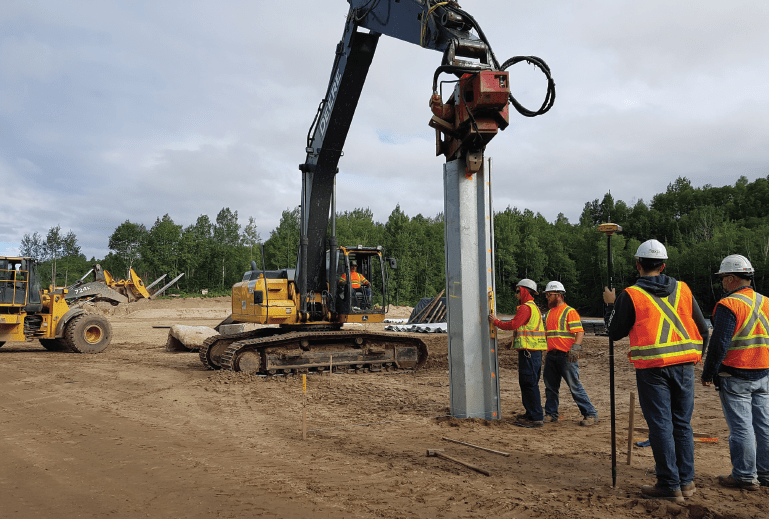
At a historic airbase in Newfoundland and Labrador, a unique environmental containment system called the Waterloo Barrier® is being used to entomb decades of domestic and industrial waste
By Mark Halsall
The Goose Bay Remediation Project is a multi-year, multi-million-dollar environmental program for the Department of National Defence. It is centred around a storied Second World War airbase in Newfoundland and Labrador known as 5 Wing Goose Bay.
One of the remediation contracts at 5 Wing Goose Bay, which was built in 1941 and is still in use, involves cleaning up an old dump used by the base that’s located near the remote community of Happy Valley-Goose Bay in central Labrador.
Over the years, various waste materials including domestic garbage, construction debris, barrels containing a range of products (fuels, lubricating materials, pesticides, etc.) and even discarded heavy equipment have piled up at the site.
The solution was to enclose the waste and potentially contaminated materials within a massive containment cell.
The cell, which measures 108 metres wide by 115 metres long and ranges between four to 10 metres below grade was built two years ago. The total cost of this part of the project, which included an engineered cap over the cell, totalled approximately $1.5 million.
C3 Environmental Limited, an environmental engineering and contracting firm based in Breslau, Ont., played a key role in the remediation effort, assisting with the project design and providing a unique solution known as the Waterloo Barrier® System that was used to encase the waste.
According to Minh Le, president of C3 Environmental, the containment cell was constructed to essentially entomb waste that was buried at the site and prevent it – along with impacted groundwater – from migrating into the surrounding environment. Waste at the surface and at shallow depths was removed and disposed of at a licenced landfill prior to construction of the containment cell.
“A major advantage of the Waterloo Barrier® is that excavation of subsurface materials is not required, thus there is less damage to the site and disruption of normal site activities,” Le said, adding that the high costs associated with the health and safety precautions that are required to excavate and dispose of contaminated material were also avoided.
Watertight system
The Waterloo Barrier® is comprised of interlocking steel piles that incorporate a unique sealable joint system which makes the system virtually watertight – an essential consideration for the 5 Wing Goose Bay project.
According to Le, conventional steel sheet piling is seldom used in environmental applications due to an unacceptable amount of leakage through the interlocking joints.
In the Waterloo Barrier® System, the interlocking joints incorporate a cavity that’s created by cold roll forming in the sheet pile manufacturing process. Le explains that a footplate at the bottom of each cavity displaces soil laterally as the sheets are driven into the ground, allowing the joints to remain largely soil free.
“Soil that does enter the joints is relatively loose and easily removed by jetting with water,” he said, adding that epoxy, cement or clay-based grout is then injected into the sealable cavities between the sheet piles to create a low permeability barrier.
Le notes that the Waterloo Barrier® is the only system where the joint sealant is placed after the sheet piling has been driven and is in the ground.
Le says a number of different watertight sealants particularly resistant to chemical degradation are used in the process and that because the volume of required sealant is relatively small, they’re economical to use.
For the 5 Wing Goose Bay project, C3 Environmental was contracted by Quebec firm Loiselle Environment to supply the Waterloo Barrier® materials as well as perform the quality assurance and control inspection and sealant installation services during construction.
According to Le, Loiselle Environment used a typical set and drive procedure to install the sheet piles provided by C3 Environmental.
Le says due to the nature of the landfill area, piling workers had to deal with various obstacles that included tree trunks, metal drums, tires, vehicle parts and heavy equipment.
He adds that differing soil conditions were also encountered at the site, which meant different equipment set-ups were required during pile driving.
An excavator-mounted vibratory hammer/extractor was used to install most of the sheets, says Le, while in a few areas where soil obstructions were encountered, a set-up using an HPSI 300 XL Vibratory Hammer and a Link-Belt HSP Rough Terrain Crane was put in place.
“Once the sheet piles were installed, the sealable joints were cleaned and inspected to confirm that they were not separated or damaged. Subsequently, C3 sealed each joint with a cementitious based grout from bottom to top using injection line.” Le said. “The line was inserted to the bottom of each joint facilitating the emplacement of sealant into the entire length of the joint.”
A total of 656 galvanized steel sheets, including four corner sections, were driven for the containment cell. Following its completion, the structure was covered with an engineered cap to minimize the amount of precipitation infiltrating the cell. This cap is three-quarters of a metre thick and is comprised of geosynthetic clay cap, granular materials, topsoil and vegetation.
Hundred-year lifespan
Throughout construction, the integrity of the containment cell structure was confirmed by regular inspections by C3 Environmental personnel. Le says the company’s rigorous quality assurance and control program enables C3 to offer an excellent performance warranty on Waterloo Barrier® Systems for one year after the installation. However, he adds that the normal lifespan of a typical Waterloo Barrier® System has been estimated in excess of 100 years for underground applications.
Le says the remote location of the containment cell was one of the biggest challenges for those involved in the the 5 Wing Goose Bay project.
“It was difficult to obtain the required sheet pile driving equipment and services, [and] when the operation required parts and repair services for the rare equipment breakdowns, parts had to be flown in from St. John’s, Newfoundland, or larger cities,” said Le. “Specialty labour resources also had to be flown in from other cities as well.”
The site is situated on a migratory bird flightpath, so the containment cell also had to be completed on a compressed schedule to avoid the primary migratory period and harsh winter weather.
Le notes that one of the unique aspects of the project was an engineered wetland that was put in place following completion of the containment cell. The wetland was designed to provide passive treatment of potential contaminants discharging to surface water in the area of the Waterloo Barrier® System, he says, thereby helping to protect various potentially sensitive ecological species that inhabit the area.
-
CZM Foundation Equipment introduces CZM Capital Financing options for customers
April 25, 2024 -
Student Engagement Committee
April 25, 2024 -
DFI announces two new committees
April 25, 2024 -
Keller’s John Wolosick and Allen Sehn receive awards at the 2024 Geo-Institute’s Geo-Congress
April 25, 2024 -
Rod Kern appointed as vice president of Equipment Corporation of America
April 25, 2024