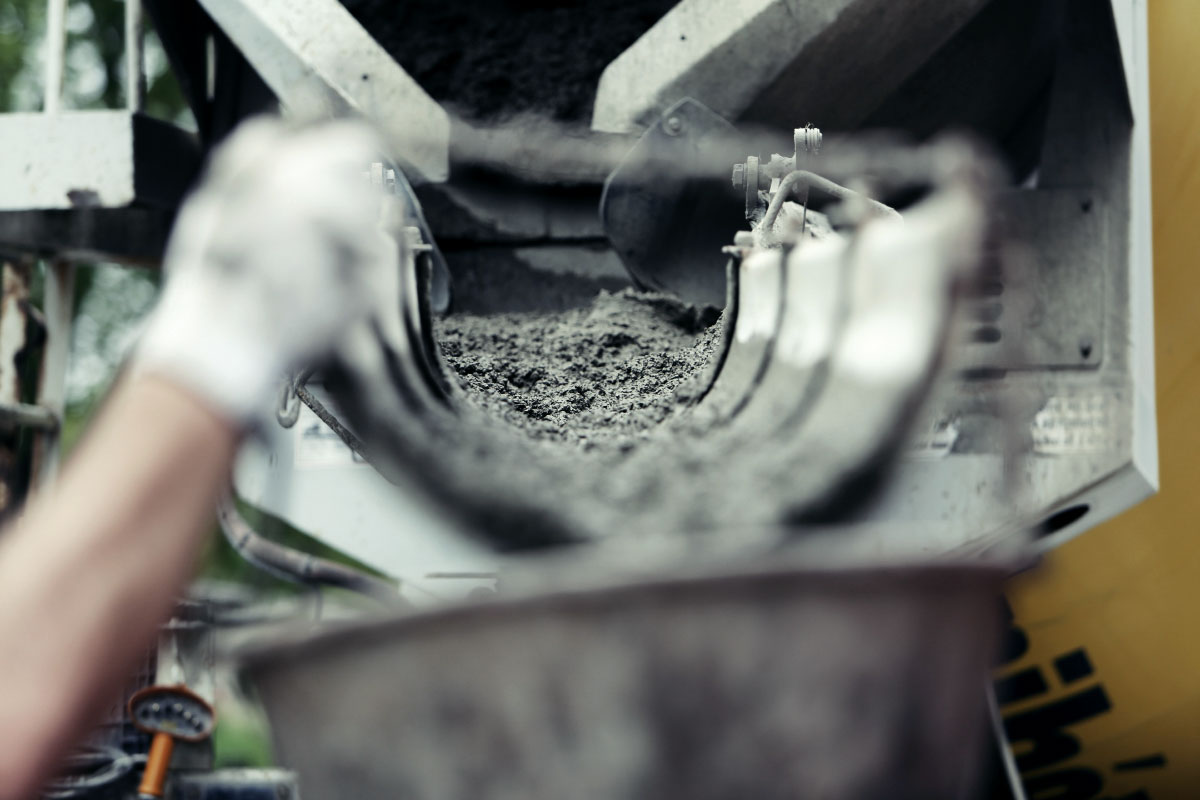
With the ability to provide long-lasting infrastructure, contribute to robust economies and mitigate the impact of climate change, cement and concrete play an important role in creating a more sustainable and resilient world. Concrete is among the most consumed materials in the world, second only to water.
The Portland Cement Association (PCA) member companies produce the majority of cement manufactured in the United States. Many member companies also produce concrete and concrete products and sell them to concrete producers, says Rick Bohan, senior vice president of sustainability for the PCA. According to the U.S. Environmental Protection Agency carbon emissions data, the manufacture of cement accounts for 1.25 per cent of emissions of carbon dioxide and other greenhouse gases in the U.S., which is predicted to add another 121 billion square feet (more than 11 billion square metres) of buildings by 2050, in addition to trillions of dollars worth of repairs and upgrades to its infrastructure. Carbon neutrality will greatly slow global warming, with benefits to air quality, ecological recovery and landscape beautification.
The PCA’s “Roadmap to Carbon Neutrality” identifies five links in the value chain that must pull together to reach and potentially accelerate the goal of carbon neutrality: the production of clinker, the manufacture and shipment of cement, the manufacture of concrete, the construction of the built environment and the capture of carbon dioxide by concrete, which is a carbon sink.
The Roadmap lays out specific targets for each decade and outlines timelines, technologies and supporting policies needed to achieve them.
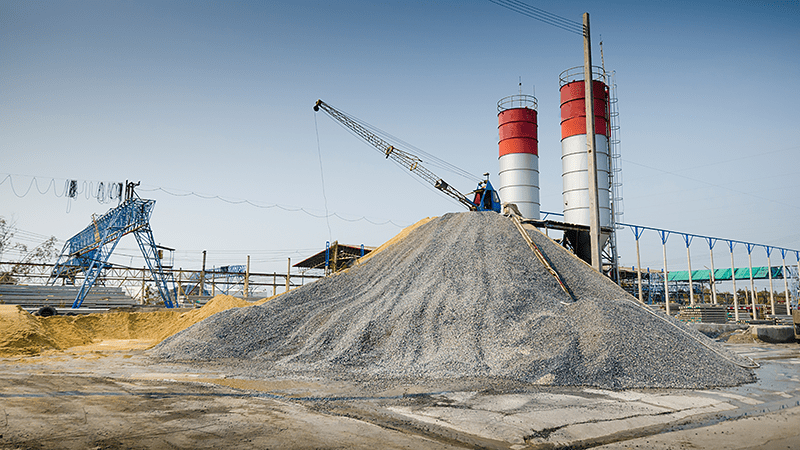
“Those links are intimately related to one another; what happens ‘upstream’ has ripple impacts ‘downstream,’” said Bohan. “Likewise, ‘downstream’ demands drive ‘upstream’ supplies. Progress in one link will often be out-of-sync with progress in another link.”
The value-chain approach allows for responsive adjustment to ensure that overall progress stays consistent.
“The most energy-intensive phase of the chain is at the cement plant, where two critical materials are produced: clinker and cement,” the Roadmap stated.
The essential chemical reaction in cement manufacturing, the “chemical fact of life” responsible for more than 60 per cent of CO2 emissions from cement manufacturing, is the transformation of calcium carbonate in limestone to calcium oxide. According to the Roadmap, “there is no way around that step, and there is no viable alternative that can be produced at the scale needed.” Material temperatures of about 1,500°C are needed to drive off the CO2 and continue the chemical process. Fuel combustion is the only way to achieve those high temperatures, accou-nting for 40 per cent of manufacturing-produced CO2.
A ‘chemical fact of life’
Clinker, the most chemically active ingredient in cement, is produced by heating quarried materials like limestone, clay, shale and sand. Heating limestone releases CO2, so its production is a significant source of CO2 in relation to cement. Using decarbonated raw materials as feedstocks, such as slag and fly ash, which have already been processed and no longer contain CO2, can reduce the CO2 generated by the chemical reaction and divert these materials from landfills. The CO2 generated from combustion in the manufacturing process can also be reduced by using alternative fuels and increasing fuel efficiency and, in the future, from new fuels and technologies.
“While we can’t control the downstream portion of our value chain, we can take the lead.”
– Rick Bohan, Portland Cement Association
Today, a cubic yard of concrete represents about 500 pounds of CO2. By decreasing the amount of clinker and increasing the limestone, inorganic processing additions and other materials, and using conventional and machine-based tools to design tailor-made mixtures that possess the optimal strength and durability for specific applications, the Roadmap suggests that by 2050, the amount of CO2 generated by the same amount of concrete will be less than 200 pounds. Construction efficiencies such as more precise design and reducing excess materials at the jobsite will achieve a 30 per cent savings.
Mixing and delivering concrete also requires energy – shifting to renewable energy sources, the total CO2 footprint of production facilities can be reduced to zero emissions by 2050; transitioning from diesel-powered to zero-emission fleets can result in a 50 per cent CO2 reduction.
In the U.S., governments at all levels have been actively focusing on carbon capture for energy-intensive industries like cement to accelerate its at-scale implementation, says Bohan, but as of today, carbon-capture and related technologies are still in the research and development phases. The industry supports various research and technology efforts to accelerate its progress and is working with – or as – an advisor to government agencies, research institutions and universities worldwide.
“PCA is working to ensure those efforts achieve their goals and don’t unintentionally exacerbate greenhouse gas emissions,” said Bohan. “And while carbon capture at the cement plant can achieve dramatic carbon reductions, we believe carbon neutrality is achievable only by using the full value chain.”
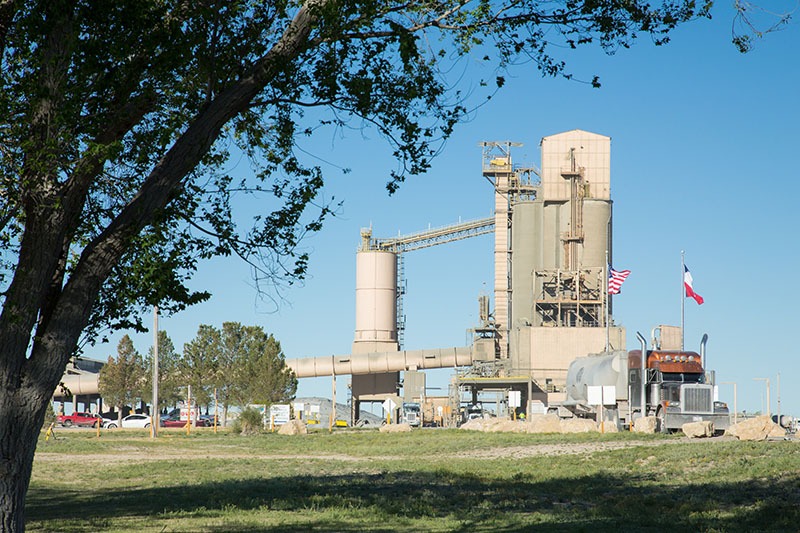
There are issues that the cement industry won’t tackle on its own. Carbon capture, for example, will also need power, pipelines and permitting.
Bohan said, “Power, because carbon capture will increase energy consumption at our plants; pipelines, because not all plants will be able to inject CO2, so they’ll need to transport it to areas where the geology exists to safely sequester that CO2 permanently; permitting, because carbon capture is the equivalent of constructing a ‘plant within a plant,’ and our members will need certainty that the permitting process chosen today will be the same process used tomorrow.”
Providing direction and incentives to spur action
“The Roadmap was developed by our members, for our members, for the good of society and was unanimously approved – their companies, customers, communities and staff all recognize the urgency of the situation,” said Bohan. The Roadmap provides direction and incentives that stoke action within the cement and concrete industries.
“Our message to government, academia and the public is simple: help us to help you,” he said.
“There is no single process, product or technology today that on its own, or in combination with others, can achieve complete carbon reduction. While we can’t control the downstream portion of our value chain, we can take the lead. And using today’s processes, products and technologies intentionally and optimizing them to the fullest extent possible gives us a running head start.”
The 73-page PCA “Roadmap to Carbon Neutrality” can be found at www.cement.org/docs/default-source/roadmap/pca-roadmap-to-carbon-neutrality_10_10_21_final.pdf.
Photos: courtesy of Portland Cement Association