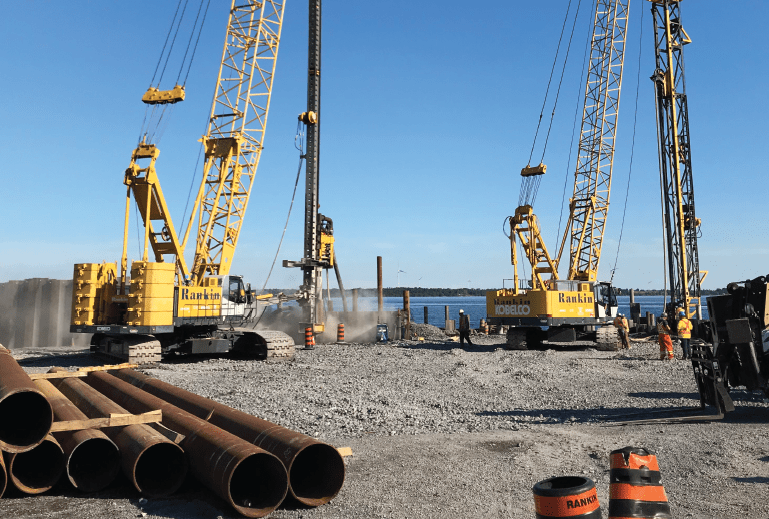
Over the years, Bermingham Foundation Solutions and Rankin Construction Inc. have developed a solid relationship.
Bermingham Foundation Solutions is Canada’s oldest foundation contractor, offering both contracting and equipment manufacturing services. Rankin Construction Inc. is an innovative and diverse company that specializes in a wide range of heavy civil construction projects that include roads, bridges, sewer and water main, marine and renewable energy.
David Zanchetta, Berminghammer Foundation Equipment sales and service representative, says a “reciprocal relationship” has formed that has seen both companies request each other’s services for multiple projects over the years. When Rankin was awarded a contract by the Ontario Ministry of Transportation to reconstruct the ferry docks at Amherst Island, it was a natural choice for the company to select Berminghammer to provide the equipment.
“Bermingham prides itself on their lasting relationships with clients and owners,” Zanchetta said. “When Rankin was awarded the project, they knew and trusted that Bermingham would be an asset to the design, installation, staging, resource supply and management of the work.”
The upgraded project will include reconstructed ferry terminals at both Millhaven and Stella to accommodate the end-loading ramps for the new Frontenac ll ferries and the future new Amherst Island ferry. The goal is to create easier access to and from the island, improve the overall efficiency of ferry operations and accommodate the increasing number of large commercial trucks and farm equipment that use the service.
The design phase of the project concluded in summer 2017 with the construction phase following soon afterward. The new end-loading docks are scheduled to be in service by June 2019 and the project is slated to be complete by summer 2020.
Although Bermingham was not directly involved in the initial design or material selection for the project, Zanchetta said the company was consulted regarding the practicality of the proposed design and what equipment and process may be suitable for its installation. He added that Bermingham recommended MS Cable Grout when Rankin was having difficulty maintaining the integrity of the toe pin cavity due to weak rock on one section of the project.
During the construction, Bermingham’s Construction and Equipment divisions have been heavily involved in various aspects of the work. At the height of production, Bermingham contributed two drilling crews. Starting October 2017, Bermingham Construction was contracted to install 16 rock-socketed piles, 24-inch diameter in the open water from a barge. These piles are used to support the temporary dolphins that stabilize the ferry during loading and unloading.
Bermingham Construction was also contracted to install sheet piles for the permanent dockwall structure, along with the toe pins, rock anchors, walers and tie-rods that hold the structure together. Berminghammer’s equipment supply and manufacturing division supplied all of the rock-socketing systems (large and small diameter) as well as vibratory hammers. Work on the permanent sheet pile walls began this February and is likely to wrap up in early 2019.
Berminghammer has also supplied the toe-pin drilling system since October 2017 and anticipates this system will remain in use until early 2019.
“Essentially, Amherst Island is getting upgraded ferry service, and this involved creating a new dockwall/pier on both sides,” Zanchetta said. “Bermingham RC drilled to install the larger king piles that the ferries will ultimately moor against. These piles were rock socketed to prevent against any movement. The sheet pile walls were installed to the depth of rock at most locations. Berminghammer provided equipment to drill holes for steel toe pins that would secure the bottom of the sheet pile wall and prevent toe failure.”
Zanchetta says there have been plenty of challenges so far. He notes that while half of the project was executed on the mainland (Milhaven), which is readily accessible by truck, the other half is on Amherst Island, which is accessible only by ferry. The technical requirements were also unique.
“This project is memorable because of the uniqueness to the equipment selection,” he said. “The equipment strategy was formulated based on the need to be able to switch between drilling and sheet piling systems regularly and often. Having a flying system that could easily disconnect from the crane allowed Rankin to utilize the same crane to complete both the drilling and sheet piling operations.”
He added that the most challenging portion was a project acceleration which involved predrilling into a rock trench to embed some sheets. “Bermingham had available an HC165 Crane and L-23 VTL Drilling system on the island equipped with an 18-inch DTHH and 24-inch bit. To drill the linear trench Bermingham drilled in a triangular pattern nesting the next pile between the previous two in order to maintain a straight line. The pipe piles were under-reamed and thus could be removed and reutilized.”
Berminghammer has supplied equipment and worked on some big projects over the years, from the Hartford Sewage Tunnel drill shaft project to the construction of the 9 Dekalb Avenue skyscraper site in Brooklyn, N.Y., – the tallest building in Brooklyn when completed – to the creation of a pedestrian pathway in the newly constructed Pier 3 Park as part of the 20-plus year Brooklyn Bridge Park Project.
Zanchetta said that among these big projects, working alongside Rankin to reconstruct the ferry docks at Amherst Island has been a memorable experience.
“This project stands out for a variety of reasons,” he said. “It really draws on Bermingham’s uniqueness as a contractor, equipment supplier and a custom manufacturer. Our construction workforce has ample experience with this equipment and are already onsite to diagnose challenges related to geotechnical conditions, staging considerations or design complications. This feedback quickly goes to Berminghammer, where the systems can be adapted to suit these conditions and custom parts can be designed and fabricated in short order to make it work. This scenario has been applicable for equipment supplied to both the construction division and Rankin directly.”