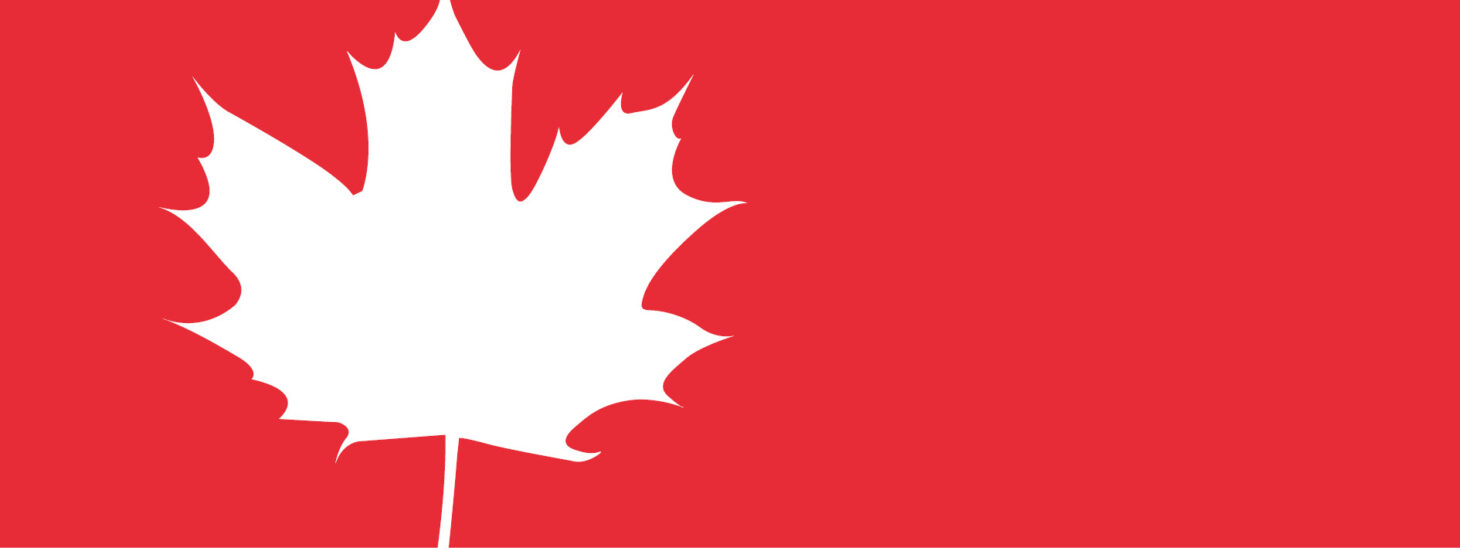
Toronto’s $456-million new Union-Pearson (UP) Express rail link is part of the most ambitious transportation strategy in the history of Ontario – a plan to deliver multi-directional high-order transit connectivity to the Greater Toronto and Hamilton Area, a region of more than six million people, and one that is projected to grow to more than 8.6 million by 2031.
The UP Express, which connects the two busiest transportation hubs of Canada’s biggest city from downtown Union Station to Toronto Pearson Airport, was funded through Infrastructure Ontario, which represents Metrolinx, an agency of the Government of Ontario created to improve the coordination and integration of all modes of transportation in the Greater Toronto and Hamilton Area.
The CA$129-million AFP (alternative finance and procurement, or public-private partnership) contract to design, build and finance the new Airport Rail Link (ARL) spur elevated guideway structure was awarded to AirLINX Transit Partners JV, a consortium of Dufferin Construction and Aecon, and included the elevated guideway between the existing GO Georgetown South Corridor to Toronto Pearson International Airport and other work. AirLINX chose Anchor Shoring and Caissons Ltd. to build the foundations for the new 3.3-kilometre spur line that veers off the Georgetown line near Woodbine Station and into Terminal 1.
Setting up and tearing down
“This was really an elevated roadway with a rail track on it,” crossing above major existing access infrastructure, said engineer Derrick Speakman, vice president of Anchor.
“We were going through industrial areas, on an easement beside Highway 409 that parallels the entrance of that highway into the airport, so there was no residential impact whatsoever. But the access conditions became more complicated as we came into the restricted area of the airport. The myriad roads coming into the airport looks like a spaghetti bowl from overhead,” he said. “So as we approached the airport, it became a much more logistically complicated job, particularly for setting up the machinery and locating ourselves away from the public roadways to allow us to complete our work.
A great effort by Anchor’s operation team was required as we spent a lot more time setting up and tearing down and a lot less actual time drilling. We also had to have more Greater Toronto Airports Authority (GTAA) involvement and approval in order to set up, because now we were beginning to impact some of their traffic patterns in and around the airport.” Occasionally, traffic lanes were closed throughout the project, but no roads needed to be closed.
The job was done more or less in sequence, says Speakman.
“[We started] with Column #1 and proceeding up to Column #70 with a few jumps in between. The Anchor crews would do one caisson at one location and then the next would be on the other side of a bridge,” he said. “We’d have to tear everything apart and put it on trucks, go underneath, pop back up on the other side of the bridge and do it all again.”
The crew would install one more caisson, and then tear everything apart and relocate to the next location. For the most part, it was one large-diameter caisson under each pier, with caisson diameters ranging from 1.5 metres to 2.4 metres and ranging from about 16 metres to 25 metres in depth, with rock sockets from between three and six metres in the Queenston shale bedrock.
An urgency to complete the job on time
There was a fair variation to deal with in drilling conditions but there were no surprises, says Speakman. “The geotechnical report provided a bore hole at each location, so we had advanced warning of any issue we might experience,” he said. Because of the variation in depths and some saturated conditions, different machinery and set-ups were used at each location, and the actual area of the work site was also a factor at some locations.
“[However,] it was a fairly conventional job once the right machinery was strategically chosen, a combination of conventional liner drilling techniques and the more current drilling techniques using segmental casing. We used Bauer BG40s closest to the airport where the work areas were quite tight and the depths of the caissons were the deepest. They also had the deepest rock sockets,” he said.
The Bauer BG40 can install casings in sections in advance of drilling without the need for a vibratory hammer. In the other areas, a Link Belt 218 crane with a Haines drilling attachment was used.
“If we were lucky there’d be two or three in a row,” he said. “There were 70 piers, but some had four caissons for each, so we had 79 caissons to do, about two or three a week.” The biggest challenge by far was the scheduling. “There was an urgency throughout the job to complete it on time,” said Speakman. There had been a promise that the UP Express would be ready for the start of the Toronto 2015 Pan Am/Parapan Am Games in the summer of 2015. Although Anchor’s own work was scheduled to be completed in 2012, a long period of testing also had to take place on the line before it could be opened for passengers.
“We would complete a caisson in the ground and right behind us would be the AirLINX JV pouring the column and eventually erecting the elevated guideway, which was basically a series of bridges from caisson to caisson to caisson – they were right behind our tail,” said Speakman.
A winning team
“The airport stands as a real landmark in Toronto, and everybody saw this thing rising out of the ground,” said Speakman, who notes that challenges that came up in the course of the job were accommodated and dealt with expeditiously by both the design and construction teams, and that the project did go according to schedule.
“I think that’s one of the advantages of a P3 and a design-build project. There’s no one party blaming the other party. The project’s success is a shared responsibility with all contracted parties and rests collectively with one winning team,” he said.
Anchor’s work commenced in June of 2012 and finished on Dec. 14, 2012, and at its peak the company had 30 workers on site. Despite the project’s demanding schedule and technical complexities, Speakman says that safety was of the utmost importance.
“Safety was a priority for both our firm and the JV partnership,” he said, and the Anchor crew did not have one lost-time injury on the project. “Completing such a complex job with zero injuries is a major accomplishment. It needs every single one of those 30 guys to work efficiently, effectively and safely, every minute of every day on the job.”