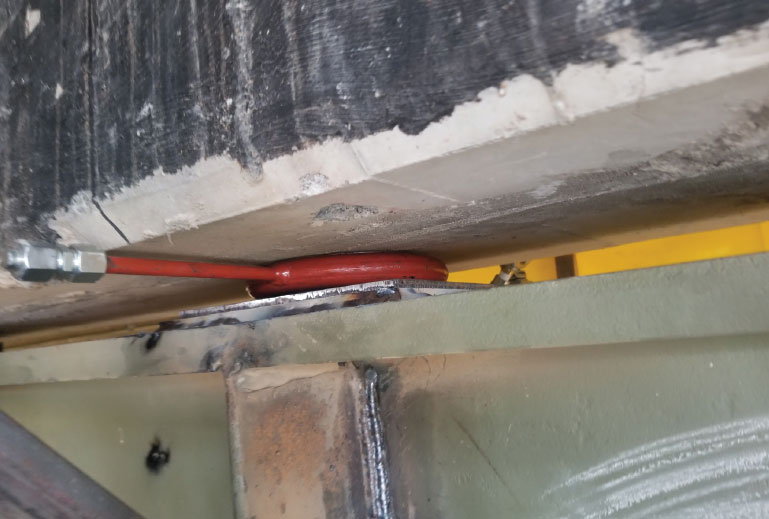
The expansion of its primary maintenance facility last year was made possible with the use of flat jacks
The Fort Rouge Transit Garage is Winnipeg Transit’s central and primary maintenance and repair facility, handling the majority of the total upkeep for the city’s transit fleet. Built in 1969, Fort Rouge Garage was considered state-of-the-art; the Storage Garage features a special drive-through wash bay, as well as additional areas to check oil, water, tires and lights of each bus after the day’s run. A separate maintenance and repair building also handles scheduled maintenance inspections and major repairs.
Now more than a half-century old, the original buildings at the facility could no longer handle the capacity required of a larger bus fleet. Therefore, the City of Winnipeg made the decision back in 2016 to expand the Maintenance and Repair Garage to better meet current and future needs, in addition to keep up with a vehicle fleet that had grown considerably in the decades since the facility was built.
In July 2017, PCL Constructors of Canada was selected to become the design-builder for the Winnipeg Transit Bus Maintenance Garage Expansion Project. Located next to the recently constructed Brandon Avenue Storage garage, this 72,000 square foot expansion project was finished in June 2019; greatly increasing the facility’s floor space from 113,000 to 185,000 square feet, while also improving upon the already impressive capabilities of the existing facilities.
“The Fort Rouge Garage has the ability to take a bus all the way down to the frame and then re-build it from scratch, but now with additional space to do so,” said Kyle Park, project coordinator at PCL Constructors Canada Inc. “You can accomplish pretty much anything you can think of at this facility, from upholstery and sheet metal, to diesel engine maintenance to electronics; just name it and they can make it happen. And their cafeteria is pretty good too.”
The new expansion is essentially a large open space comparable to a warehouse-style building, with just a few columns running down the middle of the building. The project included the construction of a number of new service bays, featuring in-ground hoists for mechanics similar to what you might find at a regular mechanic’s garage, but built to a larger scale that allows for servicing the different models of buses used by Winnipeg Transit. The expansion also included additional shops area (including welding facilities) and a paint shop with preparation and paint booths large enough to accommodate full-sized transit buses.
As building codes have evolved over time, the requirements for snow loading also increase. That meant PCL needed to provide underpinning piles to help support the existing building’s foundation, as well as accommodate the new roof loads that were imposed on that existing facility’s structure.
“Fortunately, however, mostly everything related to the underpinning was pretty standard for a building project of this type,” said Park. “The piling trades here in Winnipeg are really good at working in close proximity to existing buildings and the piling contractor we had on site, Preset Piling Inc., did an amazing job.”
One of the more unique aspects of this project – particularly for PCL – was in the use of flat jacks that were supplied by WB Equipment Service Corp., based out of New Jersey. For 41 years, WB Equipment has been in the business of designing and providing equipment for all types of jacking operations. Their flat jacks have found use on projects of all sizes throughout the U.S. and Canada, such as the stadiums of the NFL’s New England Patriots and Baltimore Ravens, the San Francisco Central Subway and the Philadelphia Museum of Art.
“The flat jack was specifically made for areas that have very little clearance,” said Stephen Cireco, president at WB Equipment. “When deflated, the jacks are only 1.3 inches tall so, in tight spaces, they have proven to be extremely useful. And, unlike normal hydraulic jacks, these jacks also have the ability to become a permanent part of your structure.”
When installing the underpinning piles, PCL would pour a cast-in-place pile next to the existing building foundation. The cast-in-place pile would then have a concrete pile cap on top that was engineered to a very specific shape in order to reach under the existing building foundation, leaving a narrow space between the top of the pile cap and the underside of the existing foundation. The flat jacks were then placed at strategic locations inside the gap to ensure there wasn’t any sinkage when the roof load was transferred from the existing building foundation to the new underpinning piles.
The flat jacks were then filled with epoxy grout up to a precise amount of pressure that translated to a specific amount of force pushing outward on the exterior surface of the bag, which then corresponded to a certain weight on the new underpinning pile. The remaining space between the underpinning pile and the foundation was then grouted solid.
“The flat jack is basically a metal balloon that sits in between two objects,” said Park. “You fill the flat jack up with liquid grout to a certain level, tie off both ends of the ‘balloon’ and – over the course of 24 hours – the grout that’s inside the flat jack will harden and become a completely solid object.”
As is common with the unfamiliar, there is a natural tendency to be hesitant when using something new. As such, flat jacks were not the first technology PCL considered. The company explored a number of different options before choosing flat jacks, such as the use of steel plates or hydraulic jacks that could temporarily pre-load the underpinning piles as the space between the new underpinning piles and the existing foundation was grouted.
“To be honest, since I had never worked with flat jacks before, I looked into a number of different options instead of using them,” said Park. “But in terms of the actual work that took place on site, it ended up being very easy to use the flat jacks and I know that if I were to ever run into a similar situation, I would use them again in a heartbeat. Flat jacks were far and above the most economical solution in providing the pre-loading detail we required.”
The pile cap on PCL’s cast-in-place piles is wider than the pile itself and, when installing the flat jack, it was critical that the jack be placed on the centre line of the pile so the force from above would be transferred directly onto the pile. One of the unforeseen challenges for the project was that the pressure gauge on the flat jack was positioned in such a way that the jack could not be placed on the pile cap’s centre line.
Fortunately – with the blessing of the WB Equipment supervisor on site – the solution was to simply remove the gauge and flip it around to a different orientation to allow PCL the ability to reposition the flat jack a couple of inches over, along the centre line.
“It really just meant that some creative and collaborative engineering needed [to] be used to get that thing to fit exactly where it was supposed to go,” said Park. “But it goes to show that even on large buildings of thousands of square feet, every single inch or two has the potential to affect the success of a project or impact the performance of the building.”
PCL recognizes that its most valuable asset is its employees and, as such, the creation of a safe and healthy work environment is one of the organization’s most central guiding principles. PCL refuses to compromise on the safety of its people and its safety program raises the bar for the construction industry as it strives to achieve zero safety incidents throughout the course of each and every one of its projects.
PCL’s Safety Observation System teaches employees to recognize and eliminate hazards and dangerous conditions by correcting unsafe behaviour through positive coaching. The company also makes its policies, procedures, guidelines and practices for performing work safely readily available for all its employees through the use of its comprehensive health, safety and environment manuals.
“We will hold extensive safety orientations with all of our projects, along with daily pre-job safety inspection that we renew at every break,” said Park. “As the work changes for each activity we do over the course of a project, we will provide additional jobsite-specific Health, Safety and Environment Operating Procedures (HSEOP). Whether it is for cast-in-place piles, pre-cast piles, pile cap forming or excavation, each one of the tasks we undertake will have its own particular HSEOP.”
Although the LEED® certification process is still underway, it is expected that the new expansion will achieve at least LEED® Silver certification through the Canada Green Building Council, clearly demonstrating the sustainable approach that was taken in the design, construction and current operation of the building
“Winnipeg Transit is a 24/7, 365 days a year operation and it is an essential service for a lot of Winnipeggers in getting from Point A to Point B across the city,” said Park. “To say that this project has been a feather in my cap would be a tremendous understatement. It’s been a privilege to play even a small role in helping Transit provide this service, and this project has proven to be a phenomenal opportunity for both myself and PCL.”
-
CZM Foundation Equipment introduces CZM Capital Financing options for customers
April 25, 2024 -
Student Engagement Committee
April 25, 2024 -
DFI announces two new committees
April 25, 2024 -
Keller’s John Wolosick and Allen Sehn receive awards at the 2024 Geo-Institute’s Geo-Congress
April 25, 2024 -
Rod Kern appointed as vice president of Equipment Corporation of America
April 25, 2024