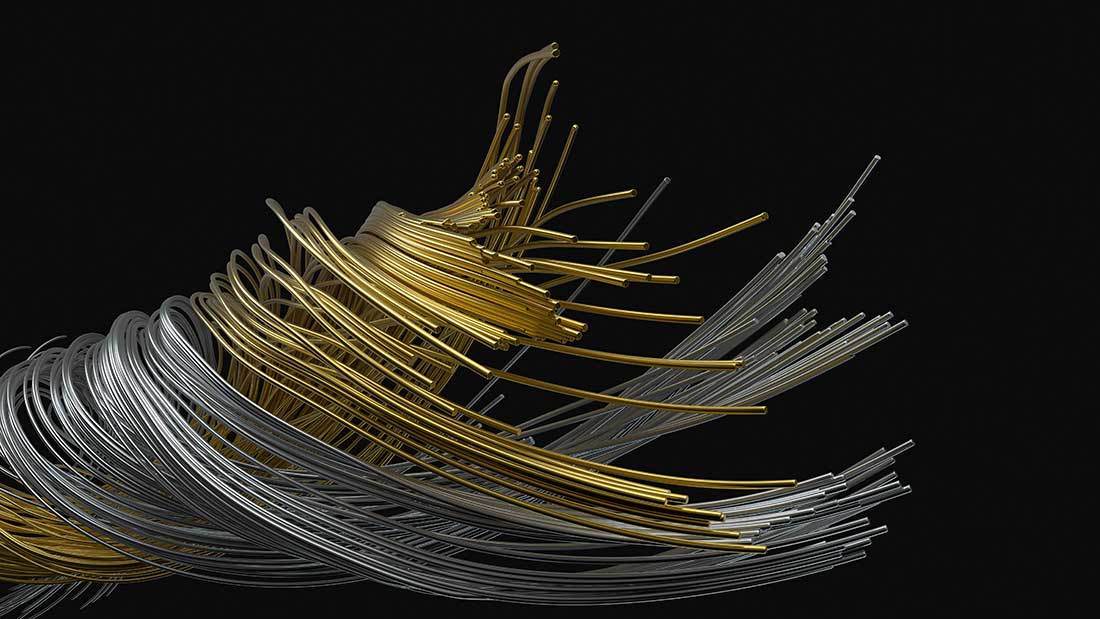
kasezo/123RF
The term “composite” indicates a combination of two materials or substances used to elevate and create a new product with superior properties compared to its original. To meet the requirements of today’s advanced superstructures and substructures, research and investment in new pile technologies are essential. Researchers found that traditional piles made of concrete, steel or timber have limited use, short service life and are challenging to maintain and replace (Lampo et al. 1998/1997). Therefore, the industry is shifting its focus to increase the use of composite piles, specially for off-shore and marine construction, due to its lower maintenance costs, composite properties and longer lifespan.
Composite piles were first used in the United States in the late 1980s (Heinz et al. 1993). The first composite pile prototype was a steel pipe encased by recycled plastic. There are several types of composite piles such as steel pipe core piles, concrete-filled fibre-reinforced polymer (FRP) pipe piles, structurally reinforced plastic matrix piles, fibreglass pultruded piles and plastic timber piles. However, due to a lack of performance data, advanced research, and material and tools availability, composite piles are still limited to specific uses. Generally, composite piles are designed to reduce maintenance costs and increase service life in harsh, sensitive environments, such as marine applications.
From 1987 to now, many projects like the Port of Los Angeles and the Port of New Jersey have used composite piles as fender piles due to their advantages over conventional piles.
Steel pipe core piles (Part 1 of Figure) consist of a recycled plastic cell as an outer layer and steel pipe in the centre core area. These piles can range up to 75 feet in length. The steel centre core serves as a structural strength element, while the plastic outer shell layers protect from external environmental substances. This type of pile is designed similarly to the conventional pile, so there is little need for further research and data collection.
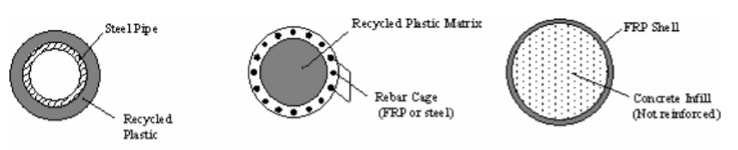
Common types of composite piles
FHWA-HRT-04-043 report
A structurally reinforced plastic matrix pile (Part 2 of Figure) consists of a recycled plastic matrix in the core with an FRP or welded steel rebar cage as the outer layer. Potential issues with this type of pile include debonding of the reinforcing FRP rods and high creep rates associated with the high polymeric content. Therefore, to date, these piles have been used only as fender piles.
Concrete-filled FRP tube pile (Part 3 of Figure) is the most commonly used composite pile in recent history. It consists of a concrete centre infill without steel reinforcement and an FRP shell. These piles can be installed by driving the empty FRP shell and filling it with concrete. Also, they can be installed by filling the pile with concrete and driving it after the concrete is cured. In the U.S., Hardcore Composites and Lancaster Composite are major manufacturers of these piles.
There are limited research data available for these common types of piles, and further research is carried out by the U.S. Department of Transportation’s Federal Highway Administration and pile manufacturers to understand long-term durability, freeze-thaw cycle and geotechnical behaviour, and to develop an uncomplicated design process.
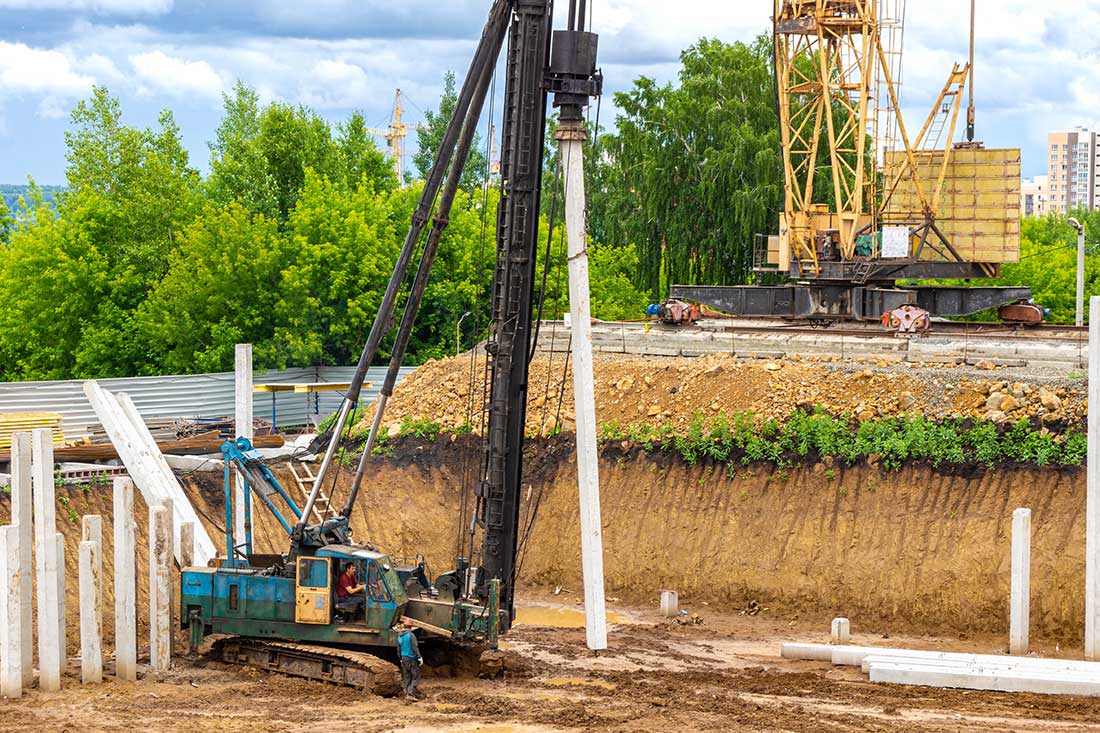
dkorostilev78/123RF
In 2000, the Virginia Department of Transportation (VDOT) considered concrete-filled FRP composite piles to rebuild a new bridge on Route 40 over the Nottoway River in Sussex County. This pile program aimed to understand the drivability, axial-lateral load capacity and long-term interaction to moving load and geotechnical strata. Composite piles were compared against the common prestressed concrete piles. Based on test programs, analysis and construction practices, composite and prestressed concrete piles performed similarly under axial load, field tests and lateral load. Beyond specific lateral loads, composite piles demonstrated lower stiffness, but resisted it with larger deformations. The composite piles were determined to fail in bending by cracking of glass fibre reinforced polymer tube into tension.
A similar test program was conducted to understand the performance of composite piles at another VDOT bridge project located on Route 351. The test demonstrated similar results as the bridge on Route 40. Field and analytical test results indicated that conventional pile design, conventional T-Z curves, driving installation and theoretical load transfer curves can be used for composite pile design criteria. However, the initial cost estimation was much higher than traditional prestressed concrete piles for these projects. The cost-effectiveness of composite piles can be measured with mass production, low maintenance and longer life cycles.
The composite piles can become a game-changer system in the future geotechnical industry.
In conclusion, composite piles are a viable option with an extensive field test-monitoring program. The composite piles can become a game-changer system in the future geotechnical industry. However, durability studies, geotechnical studies and long-term maintenance programs should be considered for further evaluation.