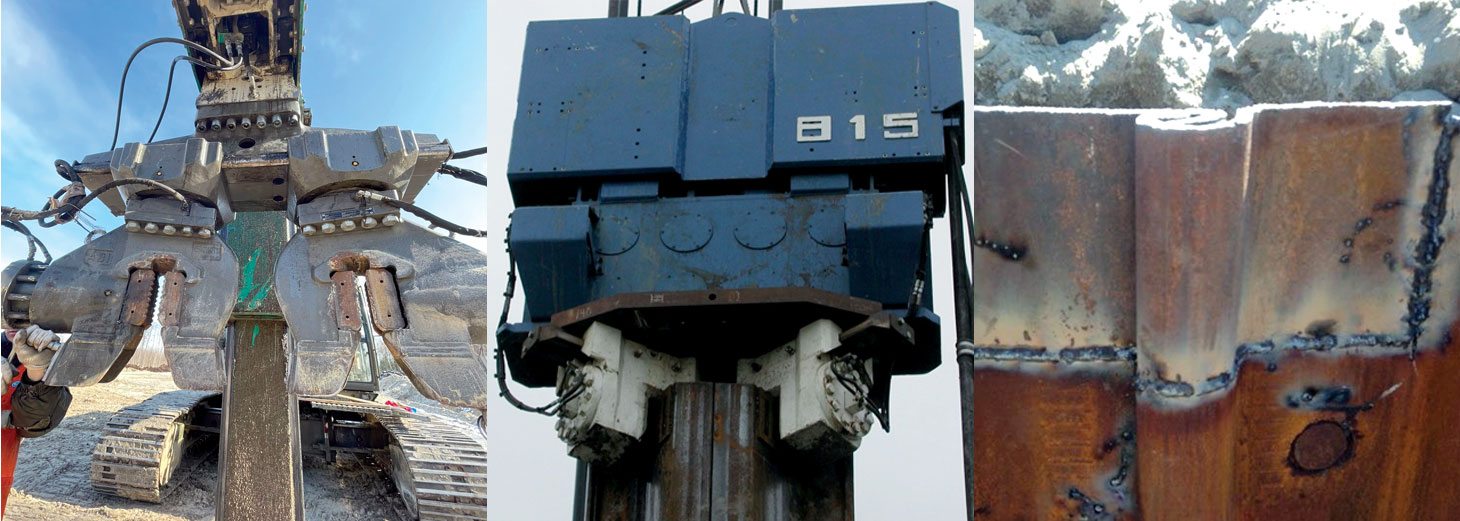
Gerry McShane still recalls the amount of re-construction that was required after Hurricane Sandy decimated the mid-Atlantic region of the United States in 2012.
“There was six miles of coastline driven with heavy cold form sheet piles,” he said. “On that project, there was failure after failure of sheet pile heads and repair after repair. When you look at the scale of that project, the amount of repair work that was done, the need [for] sheet piles just for the sake of cutting them up to provide repair material, it was clear there would have been significant savings for the contractor had double clamps been available.”
McShane, the director of piling sales for Service Steel Warehouse, recognizes that while double clamping remains a less-than-common practice in the piling sector, there is a need for greater adaptation. With more than 35 years in the construction industry and expertise in ground engineering, McShane has worked exclusively in the steel piling industry on four continents.
He says the need for double clamping has emerged as sheet pile manufacturers have steadily increased the width of steel piles over the last 20 years to improve efficiency. However, problems began to emerge after 770-millimetre-wide (30.3 inches) and very light sheet piles were introduced into the market.
“The wider the sheet pile, the more skin friction is developed across the sheet pile area during installation,” said McShane. “Typical vibro hammers used a single clamp that sits across the centre lock of the pair. While this works well with most 700-millimetre-wide sheet piles, the limitations of using a single clamp became apparent with the lightweight 770-millimetre-wide.”
These limitations emerged as the additional skin friction developed on the wider pile led to increased penetration resistance. The hammer energy increased to ensure penetration, which led to increased stress on the sheet pile where it is clamped by the hammer. On a thin, wide sheet pile, a single clamp’s concentration of hammer energy at the locks can lead to fatigue and localized steel failure at or near the lock.
“If you are driving wide light sheet piles and they’re failing, that’s an indication that a different approach is warranted.”
Gerry McShane, Service Steel Warehouse
A second and less recognized problem occurred with recently introduced higher capacity cold form sheet piles. This appears to be the same problem of wider sheet pile – excessive skin friction – but is in fact quite different. Similar fatigue failures occur at the lock; however, the failures are caused by the larger cold form lock being slightly too large for the throat opening of the vibro hammer. If the lock didn’t go into the hammer at all, the problem would have been seen and corrected long ago. However, it still goes in, only slightly skewed, and the problem is not easily visible to the piling crew. One side of the vibro clamp will catch the edge of the lock, lifting it slightly. This leads to a concentration of hammer energy on one side of the pile and quickly leads to fatigue failure.
The double clamp solution
“The solution to these issues has been to cut off the head of the pile, cut a new piece of sheet pile and weld it back on as you repair the piles. This may seem like a quick fix, but if you are doing a run of sheet piles that’s a mile long and you are repairing every single pile, then there are a lot of additional new sheet piles to make up these repair pieces. This cost has not been recognized by the industry as being significant when it actually is,” said McShane.
He says double clamps should be used to distribute the vibro hammer’s energy concentrically down each pile in the pair. With wider lightweight sheet piles, the additional skin friction that is a problem for single clamps is easily dealt with. For larger cold form sheet piles, a double clamp solves the lock size issue and eliminates lock fit concerns.
Despite these benefits, McShane says adoption by the industry has been slow for several reasons. First, he says there is a lack of understanding that lightweight wider piles present a problem due to excessive soil resistance.
Secondly, there is very little or no understanding that failures of the locks on heavy wider cold form sheet piles are caused by the lock being slightly too big for the clamp throat, and that double clamps solve these problems, according to McShane. There is also a general lack of awareness of the availability of double clamps and a preference by the industry to stick with single clamps despite their limitations.
However, the biggest reason appears to be the perceived cost of using double clamps.
“The general indication from the market is that I can just buy a sheet pile, I can buy a crane with a vibratory hammer suspended from it and it will sit on top of the pile and drive it in,” said McShane.
The financial arguments
McShane says the average costs using a single clamp are around USD $26,000 per month, which includes the crane rental, vibro, power pack and a four-person crew. If you use a leader-rig, two-person crew with a double clamp assembly, then the price increases to around $46,000 per month, but with twice the production speed. In the end, most contractors will simply opt for making the repairs.
However, on longer installation projects, the cost savings can be considerable. When you start cutting heavier sheet piles for continuous repairs, the costs add up quickly. McShane has calculated that the repair bills, including the costs of the welding crew and heavy cold form sheet pile replacement pieces, can add an additional $45,000 to the initial $26,000 single clamp monthly rate, totalling approximately $71,000 per month, compared to $46,000 for a double clamp setup.
McShane says hammer manufacturers typically have double clamp options for pile drivers, but there appears to be a lack of awareness in the North American marketplace. Double clamps are used fairly extensively in Europe. They are also not complicated to use – it just takes additional time to assemble.
“If you are driving wide light sheet piles and they’re failing, that’s an indication that a different approach is warranted,” said McShane. “It really is poor practice to be ripping the heads of sheet piles during the installation process. If it’s something that is occurring frequently, then the cost of switching to a double clamp is irrelevant because your productivity is increasing. You can install rapidly without any problems occurring, you don’t need a backup crew doing welding and cutting and you’re not destroying new sheet piles. It’s just a change in mindset.”