terex crawler crane mounted of floating seven-foot-deep Poseidon P2 barges. Photo shows the in-progress timber pile section of the project at right angles to the first section.
Back at Measutronics headquarters in Lakeland, Fla., Trevor Yocum, who performed most of the beta testing on the system, created a mock-up of the proposed system to envision the location of the GPS receivers and antennas, angle sensors and other hardware on the equipment and in the cab. Teledyne programmers in Rotterdam wrote the software for the drivers that integrated the changing information from each sensor into the system, and marine construction systems specialist Nathan Keys worked with Nash to envision and create operators’ screens that showed a simple and accurate method of positioning a pile before and during engaging the hammer, along with monitoring and displaying other statistics of the ongoing project.
The new application was ready to go 10 days after CONEXPO closed.
Keys describes the main operating screen, split into three screens, as having the current pile location represented in green and the target location in yellow. Text indicates movement from left to right, straight line distance to the target, the change required to get from the current location to the target location in the forward/backward direction, change required to get from the current location to the port/starboard direction and change required to get from the current heading to the designed heading. This screen shows the yellow line that the operator aims to cover with the green pile in a vertical placement. The red piles are design piles that are selected one by one as the project progresses.
Another section of the screen shows a real-time 3D view of the project area, with the design pile locations in red, the selected design pile in yellow and the current pile/lead shown as a thick green line. “Basically, they want to move the green pile onto the yellow one,” said Keys.
As the operator moves the joysticks, the text reads the inclination change required to get to design inclination, and another reading gives the inclination heading change required to achieve the design inclination heading. Meanwhile, he sees the green pile moving toward the yellow line on the screen. “The third screen is where you select which design pile you are going after. Once the pile is selected, the screen shows the design pile properties such as northing, easting, elevation, length and inclination,” said Keys.
The system uses the Trimble BX982 Marine GNSS Receiver, which Keys calls the “brain” of the system. The antennas were two Trimble Rugged Zephyr 2 GNSS antennas, one providing position and the other to allow calculation of heading. The Alva crew built a metal bracket perpendicular to the pile driver lead, with a rail around it to protect the antennas and the pitch and roll sensor from the free-swinging piles as they were loaded into the leads. The bracket was placed high on the lead to minimize the possibility of it being struck by the piles.
Another concern was for the cable that connected the components to the computers in the cab. The solution was to run the cable inside the crane boom, with sufficient slack to prevent movement of the crane and leads from affecting it. The cab-based equipment included a laptop computer to run the TMC software and the Trimble GNSS receivers. Because space in the cab was limited, a Panasonic Toughbook CF-19 with a 10-inch screen was used.
Cheston VanAlstyne, install technician for Measutronics, positioned the cables so they were out of the way and would not interrupt the normal operation. The GPS and pitch and roll sensors were hardwired through the equipment to get the data to the computer, which eliminated external cables for those functions. After installation of the equipment bracket, followed by three days of installation, calibration and training by Measutronics, the system was put to work.
The pile driving portion of the project was 65 per cent complete, and during the remainder of the project, the time for placing the piles decreased dramatically, says Tramble. For the vertical piles, it took 40 to 50 per cent less time, and the only necessary human contact with the pile was during loading and for one person to unpin the pile from the lead after it was driven. For the raked piles, the time savings was about 25 per cent, says Tramble, but he expects this to improve to 50 per cent after the operator becomes more familiar with the system.
For this project, Alva didn’t include a component that would position the barge in a location that would allow the maximum possible piles driven per setup. The crew reported that this feature would be helpful, and Tramble intends to add it to the system before the next project.
Alva used a Terex crawler crane mounted on floating seven-foot-deep Poseidon P2 barges stabilized with two spuds during operation. The pile driver was a fixed lead Bermingham VTL system with a Pileco diesel hammer. The $4.44-million project was awarded by Public Works and Government Services Canada/Department of Fisheries and Oceans. The old L-shaped wharf was demolished, leaving the main stem for use by fishing boats during construction of the new wharf 100 feet away.
The wharf consists of two sections, the first is a cribwork section with reinforced concrete deck, nine meters wide by 33.2 metres long. The second is a timber pile section, which turns 90 degrees to the first section, and is 70 metres long and 6.1 metres wide. It will be completed with a reinforced concrete cap and deck.
The project is expected to be complete in November of this year.