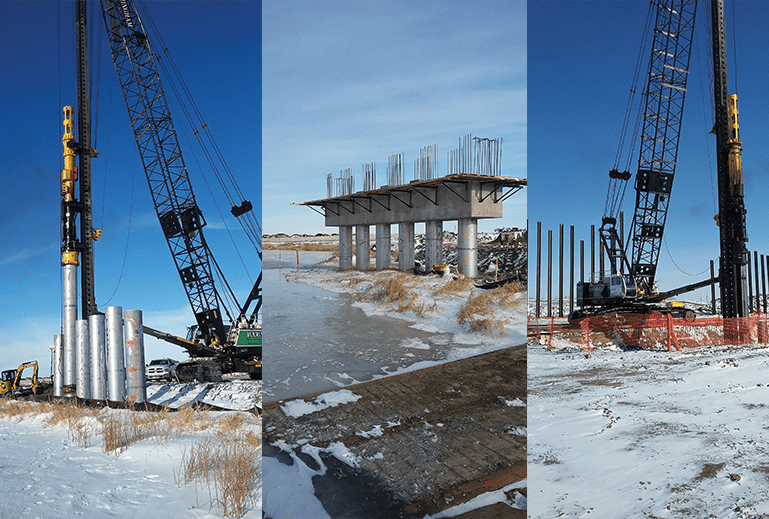
With a price tag of almost $2 billion, the Regina Bypass is the largest single infrastructure project in the history of Saskatchewan.
The new urban bypass route connects the Trans-Canada Highway with Highway 11, the province’s main north-south corridor that links Regina with Saskatoon, and in addition to relieving traffic congestion, it’s expected to make a vital contribution to the continued growth and prosperity of Saskatchewan.
The Regina Bypass project is being undertaken as a public-private joint venture and the Province of Saskatchewan is footing much of the bill, which includes a construction budget of $1.2 billion. The design-build consortium that’s managing construction includes the Saskatchewan Ministry of Highways and Infrastructure as well Vinci Infrastructure Canada Ltd., Carmacks Enterprises Ltd., Graham Infrastructure LP and Parsons Canada Ltd.
Work on the Regina Bypass began in 2015 and is scheduled for completion in 2019. Due to the size of the project, construction has been split into three zones, with Area 1 to the north, Area 2 to the south and Area 3 to the east of the City of Regina. The full scope of the project includes 40 kilometres of new four-lane highway, 20 kilometres of resurfaced four-lane highway, 55 kilometres of new service roads and dozens of highway overpasses.
To complete the extensive bridge construction required for the project, the Regina Bypass consortium has relied on the expertise of Bermingham Foundation Solutions to perform much of the piling work. The Hamilton, Ontario-based company performed the deep foundation work needed for 14 bridge structures in Areas 1 and 2, starting in late 2016 and ending in November 2017.
“This was definitely a good-sized piling project,” said Brian Abele, construction manager for Bermingham Foundation Solutions. His company was originally contracted to drive piles for eight bridge structures, but six more were later added. “Those [foundations] were tentatively scheduled to be drilled caissons and then they changed it to piling based on their geotechnical investigation,” said Abele, adding that Bermingham’s performance on the jobsite also factored into the decision.
“We had one four-man crew that [worked] continuously, and we just kept sequencing from bridge to bridge and it worked very efficiently. We were satisfying the owners’ requirements for schedule, so I think that was one of the reasons to go to the piling alternate for those other structures as well,” Abele said. “It’s a testament to our personnel that their performance was definitely a factor in helping us procure more work.”
Abele says it’s also a credit to the Bermingham crew that they were able to power through their work on the Regina Bypass project during a cold Saskatchewan winter in 2016-17 without any weather-related stoppages.
“Going in, we weren’t guaranteeing that we would work through the winter. It was all going to be weather dependent, and if the conditions were warranted to halt then we were going to do that and then return in the spring,” Abele said.
“The conditions were bad, but they weren’t intolerable, so we continued driving through the coldest temperatures. That actually gained the client a little bit of schedule… because everyone was expecting that we were going to shut down for some of the winter season,” he said. “We worked right through the winter and that was a testament to our crew. They worked extremely diligently.”
Large capacity crane used
In total, Abele says, about 600 piles were driven for the 14 bridge structures, most of them 14-inch H-piles in various sizes. Some 30 inch by three-quarter inch pipe piles were also installed. The piles were sourced from various companies, including Dominion Pipe and Piling, Samuel Roll Form Group and Pipe and Piling Supplies Ltd. All of the piles were installed using a Bermingham L-23 vertical travel lead system with a Terex HC 165 crawler crane.
“We used a big 165-ton crane, which was probably a little bit more than what would typically be needed on a piling job like this, but we wanted to be able to drive the majority of piles in single lengths. The requirement then was to have a fairly long lead with a large capacity crane,” said Abele. “We went up to 130 feet and drove up to 115-foot-long piles in a couple of locations.”
During the project, a Berminghammer B-5505 diesel hammer was used to install the H-piles and Berminghammer B-64 diesel hammer was used to drive the pipe piles. “We only had the one rig, so we switched when we had to,” Abele said. He adds that noise wasn’t a concern during the pile driving process. “Generally, it was all greenfield construction, other than along the highways, so we were okay from that perspective.”
Abele notes that the soil conditions encountered by the Bermingham crew during construction were fairly consistent, but it did vary from site to site.
“In some cases, it was relatively easy driving… but it was extremely hard driving for a few of the bridges. We had an extremely hard layer that was above the intended toe [in those instances], so we had to work with the geotechnical consultants on the job just to ensure that they were happy with capacity of the piles.”
Abele says environmental precautions were also required in some instances where the bridge building took place close to an adjacent waterway, Wascana Creek. “We had to make sure that we had spill containment and that kind of thing. That was paramount, especially in certain areas,” he said.
Abele notes the Bermingham crew also needed to be mindful of all the other road building activities going on at the same time as the pile driving. “That was one of the things that we kind of had to be cognizant of and work with the client to ensure that a reasonable degree of separation and that everybody was aware of adjacent construction activities,” he said.
Abele maintains that Bermingham’s commitment to safety and careful planning were key factors behind the company’s successful piling bid on the Regina Bypass project.
“One of the reasons why we were a preferred subcontractor is because of our safety record and our procedures. We had written procedures for everything and plans for mobilizing from site to site, and we adhered to those plans and always conveyed our progress with the owner,” he said.
Abele states a good example is the care the Bermingham crew took when they were required to do some pile splicing. “We had areas that we set up for splice beds, and that was definitely [a] more efficient and safer way of working to move the large piles for splicing,” he said.