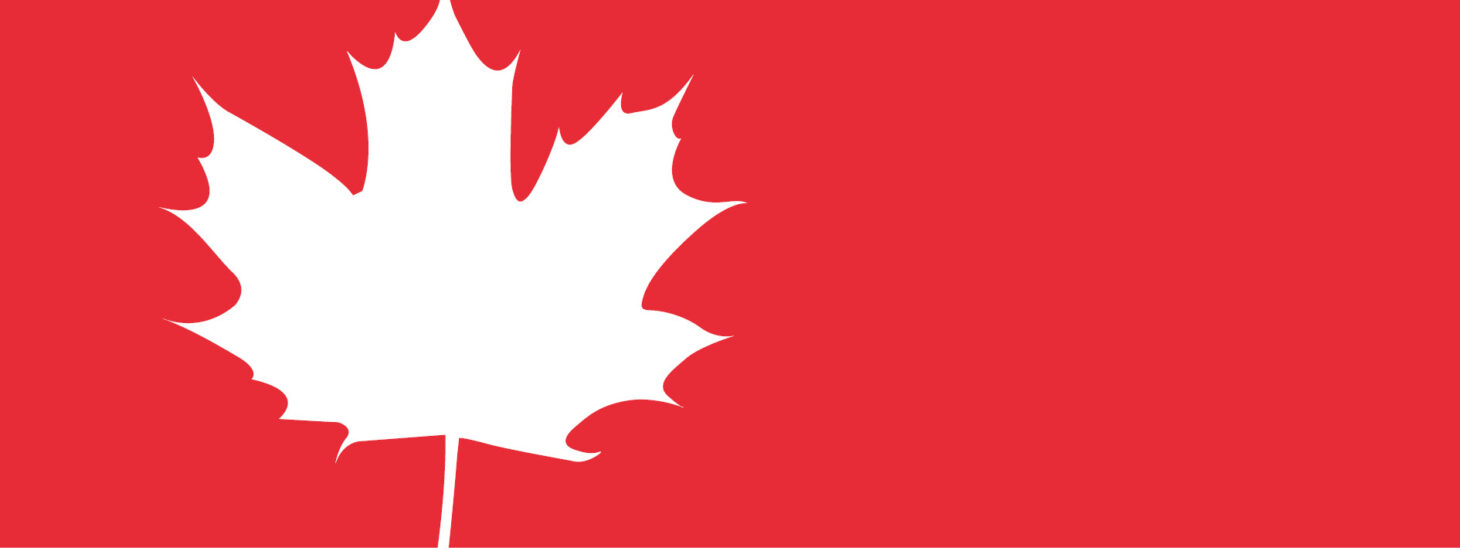
The best things in life are rarely exactly the way we imagine them. And the breathtaking Glacier Skywalk in Jasper National Park is no exception.
Back in 2010, Brewster Travel Canada put out an Expression of Interest to three construction firms to create a tourist attraction featuring a “cliff-edge pedestrian walkway” snaking its way along the Canadian Rockies. Though the initial concepts included cable- supported structures, when Dr. Simon Brown of Read Jones Christoffersen (RJC), a consulting engineering firm, and construction manager Scott Updegrave of PCL Construction Management took a trip up the side of the mountain, they were inspired to create a new design.
“After seeing what the site had to offer, we changed our minds based on the spectacular scenery,” said Brown. “We didn’t want anything above the viewing place to obstruct the view and we wanted to maximize the excitement of the glass floor element.”
These new requirements inspired a cantilevered structure that gets out of the way of the scenery and requires visitors to take a leap of faith in engineering before they step out to take in extraordinary vista. The first 300 metres of the walk are along the cliff and include three interpretive stations that tell the story of the environment. The experience culminates in a U-shaped glass-floor observation platform that extends 35 metres from the cliff and overlooks the Sunwapta Valley. Open since May 2014, it’s already weakened the knees of travellers the world over.
The design
The original cable stay concept was born out of Brewster’s requirement to mitigate any impacts to the environment. Updegrave says the team drew on their experience to come up with another type of design. “We build a lot of drawbridges and used some of those concepts to design girders that could be anchored into the cliff face and cantilever off the face by about 50 metres,” said Updegrave.
Brown says the design was mainly driven by engineering, but character was paramount. The bulk of the 21 tons of steel is weathering steel because of its minimal maintenance requirements and the fact that it naturally rusts, protecting it from further corrosion. It also has a reddish hue that blends into the colour palette of the cliff.
“We wanted a mottled appearance rather than a uniform one to blend into the natural surroundings as much as possible. We didn’t want it to compete with Mount Athabasca in the background,” said Brown. The design of the glass walk itself is unique: it’s a suspension bridge supported only on one side. “We get away with that because it’s curved in plan. If you look down on the vista, you’ve got that glass walk at the end in a roughly parabolic shape. It’s that shape that allowed us to run the structural system,” said Brown.
“It works because the suspension cable lifts the bridge up but also pulls sideways on it and that allows us to stop it twisting over,” he added. “The cable actually pulls it back in the opposite direction so it can achieve force balance because of the overall geometry of the structure.”
With a design concept in place, the team came together: RJC as prime consultant and structural engineer, PCL as project lead, construction and quality management, Sturgess Architecture as architect, Thurber Engineering as geotechnical engineer and pile drivers BAT Construction and Construction Drilling, Bluebird Contracting and Pacific Blasting among others who helped bring the project to life. The proposal was submitted October 2010, ground was broken in June 2012, construction was finished in October 2013 and the attraction opened in May 2014.
The construction
Before construction could begin, Thurber Engineering tested the rock quality and found it was basically competent lime- stone bedrock. They also mapped the rock face by lowering a basket from a crane over the edge of the slope and measuring the discontinuity orientations of the bedrock.
“Some of the layers dipped over the slope a little bit, which influenced the anchor design and depth,” said Stephen Bean, principal and geological engineer with Thurber Engineering. “The rock was relatively fractured which required more closely spaced anchors to tie the rock together so it behaved as one big unit instead of smaller pieces.”
PCL took it from there. Two big box girders were anchored to the mountain. The larger has twenty-six 46-mm dyad- wag bars anchored 20 metres down into the mountain. On the compression side of the girders, there are twenty-four 250-mm mini piles.
“A series of compression and tension anchors were driven vertically into the rock face. First, we had to blast out two Vee notches that were approximately 10 metres deep from the cliff. At the bottom of the notch, there was a level area that we built so we could place the drill rig and drill a series of holes that we put dyadwag bars in, grouted and stressed them,” said Updegrave. BAT Construction drilled and installed the anchors and piles 20 metres deep. After grouting and stressing the anchors, they drilled a large concrete swing on top of them. Reinforced and connected to the footing were 14-foot-long anchor bolts, 18 for each of the two girders.
The challenges
While most of the partner companies are experienced working in mountain terrain, this was one project that presented its own special challenges. The biggest concern by far was to preserve the pristine surroundings.
“There was requirement that no rock could leave the job site, so Pacific Blasting had to shave the rocks, which required finesse. They were able to shoot all the rocks to the far back side of the cliff face without losing any material down the mountain,” said Updegrave.
That’s when Bluebird Excavating came in to dig out the rubble and worked it out to the cliff face so that all the rock went back into the cliff instead of off of it. All went well until a big surprise was uncovered after some blasting: a zone of fractured rock. “We drilled some exploratory holes to see how thick it was so we could delineate the zone and modify the design. That’s where we came up with micro steel piles for that area instead of the original anchor piles,” said Brown. The micropile allowed them to transfer the load through the fractured zone down into deeper, more solid rock. Though the steel pipe piles were more expensive and had to be done quickly, it was the right solution.
Meanwhile, crews had to have their eyes out for other surprises. The area is also home to several herds of big horn sheep and mountain goats. Updegrave says they weren’t shy about sticking around during the construction process. “They weren’t bothered at all by the crews. If they wanted to eat, we just had to wait. There were studies done on that particular herd before and after the project and it was discovered that the population actually increased while we were working there, so I guess we didn’t bother them too much.”
Other challenges included: no Internet or cell service (they ultimately purchased satellite phones and a satellite dish), a Dark Skies policy, which meant work could only be conducted during daylight hours, an active roadway between Banff and Jasper and a short construction season (May to Oct. 31). The job also required precision planning. Most material came through Calgary, a day’s drive from the site.
“Everything had to be pre-planned and executed exactly the way it was planned. The girders were manufactured in Quebec City and staged in Edmonton, the steel frame for the glass came from Germany and had to be shipped and delivered at the right time, along with all of the other materials and equipment,” said Updegrave.
Secrets to success
Brown, Updegrave and Bean all agree that a giant team effort and individual expertise made this project tick from milestone to milestone. “Everybody knew their stuff. We hired the people with the right experience every step of the way,” said Updegrave.
The original design can take a lot of credit for the heart-stopping experience of stepping out onto 3.81-cm thick glass floor and taking in several glaciers, waterfalls and a severe drop to the valley floor.
“We wanted it with as much glass and as little structure as possible for the glass walk portion. We wanted it be a little scary, for visitors to get that feeling in the pit of their stomach that we had when we first went out there,” said Brown.
Mission accomplished.