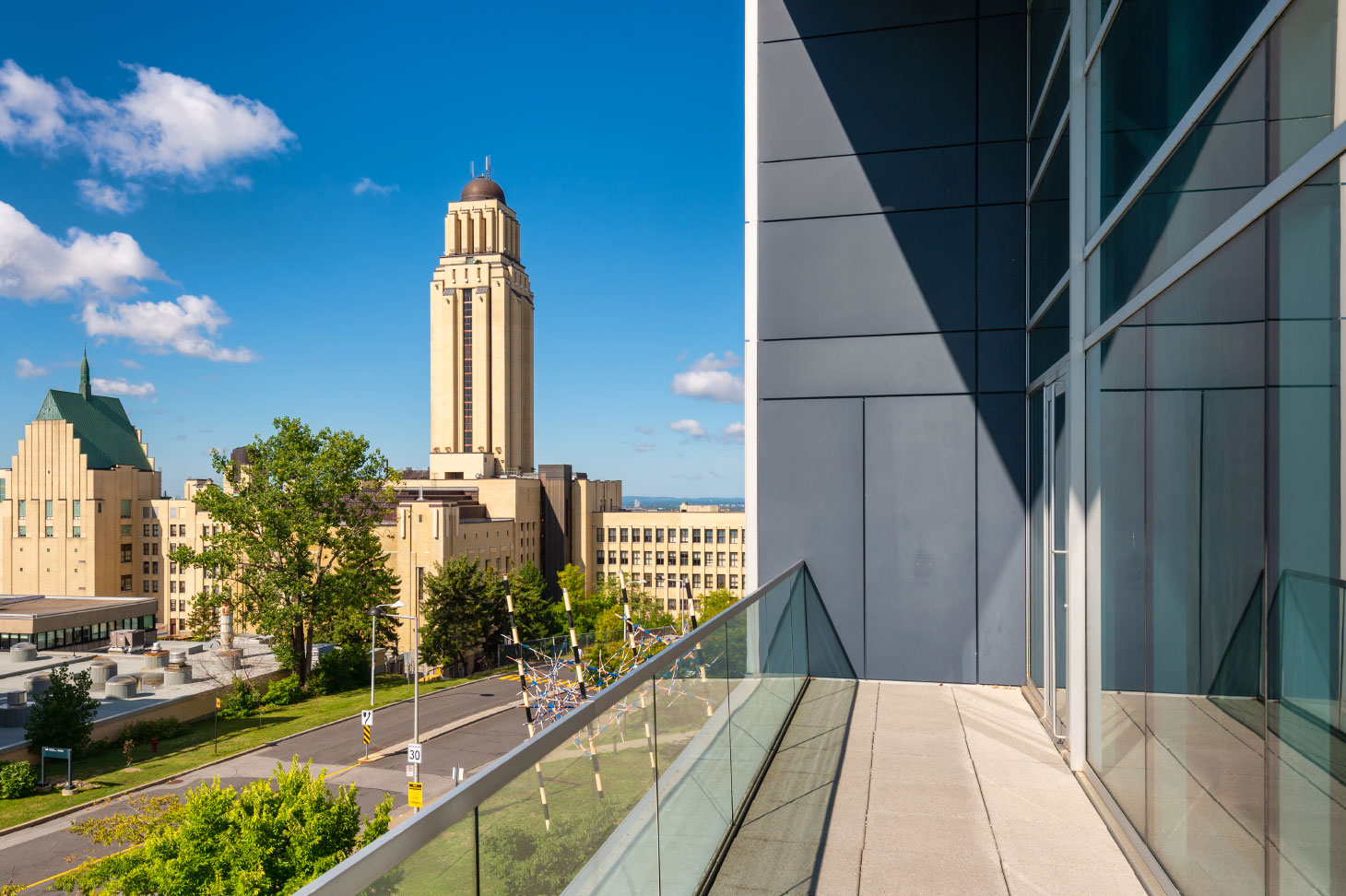
Dr. Pooneh Maghoul, P.Eng, and her former PhD student, Dr. Shihao Cui, at Polytechnique Montréal, have combined their expertise in civil engineering and acoustic data processing to tackle the challenge of characterizing the properties of deeply buried piles.
“We are primarily dedicated to providing non-destructive testing and monitoring services for piles in service,” said Maghoul. “During the monitoring process, we not only focus on the length of the piles, but also emphasize assessing their mechanical properties, which helps accurately estimate their health status. The work we do is crucial for enhancing the long-term safety and stability of infrastructure.”
One of the main challenges faced by the team in its research was how to best install sensors for monitoring deep-buried piles, as traditional installation methods could not be directly applied for effective sensor deployment. To overcome this challenge, they made use of flexural guided wave technology. Through the propagation characteristics of guided waves, they could effectively monitor deep-buried piles, as well as estimate their mechanical properties, by analyzing waveform data.
This method not only breaks through installation limitations, but also improves the accuracy and reliability of monitoring, thus providing more comprehensive data support for pile health assessment. What’s more, this innovative flexural guided wave technology also offers the possibility of reusing older, existing piles.
“Through non-destructive testing, we can accurately assess the status and condition of these old piles and then determine whether they meet the new design requirements,” said Maghoul. “This could potentially enable their reuse, reduce resource waste and lower project costs.”
Overcoming challenges
The inspiration to explore guided wave models for characterizing unknown piles stemmed from the practical challenges the team encountered in pile testing. Traditional pile testing methods – such as acoustic testing and impact response testing – are effective to some extent, but they have many limitations when dealing with unknown or deeply buried piles.
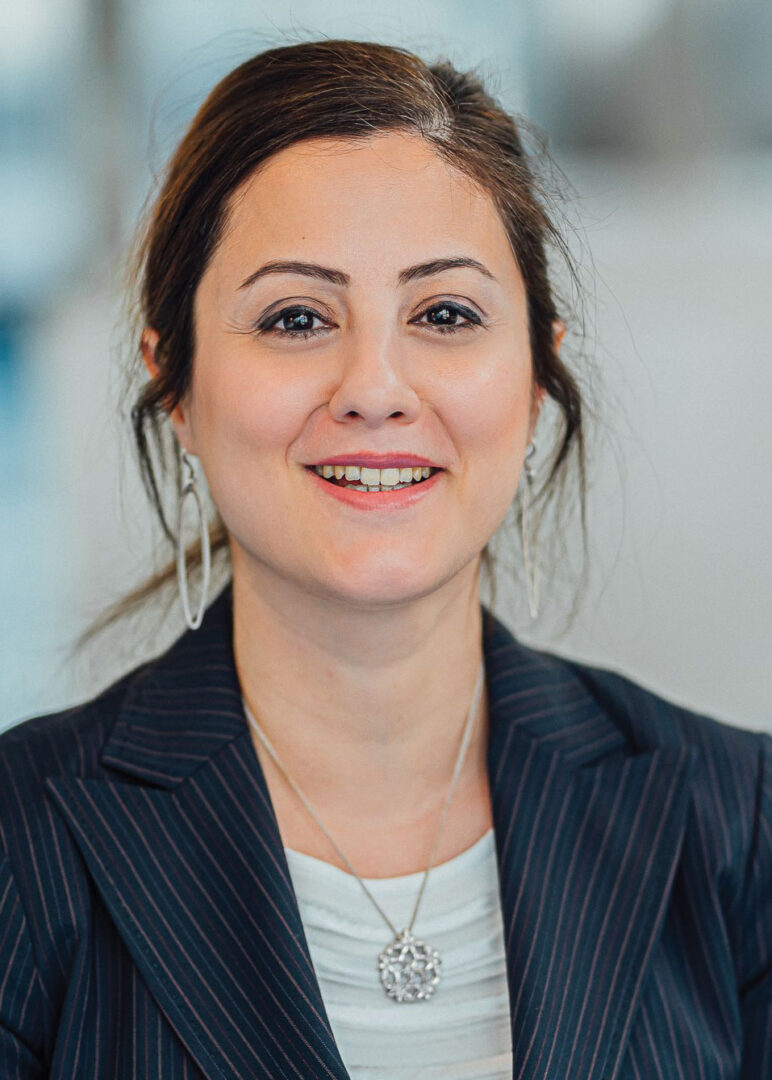
For example, the design details of many piles cannot be traced, and their length, mechanical properties and health condition cannot be accurately assessed using traditional methods. This poses significant risks to the safety and long-term durability of infrastructure. The good news is that flexural guided wave technology is an advanced non-destructive testing method that can overcome this challenge.
Compared to traditional methods, guided waves have stronger penetration ability and higher spatial resolution, which allows for a more comprehensive evaluation of piles through the propagation characteristics of the signals. Guided wave technology also has the advantages of being non-invasive and being more flexible for use on construction sites and, even in cases where access to the top of the pile is not possible, the technology can still effectively obtain important health information about the pile, especially for deep-buried or unknown piles that are difficult to detect using traditional methods.
“However, the exploration of guided wave models is not only about overcoming the limitations of traditional testing methods,” said Maghoul. “It is also about addressing the various challenges faced in current pile testing and promoting innovation and development in infrastructure testing technology.”
How guided wave technology works
Maghoul and her team achieve pile length estimation by analyzing the propagation – particularly the periodic pattern of guided waves propagating in the pile. They accomplished this by first converting the guided wave signals into the wavenumber domain and then analyzing the periodic patterns of the reflected waves in the wavenumber domain. By observing these patterns, the team can accurately estimate the length of the pile.
They also analyze the dispersion relation of flexural guided waves – the relationship between phase velocity and frequency – which delivers a forward modeling approach that allows for the measurement of the dispersion relation of the pile through resonance analysis methods. Based on this information, the team then combines the measured dispersion relation with the forward modeling approach and then inverts the mechanical properties of the pile – such as Young’s modulus and longitudinal wave velocity – using optimization algorithms.
“This method of combining the propagation characteristics of guided waves, dispersion relations and optimization algorithms not only estimates pile length, but also simultaneously provides the mechanical properties of the pile and offers us a comprehensive health assessment of the pile,” said Maghoul.
To achieve a more efficient pile assessment, researchers at Polytechnique Montréal developed two separate but complimentary acoustic data processing methods. The first method is based on dispersion analysis of guided waves. In this method, they convert the measured signals into the wavenumber domain using the dispersion relation of the guided waves propagating in the pile, which allows them to observe the periodic patterns of the reflected guided waves in the wavenumber domain. By identifying these patterns, an accurate estimate of pile length can be determined. The process of this method can be found in Figure 1.
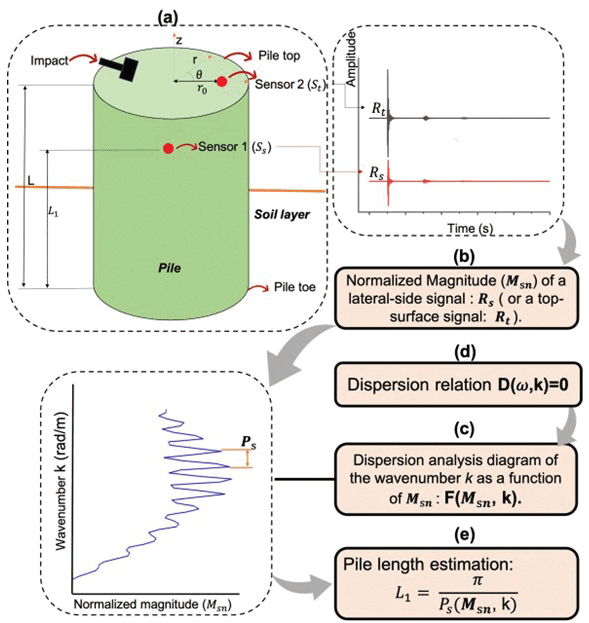
The second method is based on a combination of forward modelling and optimization algorithms. In this approach, Maghoul’s team combines the dispersion relation of flexural guided waves for forward modelling. Using resonance analysis methods, they then obtain the pile’s dispersion data and apply optimization algorithms to invert the mechanical properties of the pile. This method not only provides the geometric characteristics of the pile, but also simultaneously gives the mechanical parameters and offers a more comprehensive assessment. The schematic of this method can be found in Figure 2.
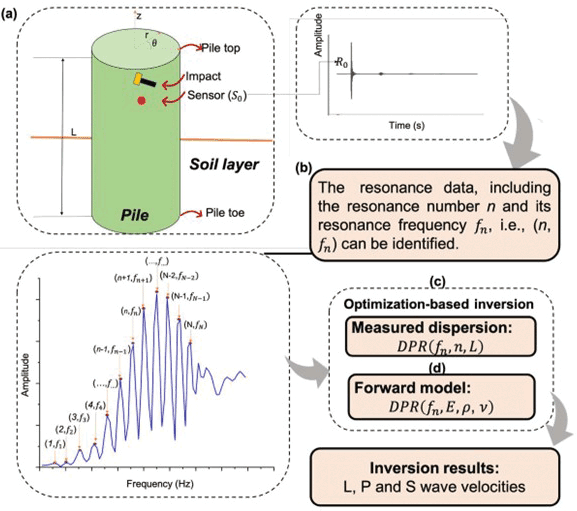
“These two methods complement each other,” said Maghoul. “By combining both methods, we can achieve a comprehensive assessment, from the pile’s geometric characteristics to its mechanical properties, as well as enhance the accuracy and reliability of pile health monitoring.”
Accuracy under various environmental conditions
Polytechnique Montréal’s innovative guided wave model is already demonstrating strong adaptability under different environmental conditions, including concrete, metal and wooden piles. The tests conducted by Maghoul and her team in these conditions have all yielded ideal results, proving the model’s broad applicability, even in underwater or high-vibration environments.
Although the propagation characteristics of water differ from soil, for underwater piles, the penetration capability of guided wave technology allows for effective monitoring and assessment, and the model is still able to accurately reflect the underwater pile’s geometric characteristics and mechanical properties. In addition, for high-vibration areas, the model can adapt to different vibration conditions using dispersion analysis and signal processing methods to effectively filter out noise, ensuring the accuracy of the test results.
“Whether in underwater environments or high-vibration areas, our guided wave model provides reliable assessments, ensuring the accuracy and practicality of pile health monitoring,” Maghoul said.
The future of guided wave technology
Looking ahead, the combination of guided wave sensing technology and artificial intelligence (AI) is set to completely transform the way pile health assessment and infrastructure maintenance are handled in the field of civil engineering.
AI has the potential to help engineers better understand and analyze the large amounts of collected data. In addition, innovations in machine learning and deep learning algorithms, will allow them to push AI further to extract more potential information from complex guided wave signals.
“Through big data analysis and AI models, we will be able to continuously optimize and update the assessment models to adapt to different environments and pile types, thereby providing more precise predictions,” said Maghoul. “For instance, through continuous monitoring, AI can automatically adjust the monitoring strategy and update the health assessment of piles based on real-time data and intelligent decision-making.”
As AI technology matures, it will inevitably lead to broader automation – from data acquisition to signal processing, to pile health assessment and maintenance recommendations – allowing the entire process to be automatically completed by intelligent systems, significantly reducing errors caused by human intervention, improving efficiency and mitigating costs. This level of automation will not only improve accuracy, but also greatly accelerate the data analysis process, allowing engineers to make critical decisions faster to proactively prevent potential problems.
“The combination of guided wave sensing technology and AI brings unprecedented innovative opportunities to the field of civil engineering, particularly in pile health monitoring, structural safety assessment and predictive maintenance,” said Maghoul. “In the future, I believe this technology will become a standard tool in civil engineering, greatly enhancing the safety, reliability and sustainability of infrastructure.”