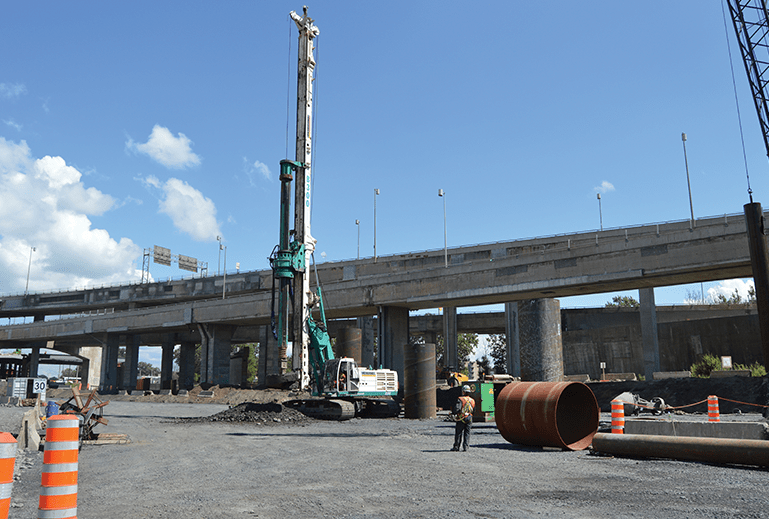
REVITALIZING A MAJOR MONTREAL TRANSPORTATION NODE IS “A HUGE 3D PUZZLE”
By Sarah B. Hood
The Turcot Interchange is the gateway to southwestern Montreal. Since freight and passengers entering the island city by rail or road have a limited choice of routes, more than 300,000 vehicles per day pass through this dense transportation network. It is the connection point for three highways, access to the Champlain Bridge and the ground route to Montréal-Pierre Elliott Trudeau International Airport. Montreal’s main rail lines also pass through the area.
But after decades of service, the Turcot Interchange was in need of rejuvenation, so, along with the Angrignon, De La Vérendrye and Montréal-Ouest interchanges, it has become part of the Turcot Project, one of the most complex transportation infrastructure upgrades ever carried out in the province of Québec. Ongoing since 2015, it is a massive operation taking place on four sites at once. The work is about 60 per cent complete and is scheduled to finish at the end of 2020.
“Turcot is like a huge 3D puzzle, so everything happens at the same time,” said Sébastien Marcoux, deputy project director for KPH Turcot, the company responsible for the design-build part of the project. “We’re talking about five million cubic metres of excavation and backfill, approximately 300,000 cubic metres of concrete demolition, 21,000 metric tons of structural steel, 45 structures, (including a cable-stayed bridge) and 440,000 square metres of concrete paving.”
The enormity of the undertaking is further complicated by the need to keep the roads and rail lines running, even while one of the highways is being relocated. But before any of the demolition and construction could begin, one of the first challenges was soil remediation.
“Turcot Yard used to be an old railway yard,” Marcoux said. “Every type of contamination needs to be managed differently.” Because the project is so large, most of the contaminated material is being reused as backfill on the job site. Of the approximately one million cubic metres of contaminated soil, about 90 per cent was reused, which greatly reduced the truck miles expended on the job.
“All our backhoes are equipped with GPS, so the operator of the equipment knows exactly where he is at all times. A 3D model of the ground was done, so it really helps us manage where we are,” said Marcoux.
He notes that a “huge spreadsheet” helps ensure that each section of the site that will be receiving fill is ready on time. It was based on information gleaned from 2,800 surveys that went into creating a soil management plan based on rehabilitation principles which was designed to limit the project’s ecological footprint.
Besides the contaminants, the geotechnical parameters of the soils presented their own challenges. “There used to be an old river, so there was also compressible material – clay and peat. In some instances, they went down to bedrock,” he said. This necessitated the drilling of close to 3,000 bore holes down to competent material.
However, of all the site’s unique qualities, the most challenging was certainly the need to maintain traffic flow throughout the project. Like a surgeon who must maintain blood circulation during a tricky operation, the KPH Turcot members (Kiewit, Parsons, CRH Canada Group Inc. and WSP) knew they had to keep the traffic moving seamlessly over the five-year reconstruction while roads, rails, ramps and bridges were being removed and rebuilt.
“It’s an extremely challenging project. When you look at it, it’s probably one of the most complex transportation jobs right now in North America because of the proximity of other structures,” said Marcoux. “We’re working in a very dense urban area.”
For everyone on site, movement is restricted because of the need to work with large pieces of machinery close to live transportation routes, pedestrian corridors and existing structures. In some cases, work has to be carried out underneath low structures. Vibration has to be carefully monitored with a seismograph or survey prism. Just one element of traffic management is the requirement to build 95,000 square metres of permanent and temporary retaining walls.
“The mobility is really at the heart of the whole project,” Marcoux said. “The schedule was developed around the mobility plan and the maintenance of traffic. One of the first things we looked at was how we were going to maintain traffic through the Interchange. The project is divided into five main traffic phases. The whole philosophy for us is that we need to build new or temporary structures, then switch traffic and demolish existing ones.”
Needless to say, the drilling demands of the project are significant, with a total of 375 10- to 20-metre shafts to be drilled, ranging in diameter from four to eight feet. Rebar density varies between 200 and 250 kg/m3. There have been notable successes. In 2017 alone, 110 shafts were driven, of which 80 were completed within the first six months.
Petrifond Foundations is the main subcontractor. To drill the shafts with a diameter of four feet or larger, they are employing a variety of cranes: LS-218H, LS-128, LS-308 and LS-108B, as well as the Casagrande B300 piling rig. In addition, they are using the ICE Model 44B vibratory pile driver and APE 250 high-frequency vibratory pile driver, with reamers and chisels for the rock and clamshell excavators to remove spoil.
Ramsol Construction is also working on the site, using the Casagrande B360XP hydraulic piling rig for 406mm-diameter micropiles and the Casagrande C9 crawler drill with a down-the-hole hammer.
“We’re driving a lot of rolled steel caissons under existing structures because we want to build before we demolish,” said Marcoux. Sealing difficulties caused by fine sand and silt infiltration were solved by ensuring the caissons were sealed properly into the bedrock.
Also, “it’s important to maintain the water pressure in the shaft to keep the sand out,” he said. “The water level should be higher than the groundwater to avoid sediment infiltration. If needed, we put more water into the shaft so it stays above the existing water level.”
With the high water table, “water management is key,” Marcoux said. Water quality in the shaft is tested for such contaminants as suspended sediments, heavy metals and hydrocarbons. Any water discharged into the local sewer system must meet quality standards set by the City of Montreal. In cases where the water is not compliant, it is extracted with a vacuum truck and transported to an appropriate alternate site for discharge.
Another important success was a design optimization that allowed for a reduction of shaft length from 30 to 14 metres by using the friction of the soil instead of the end bearing capacity of the rock. Typically a metallic shaft is drilled and sealed to the bedrock; a socket is then drilled into the bedrock, and a reinforcement cage is installed into the shaft. Concrete is then poured into the reinforced shaft.
The socket makes it possible to mobilize the lateral capacities of the bedrock and thus resist to forces by friction, which has proven to be a very efficient solution to ensure high stability and resistance considering the challenging geotechnical and stratigraphic conditions of the site, with its layers of sand, gravel, silt, clay, backfill and organic soil over bedrock.
Requiring surgical precision and military-style planning on a gigantic scale, the Turcot Project is a valuable model for other projects to upgrade transportation infrastructure across Canada.