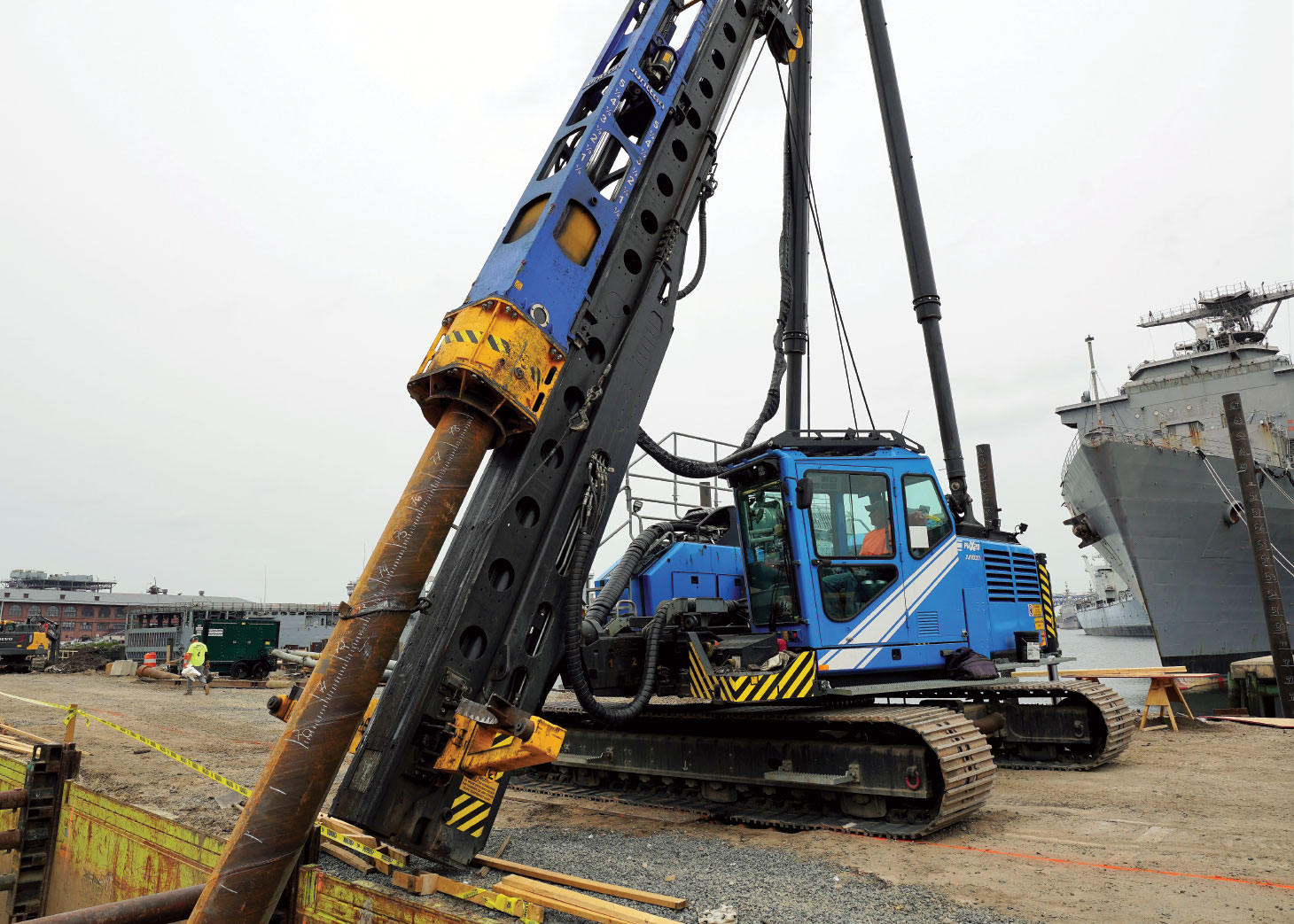
Why would an established highway contractor with a history of using a crane with a diesel hammer for pile driving be working at the Philadelphia Navy Yard with a sophisticated pile driving rig?
That would be a fair question by anyone familiar with James J. Anderson Construction Co., Inc. (JJA) and Junttan Oy, a pile driving equipment manufacturer.
Those familiar with the Philadelphia construction market tend to associate JJA with the region’s most established companies. JJA’s origins date back to 1981 when it was founded by Jim Anderson. Since then, the company has expanded its expertise into nearly every aspect of heavy civil construction. Expansion into new areas is in JJA’s DNA.
Broad Street Quay Wall project
The Broad Street Quay Wall project, owned by the Philadelphia Industrial Development Corporation (PIDC), serves as the gateway to a reimagined Navy Yard and represents an engineering feat years in the making. It includes two vehicle lanes in both directions, a two-way elevated bike lane and a scenic pedestrian plaza overlooking the Reserve Basin.
JJA’s rectangular 700-foot-long jobsite, located just inside the main gate of the Navy Yard, is a straight shot connecting Crescent Drive to Intrepid Lane. To the right, towering ships anchored in the square-shaped pocket of the Delaware River make most of the construction equipment on site seem small.
From an engineering standpoint, this project was necessary to stop the subsidence of Broad Street due to hydraulic erosion.
“The old seawall was cracked and leaking, allowing water underneath Broad Street,” said JJA’s chief engineer Bob Crawford, P.E. “This area undergoes a six-foot tide, so the water goes up and down in the Reserve Basin six feet twice each day. The tidal ebb and flow getting through the seawall was undermining the roadway to the extent that they had to shut down a portion of Broad Street.”

The joints in the existing cast-in-place concrete wall, located 20 feet apart, had widened over time. Small amounts of soil were removed every time the tide rolled out.
JJA has been working on this project since June 2022. “There was an existing concrete seawall sitting on a timber deck,” Crawford said. “Our overall scope was, first, to drive a line of NZ 38 sheet piles to create a new 700-foot steel seawall behind the existing concrete wall, then to remove the old seawall and timber deck on which it sat and drive 12-inch epoxy coated piles in front to support a new concrete pedestrian walkway.
“The new steel seawall had to be anchored to a concrete tieback sitting on battered piles. The tieback sits 50 feet behind the seawall. Three-inch diameter galvanized tendons go from the steel seawall back to the concrete tieback. Once that system and the utilities are all in, we reconstruct the Broad Street roadway, new sidewalk, bike path and pedestrian plaza.”
To build the concrete tieback anchor, JJA drove 79 18-inch and 79 16-inch pipe piles, designed to be 80 feet long and driven on a 2V:1H batter. During test pile installation, it was determined that there were locations on the project where the tieback piles would need to be spliced and driven more than 100 feet to achieve design capacity due to changing soil conditions.
“None of the pipe piles on the project are seated in rock,” Crawford said. “The 16-inch compression piles and 18-inch tension piles both derive their capacity from predominantly skin friction with only a minor contribution from end bearing for the compression piles.
“We’ve seldom done friction piles, so this was an experience to go through the test pile program and all the dynamic analysis iterations with urban engineers to determine that the production piles will attain the design capacity.”
From conventional to unconventional
JJA had never used a Junttan pile driving rig, but had seen them used locally and online. “JJA (typically uses) diesel hammers, air hammers, vibratory hammers and drilled piles installed with a crane, and our usual experience – primarily working for (the Pennslyvannia Department of Transportation) – is end-bearing piles to rock,” Crawford said.
Since past work was performed with a crane-mounted hammer, JJA was a first-time customer for Junttan USA.
In October 2022, Junttan USA provided JJA with a PMx28 pile driving rig with an HHK5S hydraulic impact hammer to drive the pipe piles, while the contractor simultaneously scheduled a rig from another vendor to vibrate in the sheet piles. When that rig became unavailable due to an emergency project, Junttan USA’s sales engineer Matt Eastburn saw an opportunity to expand the role of its rig.
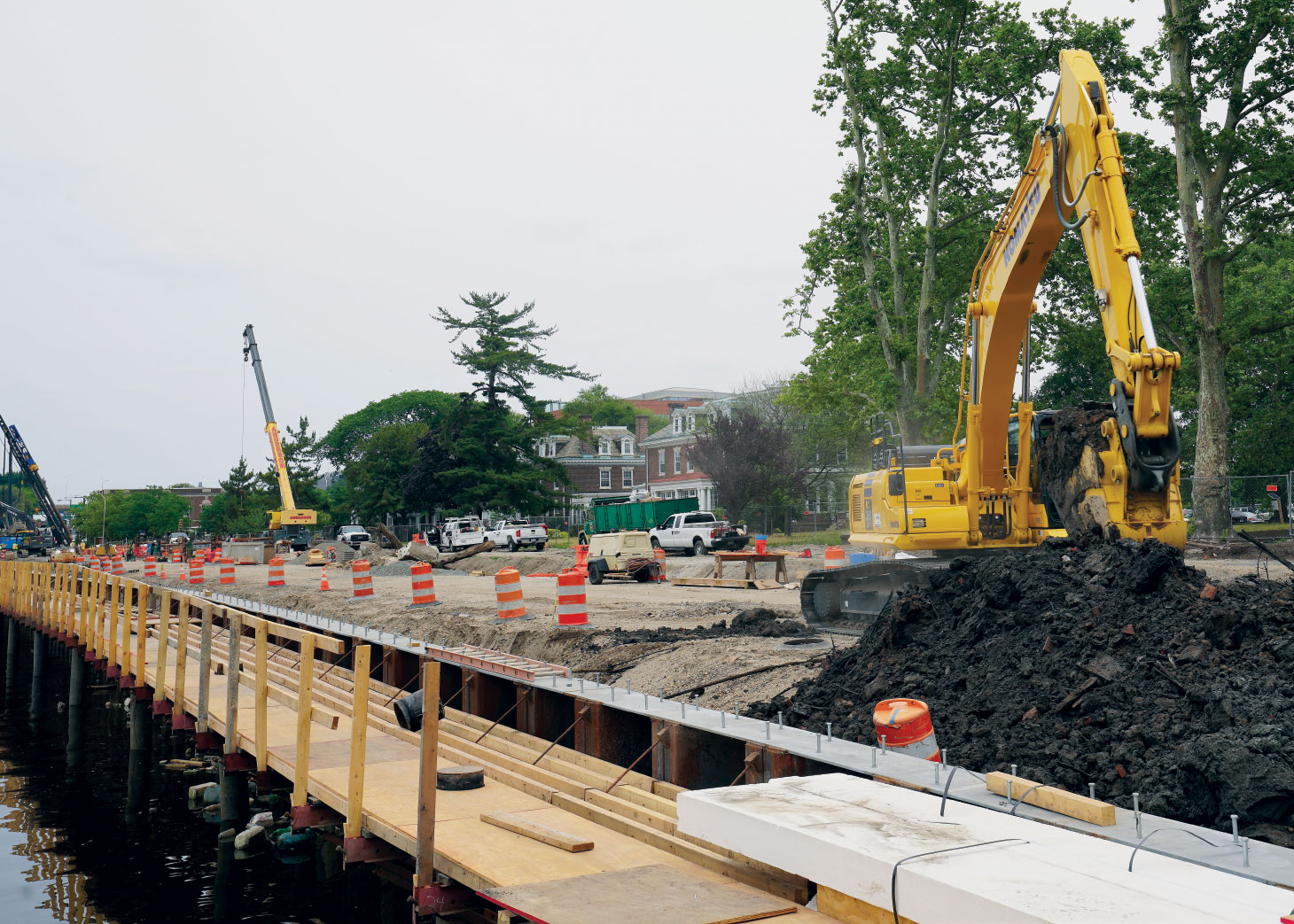
Junttan USA had never rented a rig with a vibro package and leaned on its partners in Canada to supply the package to be installed on the PMx28. The cross-continental partnership paid off.
“For the sheet piles, we had the rig equipped with a PTC variable moment hammer, so we had to mount the power pack on the back,” Eastburn said. “We took off the counterweight and essentially used the power pack in its place.”
Junttan USA had Junttan Canada ship the vibro and power pack to the Navy Yard, where the PMx28 was waiting. JJA provided crane support on the assembly. The transition between vibratory and standard pile driving was seamless. When the time came to drive the 16- and 18-inch-diameter piles, the vibro components were removed, and the counterweight and HHK5S hammer were re-installed.
Aside from a small portion where a Philadelphia Water Department culvert pokes through the seawall, all pile driving was completed using the Junttan PMx28. “We did all the engineering in-house,” Eastburn said. “Junttan USA installed the vibro kit, which was supplied by Junttan Canada. They had retrofitted it to a PMx28 they had in stock. Junttan Oy is always supportive of our companies, but their main role here was engineering work for the battered piles.
“The most challenging part of the engineering we had to do was the stability analysis to ensure that the rig wasn’t going to tip over while holding the 2V:1H batter and the 8,000-pound pile and 23,500-pound hammer. With the elimination of a portion of the counterweight, we were able to lay the leader back with a full-length pile.”
“Junttan was amazing,” Crawford said. “(Eastburn) did a balancing act with the weight of the hammer. I don’t know if it’s near the limits of the PMx28’s capability, but it’s probably pretty close to getting 26 degrees of incline and holding all that weight in place.”
Extreme battered piles
The key issue for JJA was finding an unconventional way to drive 80-foot-long piles on an extreme batter that was not labour and material intensive, says Crawford. “We’ve done battered piles before, but not quite this extreme,” he said. “At this angle, we would have needed significant anchored falsework to maintain the pile angle at such an extreme batter.”
Crawford also says JJA’s conventional equipment would have faced other challenges in this application. “We’ve had problems in the past with diesel hammers on significant batters. Diesel hammers tend to misfire when tilted. We don’t have that issue with the Junttan hydraulic hammer.”
“If we had done this pile driving conventionally with a crane boomed over those trees, it would never have happened.”
Bob Crawford, James J. Anderson Construction Co., Inc.
Although JJA has experience installing battered piles of lesser degrees, 26 degrees was a batter it had never encountered. This angle was necessary due to the heavy loads of large trucks and transport vehicles that will enter the Navy Yard on Broad Street. As these live loads will exert high lateral pressure on the new steel sheet pile seawall, they had to be counteracted by the battered piles in the tieback anchor. Due to the extreme batter, JJA required a follower to drive the battered piles the final few feet to grade.
Training supports production
Adapting to a new pile driving machine is no easy task for an operator. JJA’s operator, Steve, embraced the challenge and the pile driving productivity reflected that. Steve was familiar with JJA’s standard setup – a crane with diesel hammer. Junttan USA sent in a technician and provided on-site training, which included an in-depth assessment of the rig’s components and how to operate it. In addition to being a quick learner, Steve had studied the manual prior to training.
“Steve had quite the learning curve at the beginning, but once he got to know the machine, he was off to the races,” said Eastburn.
Since JJA had never used a Junttan rig, production was a serious concern, especially considering that the piles were to be driven with a 26-degree batter. JJA ultimately met or exceeded the estimated production for the installation of the sheeting, as well as the battered pipe piles.
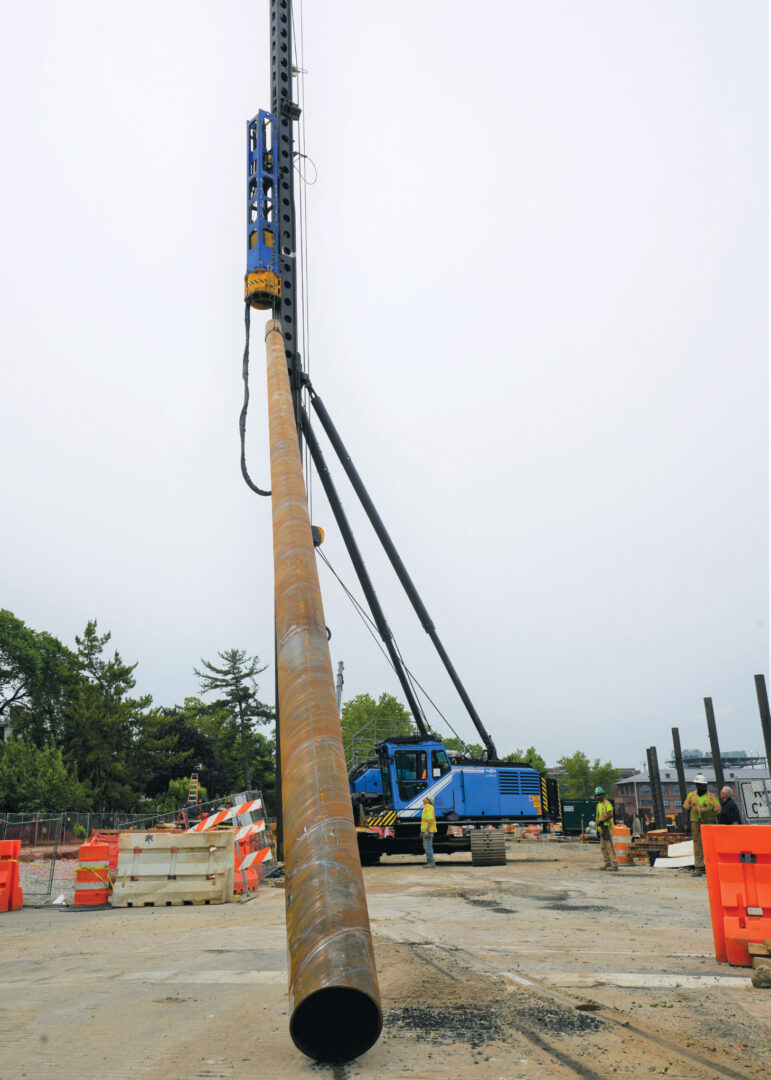
Although Crawford says the PMx28’s ability to hoist and drive piles without falsework was the main factor for choosing Junttan, the operator’s ability also played a big role. “There’s a learning curve, of course. But once it has been overcome, production reaches where it needs to be,” he said. The narrow 700-foot-long site also made using a crane-mounted diesel hammer with leads and bottom falsework prohibitive.
“The crane would have to be positioned to control the top end of the leads where a majority of the pre-driving weight is located,” Crawford said. “This would then require falsework at the bottom of the pile to maintain orientation and position. After completing one pile, we’d have to move the entire setup ahead every time. (Junttan’s setup is) self-contained. It holds the pile and moves it ahead without expending time to disassemble and reset falsework.”
The sheet piles were driven straight and accurately without the need for alignment falsework. After driving the steel sheet pile seawall, JJA connected a double-channel waler to the back of the sheet pile to accept the tieback tendon connections. The adjustments needed to attain proper bearing for the waler attachment were less than one inch.
Eastburn says that having a single rig offered JJA easier setup, better site access and less equipment to maintain.
“Our PMx28 setup is transported in three loads: one lowboy for the rig itself and two falloff loads on standard flatbeds for the hammer and counterweights. It requires a little bit of machine support to assemble, but once it’s set up, you can track back and forth to each pile on-site,” he said.
Under and over the Navy Yard
The Navy Yard operated as a U.S. naval base from 1876 to 1996, so it stands to reason that the underground conditions are as diverse as its history.
During installation of the 16-inch pipe piles for the tieback anchors, JJA encountered the remains of a 700-foot-long timber bridge from the 1800s about 11 feet down. The bridge had once connected Broad Street with this area of the Navy Yard, which was once known as League Island.
The Pennsylvania Historic Museum Commission determined that the underground structure had low historical significance, so JJA was permitted to put points on the 16-inch pipe piles to penetrate the bridge wall, which was comprised of six- and 12-inch timbers. The tips allowed the contractor to drive 16-inch piles through roughly two feet of wood using the PMx28.
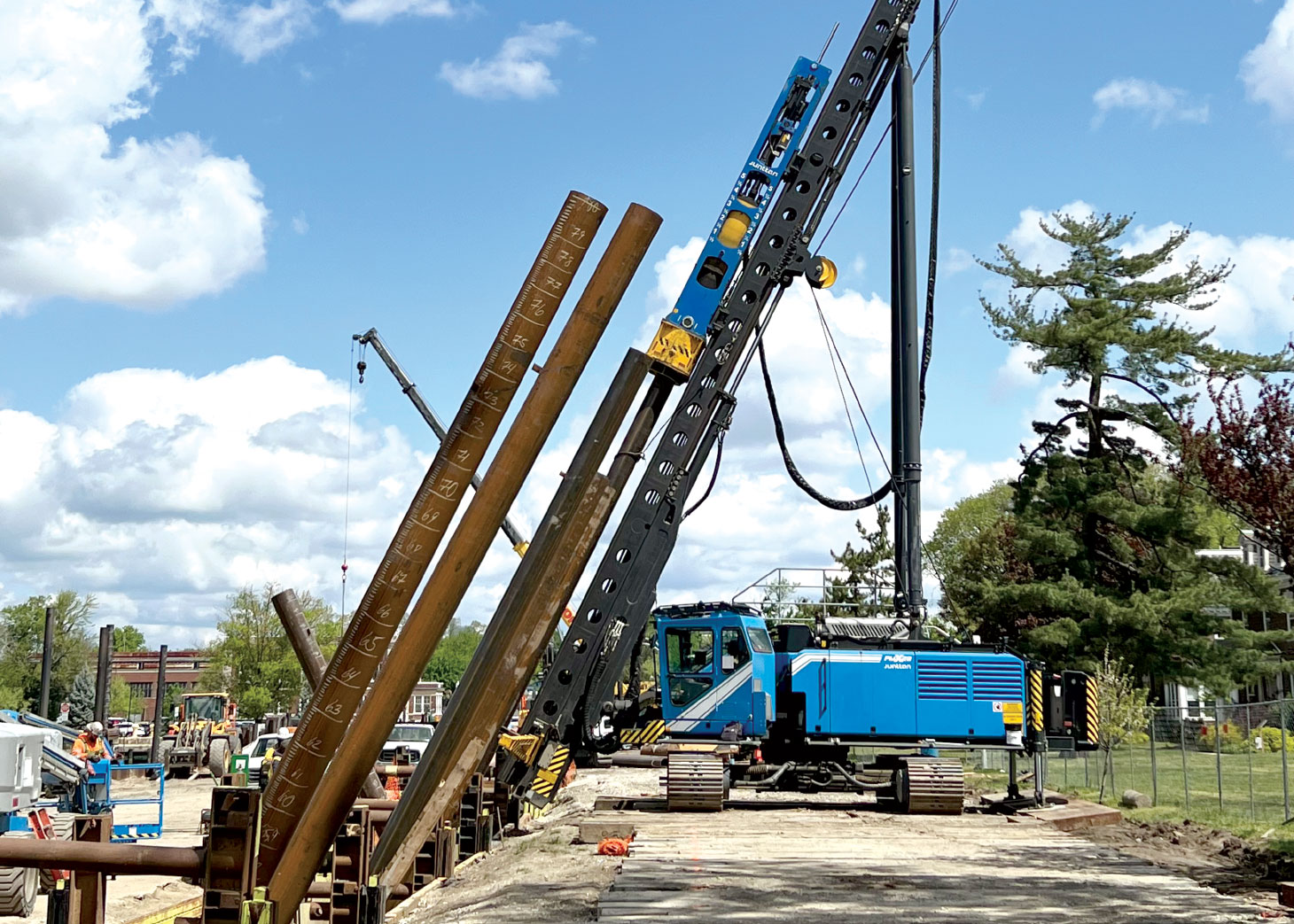
“If you’re driving a pile on a batter with a crane and leads, and a timber wall is there, the pile will slide down the wall trying to find a weak spot and then penetrate there,” said Crawford. “This pushes the pile off of its design location and orientation. The (PMx28) held it where it had to be, so we were able to keep the pile on its designed line while penetrating the wall. The point penetrated, and the hammer held up well under this added stress.”
The pile driving challenges were not just underground. The Navy Yard is densely populated with buildings connected by a labyrinth of narrow streets and 90-degree turns. Transporting 80-foot-long piles on a 100-foot-long trailer was a logistical challenge, especially with the historic sycamore trees that bordered the site.
PIDC agreed to prune the fronts of the trees to provide access for the piles and the Junttan rig.
“If we had done this pile driving conventionally with a crane boomed over those trees, it would never have happened. We don’t have the space or clearance to fit a rig holding a 26-degree batter through the tree canopies. Booming back just the mast of the Junttan rig where the trees had been pruned in the front worked for us, and more importantly, worked for PIDC,” said Crawford.
JJA finished its pile driving work with the Junttan setup in July 2023, but continued marching toward the timely completion of the project in December.
As drivers and pedestrians enter the Navy Yard, they will see freshly paved roads, newly constructed granite-clad walls with recreated stone piers and a new pedestrian walkway with extensive landscaping, but will never realize the complex geotechnical challenges below that were overcome by a forward-thinking project team and a willingness to break out of the comfort zone and engage with new equipment technologies.