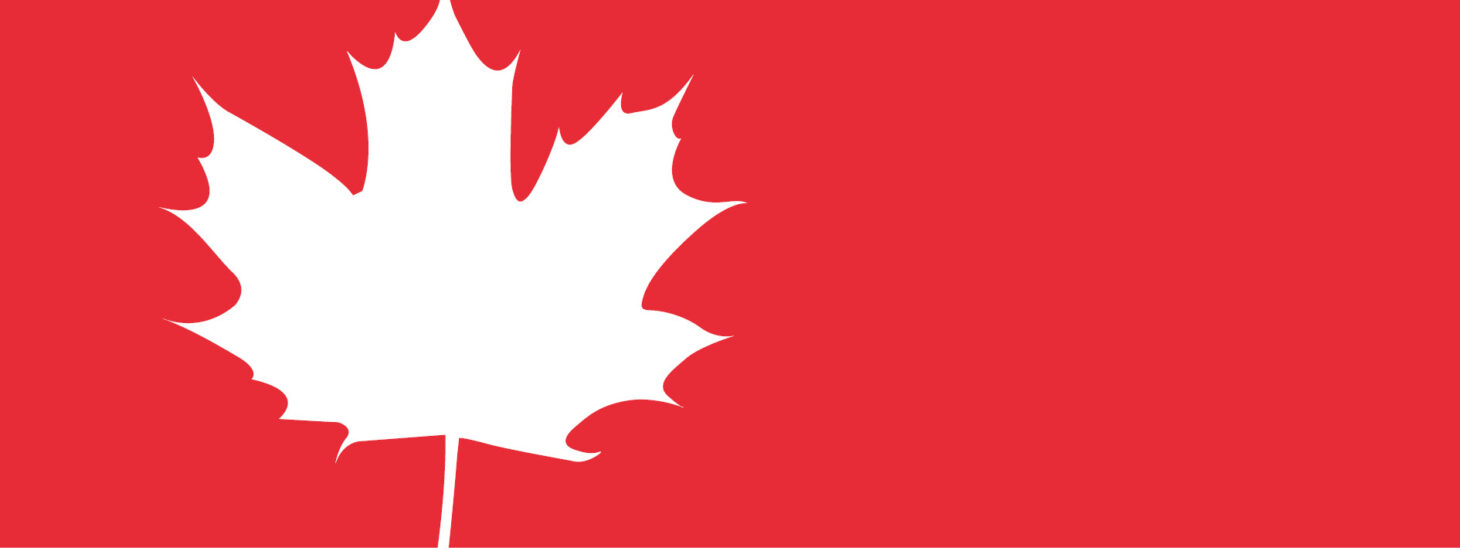
Drilling 67-foot shafts and installing large-diameter caissons into solid rock can be a challenge for even the most skilled drilling contractor. Doing so in an extremely remote location nearly 400 kilometres (250 miles) from the nearest town as winter weather quickly encroaches adds a new level of complexity. Steep cliffs, demanding soil conditions and limited equipment repair services meant the project team was forced to adjust the project’s trajectory on the fly. Without cell coverage, crews communicated with each other and the concrete batch plant via two-way radios.
Crews from Sharp’s Construction Services (Leduc, Alta.) and Henry Drilling (Langley, B.C.) joined forces to drill the foundations for transmission towers for the new 344-kilometre (213 miles) Northwest Transmission Line project in B.C. The work was performed under the general contractors’ joint venture of Valard Construction (Edmonton, Alta.) and Burns & McDonnell (Kansas City, Kan.) for the owner BC Hydro.
The monopole and self-supporting towers, each averaging 27 metres (88 feet) in height, are along a route that traverses steep hillsides, crosses rocky plains, dips into marshlands and meanders through a creek. The project is the longest transmission line in BC Hydro’s new capital management plan.
Well-equipped
The drilled shafts ranged from 167 to 304 centimetres (66 inches to 120 inches) in diameter and were spaced approximately 300 metres (984 feet) apart across a total distance of 40 kilometres (24 miles). A slew of equipment – from lattice-boom crawler cranes, hydraulic crawler cranes, drills, excavators, vibratory hammers and loaders – was deployed to tackle the job. Sharp’s and Henry Drilling crews used three Soilmec drilling rigs – the SR 80, the SR 65 and the SR 50 – to drill through a variety of soil conditions. Soilmec designs and manufactures a broad range of equipment to provide high performance for even the most technologically complex and challenging projects.
The SR 80 was deployed predominantly on large-diameter shafts between 250 and 300 centimetres (98 and 118 inches) through rock and hard soil, while the more nimble SR 65 focused on smaller diameter holes and rock holes that were perched on ledges and blasted shelves. The SR 50 was used to drill smaller shafts – most between 120 and 182 centimetres (48 and 72 inches) in diameter – through softer soil. The SR 50 enabled the team to deliver an average of one shaft per day, while the larger SR 65 and SR 80 were battling difficult drilling conditions through solid rock for upwards of a week per location.
Rock stars
With minimal geotechnical information available, crews had to assess drilling conditions on the fly. Over the vast 400-kilometre distance, the team naturally encountered soil conditions ranging from peat and soft silt overburden to gravels and heavy boulders overlying competent rock and fractured rock up to 15,000 psi in strength. Gravels were very loose in places, and to provide permanent casing, contractors had to seat into the highly sloped underlying rock to place rock sockets into the material. On the larger, 300-centimetre (118-inch) shafts, crews often had to pre-drill with 76-centimetre (30-inch) cored holes around the perimeter, then follow up with 300-centimetre (118-inch) core barrels. The team used every tool at its disposal, including vibratory hammers and cranes, to seat the casings. In some situations, the casing was modified and rotated into place with the drills. Luckily, the team had the three Soilmec drills onsite – each with varying capabilities – that allowed the crews to address any condition they encountered.
Aside from the rock foundations, some of the most challenging drill locations were the approximately 15 sites in the marshy area in and around Snow Bank Creek. Along the shores of the creek, to accommodate high groundwater conditions, workers used tremie pours to place the concrete. Water was removed with a hydrovac and delivered to a nearby retention pond where pH levels were tested and the water was conditioned before being discharged back to the creek.
Sharp’s and Henry Drilling workers also drilled three shafts in the creek bed itself – a feat that required even more preplanning. Here, workers built a cofferdam around each site and shocked the water with an electrical charge to stun any fish or tadpoles so that they could be collected and relocated. Then, the water was pumped into tanks and the cofferdam filled with crushed rock before drilling commenced.
Remote drilling solutions
The remoteness of the transmission line’s location and the driving rain that soon turned to snow as the job progressed combined to make the drilling work even more challenging. While crews shivered through inclement weather, the Soilmec drilling rigs continued strong, keeping the team on track even though the project’s schedule was considerably shortened.
The original timeline had called for drilling crews on the ground in March 2012, but that plan was delayed due to heavy snow pack and administrative obstacles involving material supplies. The drilling team mobilized in July and began initial drilling towards the end of August. By the time work began in earnest, it was September, leaving workers with only a small window to complete the contract before winter weather drove them out. The originally planned 21-days-on/seven-days-off schedule quickly shifted to 100 per cent “on,” with multiple crews needed to work daily 12-hour shifts. On the more difficult structures, the drilling teams worked 12-hour shifts day and night to complete all critical foundations. The Soilmec equipment stayed the course throughout these rigorous shifts, with the only significant equipment issue being the frequent replacement of drill teeth as the hard rock battled the augers.
The closest town with any kind of equipment parts was a four-hour drive away. Sharp’s and Henry Drilling deployed storage containers – delivered by Soilmec via Champion Equipment Sales – with extra parts, components and tools to the site to make sure the fleet of equipment was kept running smoothly.
Compressing the drilling schedule wasn’t the only thing that helped the drilling team make up for lost time. Valard Construction purchased a Cemco 275-2D mobile batch plant that was placed central to the drilling operations and used a fleet of five trucks to deliver the material where it was needed. The location of an onsite concrete batch plant lessened concerns and potential delays that could be encountered by transporting concrete long distances.
The project team was also able to come up with a way to transport drilling equipment that saved considerable time. Because of the difficult terrain and the location of nearby power lines, it was not possible to shuttle large equipment and tools from hole to hole intact. Instead of fully deconstructing the equipment for each drill site, crews used an 85-ton low-bed truck to help move the equipment. Soilmec drilling equipment is designed precisely for easy rig-up/rig-down, which reduces the amount of wear and tear on the drill rigs. By only rigging down portions of the equipment, the team was able to save both the client and owner valuable scheduling time, shaving weeks off an already compressed schedule.
Despite increasingly encroaching winter weather and the severely shortened timeframe, the project team still managed to complete the contract on schedule, and even included 16 of 20 additional drilled shafts added by the owner before the arrival of avalanche control crews, who signaled it was time for the team to leave the area.
Watch a video about this great project.
About the authors
Kevin Sharp is the general manager for Sharp’s Construction Services of Leduc, Alta., a leading drilled shafts contractor. He founded the company with his father, Joey Sharp, in 1983. Sharp’s was purchased by Valard in 2006 and both companies were purchased by Quanta Services in October 2010. Quanta Services is a publicly traded company located in Houston, Texas.
Don Henry is the president of Henry Foundation Drilling Inc. (HFDI) based out of Langley, B.C., a firm that specializes in difficult drilled shaft and piling jobs. Don and his father Barry founded the company in 2007 as an offspring of D&B Auger Services Inc., which was founded by Barry Henry in 1979. Today, both companies are owned and operated by Don Henry and his brother Ken Henry.
John Wilson is a sales manager for Champion Equipment Sales LLC, which provides sales, service and technical support for Soilmec equipment in Canada and the western U.S. John can be reached at 801-824-7532 or john@championsales.net.