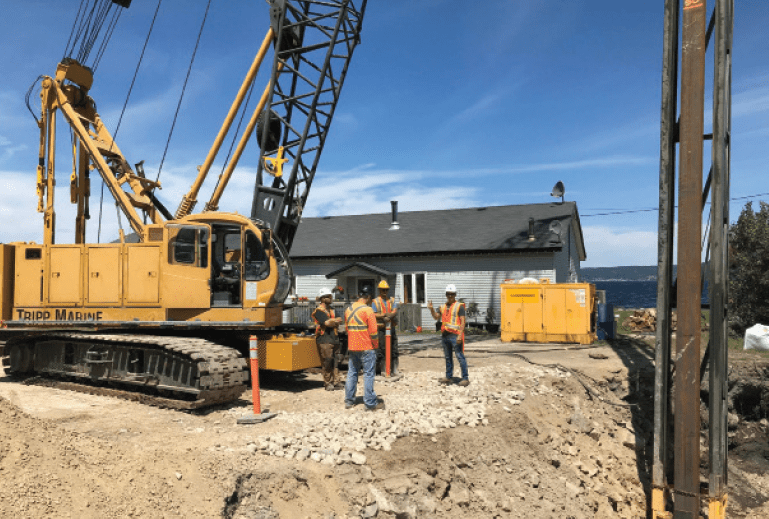
A simple, cost-effective system provides the best solution for Tripp Marine on a tight jobsite
In the summer of 2019, Complete Concrete Solutions (CCS) of St. John’s, N.L., won a bid to demolish and replace an old bridge crossing a 40-foot-span at the mouth of Cammies Brook in Humber Arm South, about 17 kilometres west of Corner Brook, N.L. Built about 60 years ago, the original bridge was so deteriorated that it wasn’t worth repairing, says Pyne Tripp, whose company, Tripp Marine, was subcontracted by CCS to complete the pile driving for the project.
Tripp and his company’s co-owner, Adam Bertrand, are both Red Seal mobile-crane-certified and have worked together for the past 20 years throughout Eastern Canada out of Corner Brook with a crew that now includes a first-year apprentice and a welder.
The old bridge had been built on a fairly large concrete mat, but not on piles, “and there may have been some settling. I suspect not much concern was offered back then in the way of supporting a small bridge such as this one,” said Tripp, but since the late 1950s, technology and building standards have changed. “Now soil borings can tell how close bedrock is, what kind of material is below the bridge and whether piles are required or not.”
In this case, there was quite a lot of soft ground below the bridge and the geotechnical survey indicated dense silty sand and gravel. He said, “The new build had to be done correctly – and as we all know, there’s no beating a structure constructed on properly driven pilings.”
Tripp Marine worked with David Zanchetta, sales and field services representative for Berminghammer Foundation Equipment of Hamilton, Ont., to determine the best equipment for the job. Since dynamic monitoring had to achieve a factored axial compressive resistance of 1,000 kilonewtons (kN) ultimate limit state capacity on at least four of the 12 driven piles on each side of the abutment, Zanchetta recommended Berminghammer’s BL26 box leads and its B21 hammer for the Cammies Brook project, noting that the B21 can provide about 1,000 to 1,600 kN ultimate limit strength.
“The B21 is 72 kilojoules [kJ] and the government had a maximum rated pile hammer energy of 84 kilojoules,” said Tripp. “We were driving a 12-inch 74-pound-foot H-pile and we couldn’t exceed that rating. The next size hammer, the B32, had 110 kJ.”
“Typically we’d recommend our Vertical Travel Leads on cranes or Excavator-Mounted Leads for excavators,” said Zanchetta. “They speed up the process of pile positioning and are easy to manoeuvre, especially for battered piles. However, it does take some time to put a system like that together, and it is more costly than simple hanging box leads.”
However, if firms already have a crane that can handle hanging box leads – one of the simplest of lead systems – that can be a good, budget-wise solution, Zanchetta says, since there is no connection to the boom tip or crane body, and the leads are relatively easy to set up.
“And with just about a month’s time required to deliver – and the lower budget due to the limited number of piles – it made sense for Tripp to rent something that could do the job relatively quickly; maybe not the quickest, but the most cost-effective for their needs,” Zanchetta said.
No fabrication required
Projects are going ahead, “but with extreme caution” in Newfoundland and Labrador because of the COVID-19 pandemic this summer, Tripp says. Travel restrictions between Ontario and Newfoundland and Labrador meant that Berminghammer was not able to send a technician to assist with the rig-up as anyone sent from the company’s home base in Hamilton would have to quarantine for two weeks.
“Instead, we held a virtual rig-up session with our technician hosting. We’ve done a couple more since, but it was the first time we did one that way,” said Zanchetta. “The technician was very methodical about outlining the process of putting the leads together and the operation of the hammer, and Tripp was able to execute with excellent production rates.”
“A system that has leads that attach to the boom tip offers lots more control, but it’s quite a bit more work to marry that lead system to a crane boom. The beauty of this system is that there’s no fabrication required,” said Tripp. “The box leads can be picked up by any crane and the swinging leads hang free from the crane boom, so you just stand them up and go to work.” Setting up and positioning each pile takes a bit more work, “so if we had 150 piles to drive, or if there were a lot of unforeseen subsurface obstructions, like rocks and boulders that were giving us trouble, we’d have to go with a different system. But this works great for smaller projects if the ground conditions are consistent,” such as at this site, where the geotechnical survey indicated dense silty sand and gravel.
CCS had built a temporary one-lane rock-fill bypass road equipped with a stoplight 25 feet away from the site to redirect traffic and free up the old bridge for demolition and replacement by the new 60-foot-long span.
“The sheer tightness of the site was shocking – I’ve never had such a compact jobsite before,” said Tripp, who has been in the pile driving industry for more than three decades. “Not only were we restricted by the bypass route, we had houses nearby, including a house that’s only 30 feet away from where the crane [was] set up. There was barely enough room to lay down the box leads.”
Although overhead wires had been moved in preparation for the project, “They didn’t move them far enough away so that we could work from both sides of the river,” Tripp said.
Where the project occurred, Cammies Brook is about 40-feet-wide. He said, “Not a very big span – we could reach it easily,” with the Kobelco CK 850 lattice-boom crawler crane selected for the job. “We’d have no room if we had a truck crane – it couldn’t be done. But this crane rotates on tracks, so that wherever you work, it’s clear 360-degrees around and there’s no excess machinery to make the jobsite more cluttered than it already is. So when I pick up the H-piles to load them into the hammer from the neighbour’s lawn where we place them alongside of the road, we turn 180 degrees and drive them.”
Innovative solution
For the pile driving itself, a temporary crane pad of gravel and processed rock was first installed on the west side to enable the equipment to angle-out to drive the 12 piles on the east side. “The tidal range here in western Newfoundland is about five feet, and the jobsite floods at high tide,” Tripp said. So an earthen barrier created out of 1,000-pound plastic sandbags was positioned around the crane pad, with a pump running continuously down in the hole while the work proceeded.
“The first day setting up we noticed that the crane pad was off level, which wouldn’t do for 110 feet of lattice boom with a diesel hammer, and the available gravel didn’t quite fix it,” he said, “So we used 20 oak crane mats for the first part of the project – that was the first day.”
Once the survey team marks where each pile goes with survey sticks at the centre of each pile, Tripp says, “you drive them free.” The piles had to be driven on a 1:4 batter, he adds, not plumb, “but the flying leads don’t mind that at all. You get the boom down and easily get the batter you need.”
When the piles for the first phase were driven and tested, the temporary crane pads removed and the land paved, reconfiguring the equipment took about a week. Tripp said, “We then drove the west side piles where we’d been sitting to drive the east side piles. Newfoundland is amazing!”