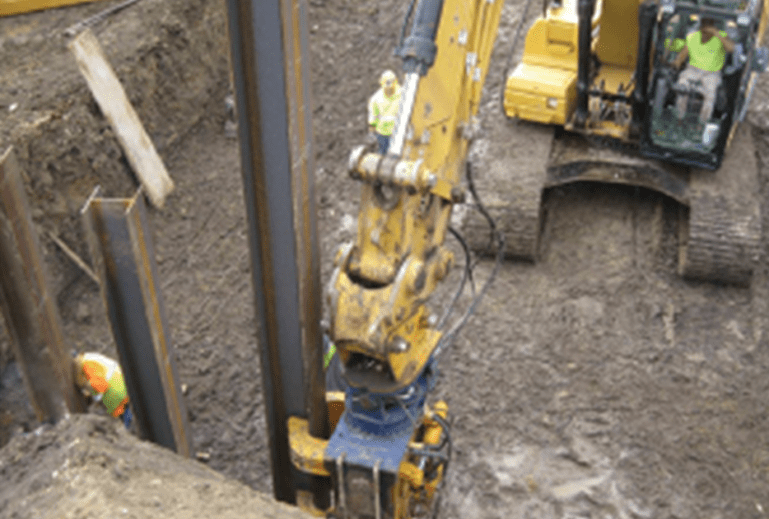
Hercules Machinery. Revolutionizing worksites since 1998
Hercules Machinery introduced the first side-grip in the industry 17 years ago and since then has perfected the Movax® Sonic SideGrip®, placing more than 500 units at worksites throughout the U.S. and Canada. An excavator-mounted attachment, this vibratory pile driver features an articulating side-grip with two unique side-gripping jaws and one bottom jaw that deliver unmatched dexterity when handling, driving or extracting nearly any style of piling.
Designed to deliver the utmost efficiency, the Movax Sonic SideGrip can not only drive piles up to 50 feet, but it also reduces the amount of peripheral equipment needed, like cranes, loaders and manlifts. It uses an excavator’s hydraulics to safely and quickly pick up, unload, place, drive and extract piling. With the most advanced auto steering system avail-able, the Movax Sonic SideGrip precisely drives pile at 3,000 vibrations per minute. Its superior maneuverability means the Movax Sonic SideGrip can expertly handle challenging worksites with low overhead or narrow passageways.
“We use the Sonic SideGrip a lot in pits and in buildings where we don’t have the headroom clearance,” said Patrick Kirchner, vice president of Force Construction. “It performs well for us every time.”
Movax® Sonic SideGrip® from Hercules Machinery
- Available in five models from 40 to 100 tons of drive force
- Available in five models from 40 to 100 tons of drive force
- SP100 model is the most powerful side grip in the industry
- Auto II steering controls assuring straight and plumb piles
- 3,000 vibrations per minute• Environmentally friendly
- Able to drive sheet pile, H-pile, timber and pipe pile
- Drives piles up to 50 feet
- Operates from the auxiliary system of the excavator
- Manufactured in the USA
Equipment Corporation of America hires Gordian Ulrich as engineering sales manager
Equipment Corporation of America (ECA) has hired Gordian Ulrich as engineering sales manager. He will be responsible for BAUER technical applications and advancement of its available technology in the Eastern United States and Canada.Equipment Corporation of America (ECA) has hired Gordian Ulrich as engineering sales manager. He will be responsible for BAUER technical applications and advancement of its available technology in the Eastern United States and Canada.
Ulrich graduated from the globally renowned Karlsruhe Institute of Technology (Fredericiana) in Germany. He studied geotechnical engineering while working at his father’s consulting company. In 2007, he joined BAUER Maschinen Germany. Over the next seven years he travelled worldwide for BAUER, doing start-ups, providing training and consulting for customers and salespeople. Ulrich and his family moved to Canada to work for ECA following the arrival of their first child. In 2007, he joined BAUER Maschinen Germany. Over the next seven years he travelled worldwide for BAUER, doing start-ups, providing training and consulting for customers and salespeople.
“Gordian has an exceptional handle on BAUER machinery and will bring that expertise to ECA customers,” said ECA’s executive vice president, Ben Dutton. “His technical background and field experience will enhance equipment applications for our diverse BAUER product line.”
Construction project failures weigh on industry Construction project failures weigh on industry despite advances in planning and controls
Over half of construction project owners experienced one or more underperforming projects in the previous year, despite confidence in project planning and controls, according to KPMG International’s 2015 Global Construction Project Owner’s Survey: Climbing the Curve. Further, project owners said only 31 per cent of their projects came within 10 per cent of budget, and just 25 per cent within 10 per cent of original deadlines in the past three years.
“As engineering and construction projects get bigger, the complexity grows exponentially,” said Geno Armstrong, global chair, Engineering & Construction and a principal with KPMG in the U.S. “The improvements by owners in planning and risk management have been significant, yet there is further work to be done to reduce the number of project failures, and bring more projects in on time and on budget.”
Greater emphasis on planning and prioritizing
While rates of underperforming projects are troublesome, KPMG’s survey shows that owners of major capital projects are implementing more mature planning and approval processes, with 84 per cent reporting that their company screens projects using both financial and risk analysis, and 74 percent of firms requiring formal project delivery and contract strategy analysis, prior to authorization.
Project owners surveyed also expressed confidence in their approach to risk, controls and governance. Sixty-four percent say their management controls are either “optimized” or “monitored,” and almost three-quarters feel comfortable with the accuracy and timeliness of project level reports. More than half also indicate that they are either “satisfied” or “mostly satisfied” with the return on investment in project management tools and training.
“As engineering and construction projects get bigger, the complexity grows exponentially.”
Geno Armstrong, Global Chair, Engineering & Construction, KPMG
“Over the past decade, owners have introduced software to improve project controls, with some positive results,” said Armstrong. “But at the same time, our research found only half of companies have project management information systems that raise the quality of decision-making in each phase of the project life cycle – which suggests there is considerable room for improvement.”
“And it’s not just the quality of the controls,” said Armstrong, “You also need to develop the skills of those managing the projects and using the various tools. Across the board, there is a critical need for more skilled talent.”
A push for greater contractor collaboration
KPMG’s survey also puts the owner/contractor relationship under the spotlight, revealing a thirst for closer working ties, with 82 per cent of respondents expecting to see greater collaboration with contractors in the next five years. However, there still appears to be a “trust gap,” with only about a third claiming to have a “high level of trust” in their contractors. Indeed, 69 per cent identify poor contractor performance as the biggest reason for project underperformance.