
Deep soil stabilization, also known as deep soil mixing, is used for a wide variety of construction tasks, such as improving soft soils, retaining walls (with or without reinforcement), reducing the risk of liquefaction, immobilizing pollutants, immersing and sealing walls and as a heavy-weight body.
Soil mixing and soil improvement processes work by adding binders, in which the existing soil is used as supplementary material. This process is based on mechanically dismantling the existing soil with a predominantly vertical movement of a mixing shaft. Mechanical mixing tools are used to mix soil to be improved with the binder in situ. Binders used are mainly cement and lime, but also fly ash, sand, gypsum and mixtures of these substances. The binder reacts with the existing soil and groundwater to form a soil mortar, which usually has lower permeability and less deformability, yet higher stiffness and higher shear resistance than the non-improved soil.
Out of complex soil-mix processes, Nature Drill developed an alternative that can be successfully performed in many application areas and almost every soil type.
NatureDrill-Mix features:
- Variable design geometries (single shaft, wall, block)
- Variable execution parameters depending on the types of soil
- Deformation- and vibration-free production
- Optimal use of natural resources
The NatureDrill-Mix process
The production of soil mix elements using single-wall casings is entirely different from typical methods, as in-situ soil is mixed under double-rotary drills. Soil mixing elements are produced under the protection of borehole casings, meaning it is mixed in situ inside a casing drilled shaft using the double rotary drilling method. Mixing, in turn, is carried out with a special screw.
Production takes place in two phases. In the first phase, the double rotary drilling method consists of an external casing and the internal mixing screw (hollow drill pipe with mixing blades or shovels). The mixing shafts are drilled in opposite directions by two rotary drives mounted separately on a common drilling carriage in the mast axis. Since no soil material is to be extracted from the borehole, the mixing auger is relatively short and is used as a beginner to loosen and dissolve the ground. The tool above the beginner is formed in paddles or special auger wings to mix the soil with the binder suspension.
From the start of drilling, the cement suspension is pressed in through nozzles at the lower end of the mixing screw, resulting in partially mixed-up soil. The soil is mixed up with the suspension by continuous, counter-rotating screwing-in of the casing and mixing auger under constant addition of suspension.
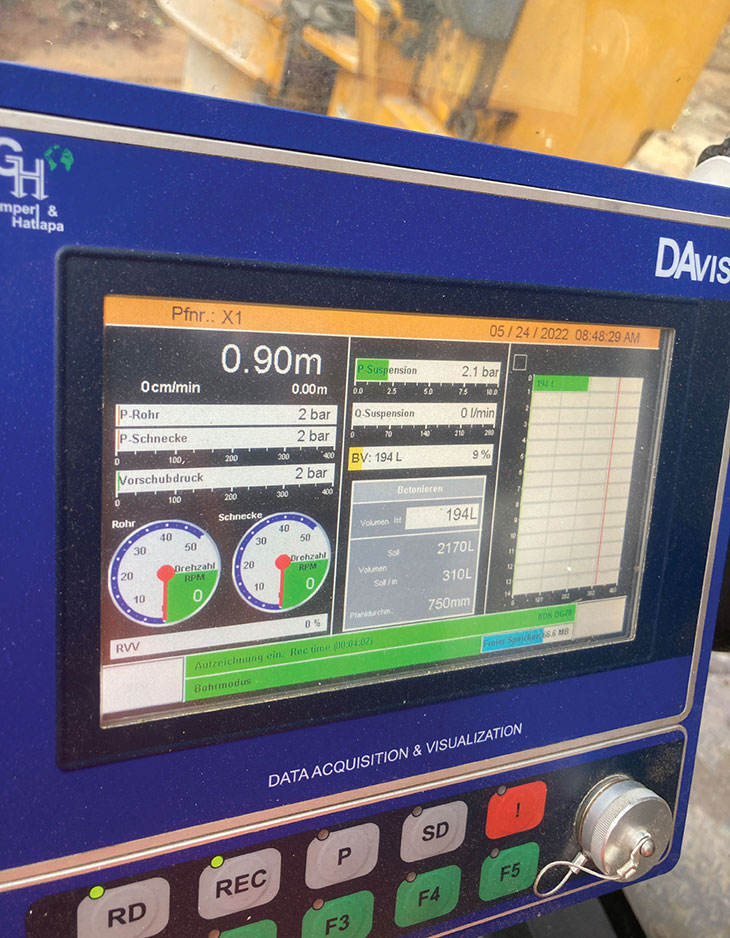
In the second phase, after reaching the final depth, the direction of rotation, casing and mixing auger changes, and further mixing of the soil is carried out in the same way as previously described. Like the drilling-down process, the binder suspension is continuously pumped while removing the casing. Hence, the pre-mixed soil is again improved, creating a homogeneous mortar column. The element’s defined diameter corresponds to the casing’s outer diameter. Depending on soil conditions and mixing depth, diameters can be designed from 50 to 120 centimetres.
Through this procedure, the soil-binder mixture is completely mixed within the casing over the whole length of the column (forced mixing) so that there are no undesired soil inclusions from the outside. Despite the mixing auger working at a slower speed compared to the speed of conventional mixing drives, the counter-rotation of the casing and mixing auger, and the high torque of the rotary drive, the soil-binder mixture forms a homogeneous mortar column. That’s why this process should involve high-power equipment and large-torque double-rotary drills.
Features and application
With the cased mixing system NatureDrill-Mix, most soil types, including cohesive soils, can be utterly mixed up with appropriate mixing tools. Steel profiles and reinforcement cages can be adjusted in the freshly mixed column to create a statically effective shoring system. The NatureDrill-Mix process can also be used when similar operations can no longer be carried out due to difficult ground conditions. This may be necessary for very dense soils where uncased mixing augers run out of the axis.
With the cased mixing system NatureDrill-Mix, most soil types, including cohesive soils, can be utterly mixed up with appropriate mixing tools.
In conclusion, the verticality of mixed-up columns by executing the cased method is much higher, in contrast to uncased columns.
From a geological point of view, the application of the method is limited to humus-rich soils such as peat, mud, digested sludge, etc. Like jet-grouting, such soils must be almost completely replaced to obtain a reasonably decent compressive strength and largely homogeneous elements. There is more to this than simply mixing the soil.
Quality assurance
Subsoil investigations are carried out in advance to ensure design and application quality. Concerning the mixing mode and the achievable features, soil samples are taken from different depths at different exploration points. These samples are then mixed in the laboratory with variable cement additions and tested for usability, as required for the project.
Suitable laboratory mixtures are used to perform test columns, which are tested for consistency and resistance before the structural columns are executed. These results are part of the design process.
During the production of structural columns, manufacturing parameters such as pressure, suspension quantity, revolutions, retraction and pulling speeds are continuously recorded to adjust the manufacturing when needed.
Samples are taken two times per workday to ensure the cement suspension’s required features are there and are tested for suspension density, which can also be used to check the necessary water-cement ratio.
Samples are taken from new columns daily and tested for compressive strength after seven, 14 and 28 days.
Equipment
Double-rotary drives and carrier devices with high engine power and high-power hydraulic units are necessary. The same features are required for double-rotary drilling. These are characterized by two separate gearboxes mounted on a carriage in the drilling axis, one above the other. The drive for the casing has a significantly higher torque than the internal auger drive.
NatureDrill-Mix process features
- High productivity
- No additives required (except for binders)
- Structurally effective shoring systems
- Usability in contaminated soils
- None or low soil discharge (except for humus soils)
- The variable layout of columns
- Any column grid performable
- Vibration-free
- Low environmental impact
Construction projects
The NatureDrill-Mix has been applied in several construction projects.
Project 1
On this construction project, the ground conditions featured fine gravel sands. Thus, a secant-pile shoring wall with a single tie-back layer was completed.
The pile elements had diameters of 750 millimetres (mm) and were executed as secant piles. Double U-beams were placed in every fifth element, resulting in a load-bearing shoring wall. A total of 1,900 square metres (m2) was produced in eight weeks.
Project 2
This construction site consisted of a dissolved wall with shotcrete fills with ground conditions featuring gravel sands.
The elements had a diameter of 750 mm and a mixing length of nine metres. Reinforcement cages were placed in the load-bearing mixed columns. A total of 2,100 m2 of the dissolved wall with load-bearing ‘NatureDrill-Mix’ system elements was produced in eight weeks.
Conclusion
Nature Drill and Borama Drilling Equipment are part of the Gollwitzer Group and developed the ‘NatureDrill-Mix’ system to replace traditional bored piles in almost all types of soil in the future. The intention is to offer a resource-saving process and avoid the disadvantages of bored piles, such as the extraction and removal of soil. In this process, existing soil can be used to produce pile elements.
Photos courtesy of Borama Drilling Equipment Ltd