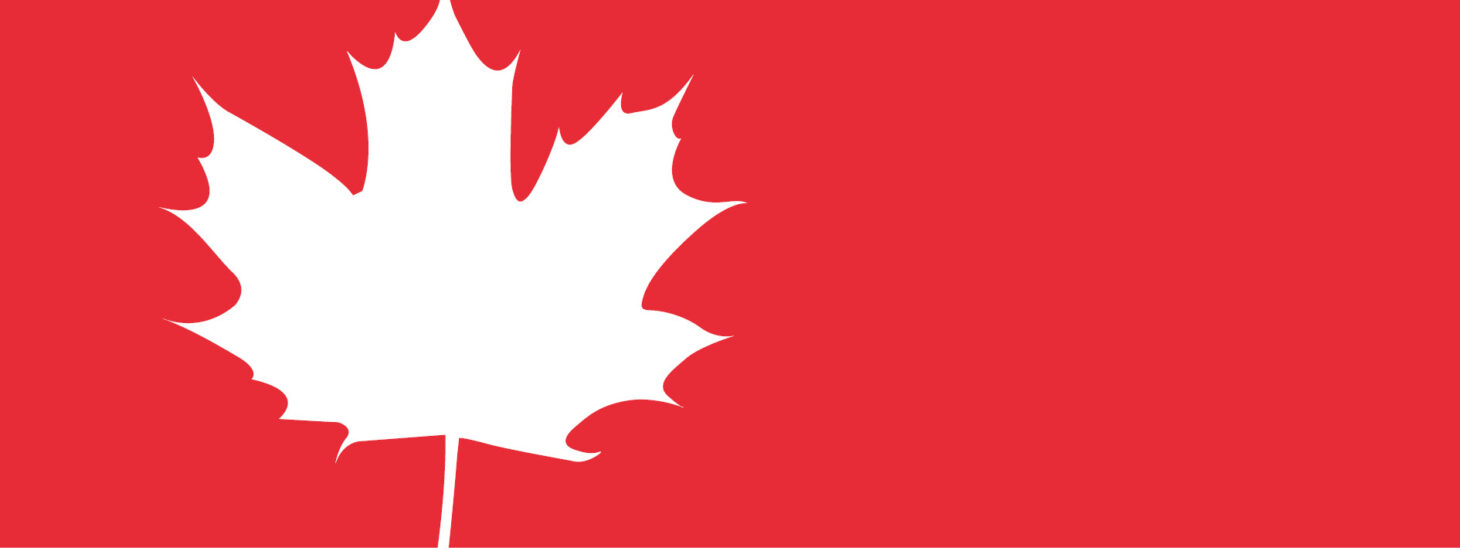
If you’ve been to Victoria, you probably know whether or not you’ve been over the Johnson Street Bridge. The name itself may not stand out, and it’s not as impressive as Vancouver’s soaring Lions Gate Bridge.
But the Johnson Street Bridge has its own unique charm and a rather steampunk silhouette (as well as a moderately well-used hashtag on Instagram). It is a 90-year-old, light blue, steel, road and rail and pedestrian bascule bridge that connects downtown Victoria with the area towards Victoria West (Esquimalt, View Royal, Saanich and points west).
The current bridge is being replaced by a sleeker, more seismic-ready and streamlined bascule bridge, but online commenters have already taken to express how much they’ll miss the old span when it’s gone.
After several years of talking about the replacement bridge, the project itself actually got underway in May 2013. The project’s website says the replacement is “the largest infrastructure project undertaken by the City of Victoria.” Elsewhere, the site states, “The new bridge will be the largest single-leaf bascule bridge in Canada – and one of the largest in the world – creating a new iconic structure and destination within Victoria’s Inner Harbour.”
The city estimates there are 30,000 crossings on the bridge every day, with 4,000 pedestrians and 3,000 cyclists also using the span. The main reason for the replacement is to meet the needs of a growing population by improving accessibility for pedestrians and cyclists. Also factoring in? Corrosion and obsolescence. Being a West Coast city, there are also aforementioned seismic adjustments needed. The value of the project is estimated to be just under $93 million, some of which is being provided by the Building Canada Fund and some from the Gas Tax Fund, amongst other sources.
The local B.C. firm of Construction Drilling Inc. (CDI), from the town of Duncan, further up the island, was chosen to do the foundation work for the new bridge, which includes the piling for the work trestle from which they were working and then the bridge itself – the drilling of 16 six-foot diameter shafts and the construction of the bridge’s piers. CDI is amongst one of the many island subcontractors working on the job, the main contractor being PCL Constructors Westcoast. CDI has been onsite since mid-summer 2013, and will be there until the job is almost complete.
CDI itself was started in 2005 by Gary Henshaw (formerly of Pacific Pile Driving) and Robin Pedersen, and currently has about 50 employees. The company isn’t just confined to projects that take place on the island; they do work all over the west and down into California.
As with every job, there have been challenges with the Johnson Street Bridge project. If you check out the site on Google Maps, you get a sense of the crowded conditions of the project; the site is an active harbour channel and a federal waterway. Then there’s the deep and immediate slope of the drilling site and the combination of soft overburden and hard rock underneath.
“One of the things with this project in particular [is that] Victoria has some of the hardest granite,” said CDI’s Kelly Smith. “It’s anywhere from 45,000 to 50,000 psi. We’ve run into similar conditions in Ontario and Nova Scotia. That’s [also] what makes this project unique. In particular, with the rock profile, it’s very undulating. There’s very steep slopes, vertical cliffs, (angles) from 30 to 45 degrees.” Not to put too fine a point on it, those slopes can occur within a single six-foot drilling site. Smith said that “the other challenges would be working off a work trestle … Access is a challenge, one of the biggest. The existing bridge is still operational. They had enough room to build the bridge just to the north.”
Because of the site’s lack of elbowroom and other particulars of the job (dealing with the size of the casings, for instance), the team couldn’t just “wing it.” They came up with solutions, like setting up an automatic welding station onsite and using the old, decommissioned E&N rail lines for carrying the materials.
“The main span of the rail was removed prior to us beginning construction. PCL decked the approach trestle with 12 by 12 crane mats for use as a work platform,” said Smith. “The work trestle is so confined. Every shaft location had to have an intricately drawn-out work plan. When there wasn’t enough room, we brought along a barge.”
One thing to come out of this project for CDI was the solution to one particular problem. “We developed a system for making that transition from overburden to rock – for making that work using both hardware and technique, purpose-built tooling for this project,” said Pedersen.
Smith says what they came up with allowed them to install casing within tight vertical tolerances into extremely hard sloped bedrock. “It solves the problem of not being able to install the casings within specification, eliminating risk and allows us to do it within a fraction of the time it would take using conventional methods,” he said.
Like that old washing detergent commercial, though, the proprietary method CDI has developed is similar to “an ancient Chinese secret”; the team is unwilling to say exactly what they’ve come up with.
By way of explanation, Smith later wrote, “CDI had to develop a technique to consistently seat 33m x 1.8m x 25mm caissons within the tolerance of 15mm per metre into sloped (up to 45 degrees), hard bedrock (50,000 psi). We successfully installed all of the shafts on the project within the specified tolerance. An added challenge to seating the casings on this project was, due to the sloping nature of the bedrock, the casings had to be embedded two metres into rock to achieve a seal and make it possible to advance a rock socket through the bottom of the casing.”
Another one of the challenges was the size of the casings, because of their length (110 feet), weight (84,000 pounds) and the setting of the project itself.
“Once the casing was vertical, as per the lift plans, everything was so large and heavy, it had to be approved,” said Smith. “We would then advance the casing, which was so heavy that it would sink nine metres down on their own weight. We would launch the pipes out, pick them up, swing them around to the work trestle, then stand the casings up. When we swing them around, we would swing them into the harbour, watching out for boats, kayaks and small ships.
“We had to meet a schedule; it’s a working channel. The area that we have to work in is quite confined. There’s limited windows when we can actually block the harbour and go in… an hour at a time.”
According to Smith, the job went like this: The casing would be erected on the material barge with the crane and was placed into the oscillator. With the oscillator, the casing was advanced until it hit the bedrock and then installed up to two metres into the bedrock, as mentioned. The BHA and cutter head (with the Wirth unit attached), using a reverse circulation drill system, drilled the rock socket.
The water for the reverse circulation drill system was delivered at 3,000 lph, and flushed the inside of the shaft; water was left in the shaft for stability and to maintain positive head pressure. The shaft is then cleaned and flushed at least four times. Video inspection is then done, making sure the standards are upheld, and then CDI is presented with a 48-hour window to install the rebar and pour the concrete.
For the next step, said Smith, “The rebar cage arrives in two pieces and is spliced over the hole. The first section hung into the hole while the second is stood hung and placed over the first section. Once the cage is spliced, it is lowered seven metres below the working elevation of the work trestle. It is aligned and hung in place in preparation for the concrete pour. CDI designed a special hanging bracket for the rebar cage to ensure all of the project specifications were met – elevation alignment and uplift.”
According to Smith, the shafts were filled via the Tremie method, with the water being displaced by the poured concrete gathered for treatment and disposal later. “Because the concrete pour elevation is below sea level, it was imperative to keep a positive head pressure throughout the entire pour,” added Smith.
There were other considerations on the project. Being on the site of an active federal waterway and a historical area of heavy industry meant that there were specific ways to handle the overburden. According to the project website, “Contaminated soil does exist around the bridge. The city has been working with an environmental monitor to ensure the environment and marine life remain protected throughout construction. Any contaminated soil will be dealt with in accordance with regulations.”
The projected date of completion is March 2016. The city estimates that by the end of 2015, the new bridge will be open to the public, while the final touches around the site are finished. And CDI can say that they contributed to the new Johnson Street Bridge, one that will hopefully become as iconic as the old one.