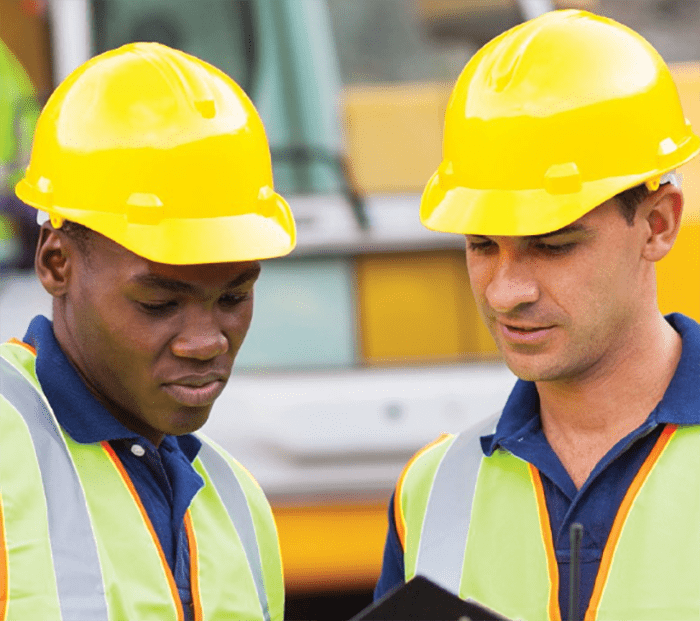
MichaelJung/shutterstock.com
When leaving for work each morning, we often don’t think about our safety. We tend to take for granted that we’ll have a decent day and come home to our loved ones, ready to eat and rest and do it all again tomorrow. But, of course, accidents happen. The Association of Workers’ Compensation Boards of Canada (AWCBC), in its most recent data, reports that in 2014, there were 919 workplace deaths across the country; 232 of those happened in the construction industry. That may not seem like a significant number, but you could argue that anything above zero is significant when it comes to workplace fatalities.
Safety is everyone’s responsibility and shouldn’t rest solely on the shoulders of the safety manager or site supervisor. Safety talks are a fantastic resource to incorporate into your organization’s safety program. Talking, however, is one thing; walking that talk is another. How do you keep your team engaged and focused during a safety talk? Who should conduct them, and how often? There are many different ways to hold effective safety talks and ensure everyone heads home safely at the end of the day.
Safety talk essentials
When it comes to planning and giving effective safety talks, there isn’t necessarily one particular approach to follow. Scott Lescak is a senior safety advisor with Pacific Safety Consulting Group in Vancouver. Lescak believes that safety is everyone’s business and should be planned for as such.
“How often should safety meetings take place? Every day, all the time. Who should be conducting them? Well, everyone. There are many different ways to do safety talks and many different people who can do them effectively,” he said.
According to Lescak, much of how you approach safety will depend on the level of risk, and your understanding that there is no one-size-fits-all safety program. If your work site has changing conditions or differing environments and you have a large crew, more frequent safety talks could make sense. If your site and crew are small with less complications, a quick talk in the morning or right after lunch may be what works best. But don’t be afraid of tailoring your safety program to the needs of your crew and the level of risk that exists on your job site.
What to talk about
As the term implies, safety talks involve talking. But what do you talk about? Lescak has some suggestions.
“Keep the topic practical and relevant so that whatever you’re talking about, you’re touching on key points and reminding your workers about how to be safe on the job,” he said. “Anything new is a good place to start in terms of a topic – a new worker, a new piece of equipment, a new phase of the project. Not everyone may know about it, and there are usually requirements around risk assessments for changes like that. So talking about anything new is always a good idea.”
Sometimes, the trouble isn’t in the topic of discussion but how to get the meeting started. A great way to do this, according to Lescak, is to have safety shares. Crew members discuss things they’ve seen or experienced on site that either were great and added to the crew’s success or were concerning and need to be discussed.
Risk and relevancy to the job are also things to consider when thinking about the length of a talk. Sometimes, a 10-minute meeting is all that’s needed because nothing about the site or the work has changed. Your crew are already aware of the risks and how to do their job safely. In other instances, a longer meeting may be necessary to discuss new or changing information relevant to the site or crew.
Keeping focused
Even though safety on the job is an important topic, it isn’t always the most interesting. Keeping everyone’s attention through a safety meeting can be pretty difficult if you haven’t planned accordingly.
“One thing you can do is minimize distractions,” said Lescak. “Keep it so that your audience won’t be looking in other directions, focusing on their phones or looking at the next site over. Use a seasonal theme or a daily theme to keep it relevant to what they’re doing and to get them involved.”
If you find that the same person is always conducting your safety talks, switch it up and involve the crew. By having different crewmembers lead a safety talk, you’re not only breaking up the inevitable monotony of the meetings, but you’re also avoiding boredom by actively involving the very people you’re speaking to. Having senior management lead a safety talk demonstrates commitment and involvement from the top level.
“In a well put together organization that has a solid safety program, the message is already coming from the top. Getting senior management to come in for a talk can help engage an audience and really drive home your point,” said Lescak.
Other tips for how to avoid audience boredom include using graphs, pictures and other images; performing a hands-on demonstration; and using humour.
“Humour can work well and can go a long way when it comes to engaging your audience. But you also need to remember to speak clearly and concisely. Understand what you have to say, say it quickly and effectively, don’t waffle and be done,” said Lescak.
Boss on site
Is having a safe, efficient job site synonymous with having an ever-present safety manager? Not necessarily. Again, you must consider the level of risk for your site and crew. The frequency of a safety manager’s site visit depends on several variables like crew size, project, environment, conditions and risk. According to Lescak, it’s not only about the quantity of visits, but also the quality.
“If you’re there three times a day but on your phone and distracted, that may not be as effective as being there once every three days but being fully engaged and attentive, spending time on who you’re seeing and speaking to, and listening,” he said.
If a safety manager is trying to gauge their involvement, Lescak says they might consider their comfort level concerning their presence on site if something did go wrong.
“How comfortable are you with the amount of time you’ve spent on site? When was the last time you were on site? Is there something you could have, should have or did see that could have been influenced by how often you were on site? These are just some internal checks for safety managers. If you’re asking and answering these questions honestly, then you should get a good gauge on whether you should be on site more often or if you’ve got a good balance.”
When the safety manager is on site, a big factor to look out for is safety compliance. An organization can say they’re the safest in the world with the best safety program available in their industry. But if that organization is not actively in compliance with their safety program, then it could be all for naught. Consider the expectations of the various stakeholders – employees, management, clients, regulators – and consider whether the organization is meeting those expectations as you walk around the job site.
Behaviour is another major factor to look at in terms of safety. The safety manager needs to ask him or herself if they have an understanding of what the right behaviour is, and if it’s being observed on the job site. Stop and check. Ask someone if they’ve done a hazard assessment and, if they have, look at how effectively it was done. This is a great way to make sure behaviours and expectations surrounding safety have been clearly communicated.
There will be times, though, where you may come across a person who isn’t displaying the behaviour you want to see.
“Sometimes, a worker can trip themselves up when answering a safety-related question. It might just be their personality or it might be that they really don’t know what you’re asking or how to answer. This can be a sign of where the culture is at in terms of safety. In a culture where safety is meshed together as part of the fabric of the organization, when you stop to ask someone about safety, that person will likely be confident and comfortable with their answer because they’re talking about their job. And safety is just a part of their job,” said Lescak.
Safety culture from the top down
When it comes to generating buy-in from your crew and showing them that the organization is truly committed to their safety, what it boils down to is leadership. Lescak says that without a strong leadership commitment from the top, you’ll find that managers at various levels are more difficult to engage with in terms of safety, that there is less trust, and perhaps even a lack of accountability and responsibility. This type of environment is simply not one that employees are going to put their trust in.
Employees must clearly see that the organization is committed to keeping them safe. They need proof that safety isn’t just a budget item to be checked off or a dollar value to be spent. Utilize open, honest communication and involve your employees in the process. When there is a safety success, broadcast it! Show your staff that their efforts towards safety are having an impact and that, at the end of the day, all the organization wants is for each of their team members to go home to their loved ones, safe and sound.
For Lescak, it’s about understanding what safety is truly about.
“Safety really is about people. If you can engage people actively and genuinely, that’s how you make a difference with safety. Hopefully, you’ll end up with a positive morale, a team that believes in safe work and that takes safety seriously. Sometimes, that’s proof enough that the company is truly invested in the safety of their employees.”
-
CZM Foundation Equipment introduces CZM Capital Financing options for customers
April 25, 2024 -
Student Engagement Committee
April 25, 2024 -
DFI announces two new committees
April 25, 2024 -
Keller’s John Wolosick and Allen Sehn receive awards at the 2024 Geo-Institute’s Geo-Congress
April 25, 2024 -
Rod Kern appointed as vice president of Equipment Corporation of America
April 25, 2024